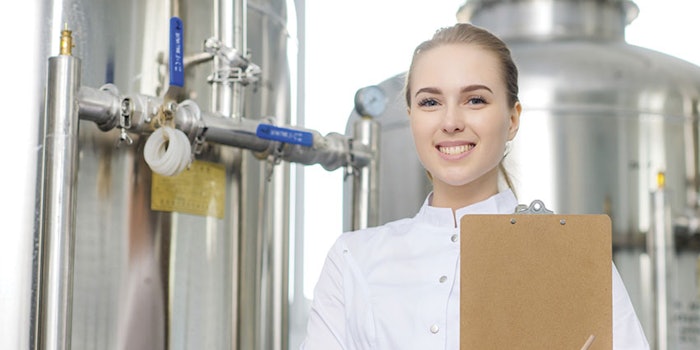
Scaling up cosmetic products to manufacturing facilities is a common cause of difficulties. From liquid/powder incorporation into viscous gels, and the discharge and filling of bulks with challenging rheology, to ensuring homogeneous emulsion products—many flow issues can occur. Yet, despite these relatively global challenges, extensive vessel and process characterization using computational fluid dynamics (CFD) does not appear to be as commonly utilized throughout the personal care industry as it is in other similar industries, such as pharmaceuticals and food.
While it could be argued the topic of CFD modelling of mixing in stirred tank reactors is well-characterized in other fields,1, 2 common topics such as counter-rotating impellers and the discharge of rheologically challenging products are, in fact, under-published in common industry technical sources. Therefore, as the cosmetics and personal care industry moves further toward manufacturing outsourcing,3 it will become ever more important to strengthen our ability to scale-up and transfer manufacturing and filling methods from one vessel/mixer geometry to another. This can be accomplished using modern, quantitative scaling methods aided by CFD, as this commentary briefly describes.4
Visualizing Flow
As is generally known, non-Newtonian fluids, which make up the majority of personal care products, have a viscosity that varies depending on the applied stress. Thus, a simple calculation of scale-up and mixing parameters, such as power input to shear thinning cosmetic emulsions, suspensions and gels, is difficult for these non-Newtonian fluids. In these cases, CFD can be beneficial.
For instance, CFD allows, through three-dimensional process modelling, for the calculation of a variety of mixing and flow characteristics with a single computational simulation. One major advantage is the profiling of shear rate “hot spots” in manufacturing vessels. Figure 1 illustrates the strain rate on water in a vessel with counter rotating impellers running at 60/-24 rpm and a homogenizer rotating at 1,000 rpm.
Such strain rate assessments allow cosmetic manufacturers to determine, in advance of manufacturing a batch, if the chosen vessel and mixing speeds may, for example, result in emulsion instability and potential production failure. The product to be manufactured can be profiled for its shear rate sensitivity using a benchtop rheometer, and CFD can then profile the strain rate/shear rate distribution throughout the proposed manufacturing process. By combining the resulting data from these two technologies, product developers obtain insight before first production trials as to whether or not our proposed manufacturing method may cause an emulsion to split due to excessive shear.
CFD also allows for the visualization of flow patterns, mixing “dead zones” and liquid velocities across a vessel, even for complicated environments such as the ubiquitously used counter-rotating multiple impeller configuration. Figure 2 shows the liquid velocities and flow patterns for the vessel described above, in Figure 1. Once any vessel “dead zones” have been identified, cosmetic manufacturers can simulate how varying the mixing regime, raw material addition points and raw material addition rates can reduce the effect of these dead zones on product mixing times and homogeneity.
CFD allows for the visualization of flow patterns, mixing 'dead zones' and liquid velocities across a vessel.
As noted, with the aid of CFD, as shown in Figure 2, product developers can even evaluate raw material addition site options; such as through a side pipe, at the liquid surface via the vessel lid, and vacuum addition through a bottom entry pipe. This eliminates the need to perform experiments at manufacturing scales, as it identifies the optimum addition point and impeller speeds in advance of the first production.
As an example, CFD can simulate the addition of fragrances and extracts to emulsions, which typically occurs at the end of product manufacturing when the emulsion is thickened and cooled. Occasionally, pooling of these liquid raw materials can occur at the surface of the emulsion, necessitating adaptations to the mixing regime or addition point. CFD, however, can troubleshoot such challenges in advance. Simulations of solid or liquid raw material additions to the bulk also can be animated over time, to visualize the time required to ensure a homogeneous mixture. This allows process engineers/chemists to recommend the best vessel choice for a given product based on quantitative data describing the vessel’s ability to mix a specific bulk product or to alter mixing speeds to ensure the best mixing performance from an available vessel.
Setting Filling Parameters
CFD also can be used to determine the filling parameters for rheologically challenging products. Simulations can be performed to determine the optimum line speeds and filling pressures/velocities,5 which allows cosmetic filling companies to visualize and eliminate filling defects such as air entrainment, and to determine the maximum shear force during filling to prevent emulsion separation.
Standardizing the Practice
It is evident from the examples described that CFD can provide much needed information for the successful scale-up and filling of shear sensitive products. As stated, while use of this technology has become standard practice in other industries utilizing stirred tank production methods, it has yet to become as mainstream in the cosmetics industry, as only industry leaders have published in this area.6, 7
As the cost of CFD is decreasing, it is becoming more feasible for smaller cosmetic companies to access this technology. This will, in turn, reduce first production/filling failures and the cost of product development through a minimization of factory trial batches and processing related batch rejections.
Acknowledgements: CFD analyses used in this article were generated using MixIT, kindly supplied by Tridiagonal Solutions.
References
- A Glace, D Seshadri, F Akpinar and B Cohen, Verification and use of CFD modeling in stirred tank reactors for pharmaceutical applications, AIChE, San Fransico (2016)
- C Sharma, D Malhotra and A Rathore, Review of computational fluid dynamics applications in biotechnology processes, Biotech Progress 1497-1510 (2011)
- wallstreet-online.de/nachricht/9878466-personal-care-contract-manufacturing-market-worth-25-8-billion-by-2025-grand-view-research-inc (Accessed on Jan 24, 2018)
- support.ansys.com/staticassets/ANSYS/staticassets/resourcelibrary/whitepaper/cosmetics-wp118.pdf (Accessed on Jan 24, 2018)
- M Tome et al, Numerical and experimental investigations of three-dimensional container filling with Newtonian viscous fluids, Computers & Fluids 90 172-185 (2014)
- digitaleng.news/de/procter-and-gamble-highlights-its-digitization-strategy (Accessed on Jan 24, 2018)
- JJ Janssen and H Hoogland, Modelling strategies for emulsification in industrial practice, The Canadian Journal of Chemical Engineering 92 198-202 (2014)