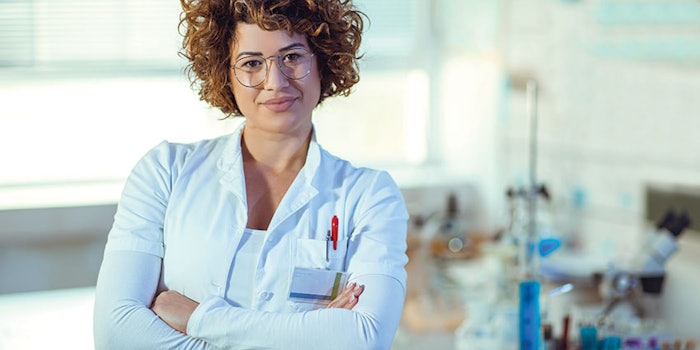
Read this article in its entirety in the September 2020 digital edition. . .
Throughout the duration of this hair testing column, I have described and highlighted commonly used approaches for evaluating the properties of hair and how these experiments might be used to assess the effects of products, ingredients and various insults. There are no “standard” methods in our industry but the widespread use and acceptance of the described techniques have established them as “best practices.” These approaches are found in most hair testing laboratories around the globe, and hair scientists will be familiar with seeing such results in the scientific literature, technical presentations, patents, claim substantiation packets, etc.
With this said, the right tool is needed for the right job and I have been periodically contacted with requests to provide information and guidance on the specifics concerning the equipment used in hair testing. The purpose of the current article is, therefore, to focus specifically on scientific instrumentation and provide guidance for those looking to set up, expand or update a hair testing laboratory. Where appropriate, I also draw attention to further considerations that allow for the generation of quality data.
Instrumental Combing Experiments
The fundamental technical function of conditioning products and ingredients is to provide surface lubrication in an aesthetically pleasing manner.1 This delivers improved tactile properties and easier maintenance since detangling and grooming are facilitated. The outcome also prompts consumers to herald other perceived improvements in hair’s qualities—such as feeling smoother, softer, less damaged, etc.—and even stronger and more moisturized.2
A highly consumer-relevant means of assessing this lubrication is to measure the friction associated with hair grooming in a so-called instrumental combing experiment. Indeed, the fundamental nature of this experiment, in association with the broad range of claims it supports, likely makes it the single most widely performed instrumental test in our industry. The classic reference to this approach was described by Garcia and Diaz in 1976.3 In relation, an earlier column in this series1 more specifically discussed the experimental details and nuances of this approach, while also speaking to data interpretation and subsequent product or ingredient communication strategies.
Briefly, this methodology necessitates a vertically aligned mechanical testing device whereby a hair tress can hang freely. Figure 1 shows the experimental setup from the author’s laboratory, whereby pneumatic fingers anchor the hair tress to a load cell. In this set-up, the load cell is attached to the instrument’s crosshead and the hair is pulled through a stationary comb whereby frictional forces are measured. Alternatively, the hair might remain stationary while the comb is moved and/or the comb might be attached to the load cell rather than to the hair. In large part, the specifics of this setup will be dictated by the available equipment.
For many years, this approach was commonly referred to as the Instron combing experiment because, at the time, Instron Corp.4 was the largest and best-known manufacturer of such mechanical testing equipment. Today, other companies such as Dia-stron Ltd.5 and Stable Micro Systems6 sell suitable bench-top instruments while providing specialized attachments for appropriately anchoring and positioning a comb on the equipment.
Single Fiber Tensile Properties
The tensile properties of hair are reflective of its inner structure, so their measurement provides a probe into activities occurring therein. Hair’s strength is compromised by a wide variety of insults7 and so this test is often considered a primary measure of hair “damage.” A previous column outlined how constant extension rate experiments are widely used to generate stress-strain curves from which a range of mechanical variables can be extracted to provide characterization.8 In principle, such experiments can be performed using the mechanical devices described above—but interpretation of the data can be hugely complicated by the high variability associated with single hair fibers. Overcoming this problem necessitates running a high number of replicate samples, which would be arduous, repetitive and lengthy on the aforementioned equipment.
In the early 1990s, Dia-stron Ltd.5 introduced a fully automated means of performing this testing; the newest iteration of this instrument is shown in Figure 2. A sample carousel is used to house individual test fiber samples that are precisely prepared using a supplied crimping press and block. The instrument can then be programmed to automatically measure dimensions for all samples and subsequently stretch each out to break. In this way, suitably high numbers of replicate fibers can easily be tested to ensure appropriate statistical rigor.
The convenience associated with this automated equipment has made it a staple in virtually all hair testing laboratories and establishes it as the closest our industry has to a standard. Fiber dimension measurements are performed beforehand to normalize out sample size effects and report, for example, a break stress (i.e., force per unit area) as opposed to a break force.8 The laser micrometer functionality can also be used in a stand-alone manner for accurately investigating hair fiber dimensions. Similarly, the crimping block and press provide a convenient means of preparing, managing and handling single fibers for all types of other experiments.
Single Fiber Fatigue Testing
Perhaps the hottest new hair testing technique of the last 10 years has been the single fiber fatigue experiment as an alternate means of investigating hair breakage. Commercial equipment is again sold by Dia-stron Ltd. This approach has been an ongoing focus of this author’s research and new insights have been described in past articles.9-11 By this approach, individual hair fibers are subjected to repeated smaller deformations as opposed to the one-time catastrophic deformation of the conventional tensile approach described above. The instrument tracks the number of repeating cycles of a predefined stimulus that are required to induce breakage. As before, multiple replicate samples can be tested in a fully automated manner to facilitate data production.
One driver for the method’s newly acquired popularity has been that it almost always gives rise to larger differences between samples than the traditional tensile approach. For instance, a 10% decrease in hair break stress by traditional stress-strain testing might translate to a tenfold difference in the number of cycles to fail under a given condition. Even more useful might be the recognition of the profound impact of previously unrecognized factors on breakage.
The biggest drawback of the approach can be the time required to perform these experiments, wherein the testing of a suitable number of replicate samples under specific conditions can take days (and even weeks). To address this issue, the manufacturer can add additional test stations to the instrument (see Figure 3), although with a commensurate increase in price.
This testing similarly requires the knowledge of hair fiber dimensions. A laser micrometer can be incorporated into the equipment but in many instances, the testing laboratory will already possess the traditional instrument described above, so dimensions can be suitably acquired and transferred.
Dia-stron Ltd. specializes in the testing of fibrous materials and further sells devices for measuring both bending and torsional stiffness. At present, these applications have not found widespread use in our industry but have the potential to yield further fundamental knowledge on hair’s structure and its interaction with products and ingredients.12
Hair’s Technical Water Content
It has been suggested that water should be considered part of the hair’s fundamental structure due to the profound effect it has on fiber properties.13 The primary factor in dictating hair’s water content is the relative humidity of the surrounding atmosphere and this relationship is given via the hair water adsorption isotherm.14 Experiments to ascertain this relationship are usually performed by gravimetric means, whereby the hair is weighed after equilibration under systematically varied humidity conditions.
These experiments can also be lengthy since considerable time is needed for hair’s water content to equilibrate at any condition. This duration is further exacerbated by larger sample sizes. This again prompts the need for automation, and modern-day equipment for performing such a test is referred to as Dynamic Vapor Sorption (DVS).
It is also critical to precisely “dry” the hair prior to beginning the experiment. This is achieved by allowing the hair sample to reside in the instrument at 0% RH for a prolonged duration—which further lengthens experimental time. It is tempting to look for short cuts that can lessen test time but such actions come with a commensurate reduction in the confidence of outcomes.
The pioneer and major manufacturer of this equipment is Surface Measurement Systems15 (SMS). Figure 4 shows the company’s latest device, which also allows for the use of volatile organic adsorbents in place of water. Studies to understand the adsorption of volatile oils or fragrance components into hair can therefore be conceptualized.
Thermal Properties via Differential Scanning Calorimetry (DSC)
Upon heating, the a-helical protein structure within hair will eventually become unstable and transform into a b-sheet structure. The temperature at which this occurs is lowered if the internal protein structure is compromised and accordingly, the magnitude of this parameter is frequently utilized as another measure of hair damage. This transition temperature can be identified by differential scanning calorimetry (DSC), which monitors energy flow into or out of a sample during heating. Denaturing is an endothermic process involving an uptake of heat that manifests as a downward peak in the resulting thermogram. The peak temperature provides an indication of the protein stability while the peak area is a measure of the amount of a-helical structure present.
In dry hair, this denaturing temperature occurs at around 230°C, which is close to hair’s decomposition temperature of about 240°C. Hair decomposition will produce an especially objectionable smell in the laboratory but, more seriously, can begin to “crud up” the expensive DSC test cell. To circumvent this issue, experiments are usually performed with hair in a wet state,16 whereby the finely chopped sample is sealed inside a high-pressure DSC sample pan along with sufficient water to ensure saturation. Under these conditions, the denaturing temperature of healthy hair is around 150-155°C and experiments can be performed without impinging on the decomposition temperature.
. . .Read more in the September 2020 digital edition. . .
References
- Evans, T.A. (2011, Aug). Evaluating hair conditioning with instrumental combing. Cosm & Toil 126(8) 558-563.
- Evans, T.A. (2013, May). Consumer vs. scientific language: Relating in vivo to in vitro. Cosm & Toil 128(5) 300-304.
- Garcia, M.L. and Diaz, J. (1976). Combability measurements on hair. J Cosmet Sci 27 379-398.
- Instron website (accessed 2020, Jul 16). Products. Available at: https://www.instron.us/products
- Dia-stron website (accessed 2020, Jul 16). Available at: https://www.diastron.com/
- Stable Micro Systems website (accessed 2020, Jul 16). TA.XT plusC Texture Analyzer. Available at: https://www.stablemicrosystems.com/TAXTplus.html
- Evans, T.A. (2017, Jun). How damaged is hair? Part II: Internal damage. Cosm & Toil 132(6) 36-45.
- Evans, T.A. (2013, Aug). Measuring hair strength, Part I: Stress-strain curves. Cosm & Toil 128(8) 590-594.
- Evans, T.A. (2009). Fatigue testing of hair—A statistical analysis of hair breakage. J Cosmet Sci 60 599-616.
- Evans, T.A. (2013, Dec). Measuring hair strength, part II: Fiber breakage. Cosm & Toil 128(12) 854-859.
- Evans, T.A. (2017, Sep). New ideas and thoughts on hair breakage. Cosm & Toil 132(8) 46-53.
- Evans, T.A. (2018, Jun). Hair volume and body–A technical dissertation. Cosm & Toil 133(6) 48-55.
- Feughelman, M. (1997). Ch 2 In: Mechanical Properties and Structures of Alpha-Keratin Fibers, University of New South Wales Press.
- Evans, T.A. (2014, Mar). Measuring the water content of hair. Cosm & Toil 129(2) 64-69.
- Surface Measurement Systems website (accessed 2020, Jul 16). Available at: https://www.surfacemeasurementsystems.com/
- Wortmann, F.J., Springob C. and Sendelbach, G. (2002). Investigations of cosmetically treated hair by differential scanning calorimetry in water. J Cosmet Sci 53 219-228.