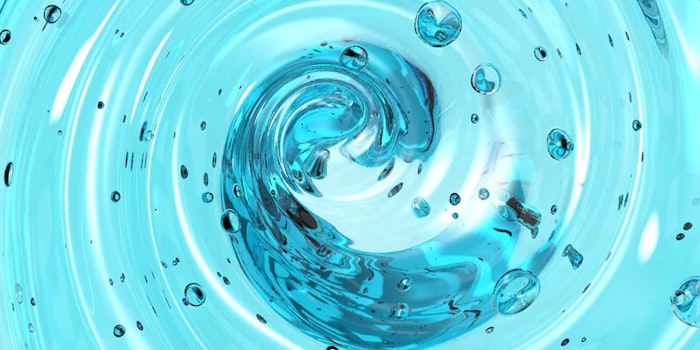
Formulators often suspend insoluble ingredients such as scrubbing beads, pearlizer crystals, oils, actives, etc., in formulations. In addition, creamy, lotion-like and thick or substantial textures often are desired. Both of these characteristics, i.e., the suspension capability and a creamy texture, are realized by a formulation’s yield stress.
Yield stress often is confused with high viscosity, but increased viscosity only causes longer settling times, it does not impart true suspension. In relation, the aim of this article is threefold: to properly define and differentiate yield stress from high viscosity; to develop a method and provide calculations for assessing whether a sample has a yield stress; and to illustrate how to determine the amount of yield needed for a given application. In part two of this series, several popular methods to measure yield stress will be explored and compared and contrasted in terms of relevance, exactness and robustness.
Defining Yield Stress
Since the earliest days of measuring yield stress, scientists and engineers have debated what method would provide the most exact and relevant values. Many methods exist and different measurements performed on the same materials often report different values. In fact, for some materials, identical measurements performed at different deformation rates often provide different yield stress values. Considering intrinsic properties such as temperature, mass or density should be independent of the measurement method, this begs the question of whether or not yield stress is a true intrinsic material property.1-4
This debate is complicated by the fact that there is no universally accepted definition for the yield stress. One common definition is “the stress above which a material flows.” However, every material that can be measured appears to exhibit flow under certain conditions. For example, long plastic pipes and rock slabs often sag irreversibly over time, indicating irreversible flow or “creep.”5 The pitch drop experiment, which is in the Guinness Book of World Records as the longest continuously running laboratory experiment, is another example of this phenomenon.6
Although these materials are experiencing stresses below their yield stresses, they are still flowing—albeit slowly. It turns out these solids are undergoing irreversible flow with extremely large creep viscosities; approximately 230 billion centipoise, in the case of pitch.7 So are the pitch and rock slabs really flowing or are they solid, as everyday experiences would indicate? And is creep considered flow? If so, does this invalidate the “true” yield stress position? Two valid arguments can be made for either case, i.e., no yield stress versus a true yield stress, but the crux of the dispute is how to define flow and how long to look for it.
Deformation, Observation and Characteristic Timescales
Here, it is useful to highlight three distinct timescales: the timescale of deformation, the timescale of observation, and the characteristic timescale of a material. The timescale of deformation is not how long a deformation is imposed. Rather, it should be thought of as a characteristic timescale of the flow; like a shear rate, for example. The timescale of observation is the time over which the sample response is measured and the characteristic timescale of a material is roughly how long it takes for said material to relax after it is deformed.
For example, a rubber band will snap back to its original shape quickly after it is deformed; on the other hand, the foam topper on a mattress may take several seconds to even minutes to return to its initial shape after it is deformed. Thus, a rubber band and mattress foam have very different characteristic timescales.
A Deborah number, De, is defined as the ratio of a characteristic timescale of a material, such as a relaxation time (τ), to the time of observation (see Equation 1).
On the other hand, the Weissenberg number, Wi, is defined as the ratio of a characteristic timescale of a material to the rate of deformation (see Equation 2), where γ is the shear rate.
To illustrate these concepts, consider Silly Puttya. As is generally known, it behaves more like a solid under fast deformations, e.g., it will bounce on the floor and it behaves more like a liquid under slow deformations, flowing into a puddle if left on a table. How can one material exhibit both solid- and liquidlike behavior that is so different? This is explained through the Weissenberg and Deborah numbers.
While the meaning of observation time and shear rate for these equations should be evident, relaxation time requires further explanation. In the puttya example, the characteristic relaxation time is the time it takes for the polymer network to relax the stress caused from an imposed deformation. If the putty is deformed at a faster rate than its relaxation time, it will not be able to dissipate the stress, so the excess energy will be stored. This is the case of Wi > 1 and the putty will behave more solid-like, storing more energy than what is dissipated and bouncing on the floor like a piece of solid rubber.
If the putty is deformed at a slower rate than its relaxation time or Wi < 1, it can dissipate more stress than what is stored and will behave more liquid-like, flowing into a puddle. Thus, the putty can exhibit different behaviors depending on the rate of applied deformation and the Weissenberg number tells us where the material is on the spectrum of solid- to liquid-like behavior, for a given deformation rate.
The Deborah number requires a different thought process. While shear rate was used for calculating the Weissenberg number, here it is not. The Deborah number does not include information about the type of flow, it only includes information about the observation time and characteristic timescale of the material. Regardless of the type of flow, the Deborah number illustrates the importance of the experimental observation time with respect to the intrinsic timescale of the material being measured.
As an illustration, imagine grabbing onto the puttya and quickly pulling it apart a few inches, while constantly observing the feeling of its resistance. The relaxation time of the puttya is on the order of 0.1 sec to 0.01 sec; this is the time it takes the putty to relieve all of the initial stress imposed by pulling it apart. Thus, at observation times shorter than the relaxation time (De > 1), the putty behaves more like a solid because the material is not able to relax the stresses imposed by the initial deformation and more energy is stored than released. In this case, the putty would pull back like a rubber band, acting more solid-like and thus be deemed to have a yield stress. However, at observation times longer than the relaxation time (De < 1), all of the initial stress would have been relaxed; the putty would begin to flow and sag and therefore deemed to not have a yield stress.
Every “solid,” from glass in windows to steel in cars, has its own distinct relaxation time. It may not be as fast as the puttya, but it is finite. The relaxation time for window glass at room temperature is estimated to be longer than 1 x 1022 years, i.e., a one with twenty-two zeros after it, which is one million million times longer than the estimated age of our universe.8 Does this mean everything flows eventually and there is no true yield stress?
A particularly obstinate measurer could define the yield stress as strictly as possible, where one measures zero irreversible deformation over an infinite amount of time for all applied stresses below the yield stress. This case corresponds to De = 0, where a measurement is conducted over an infinite amount of time. Such infinite time measurements are obviously not practical and more suited to the realm of theology.9-11
Interestingly, the Deborah number is named after the prophet Deborah, who stated in verse 5:5 of the Biblical Book of Judges, “the mountains flowed before the Lord.” There is debate as to the exact translation of this passage,10, 11 but it is thought that Marcus Reiner, who defined the Deborah number in 1928 alongside of Eugene Bingham, intended to imply something as seemingly solid and immovable as a mountain range would flow over the infinite timescale of a “supreme being” observer. Furthermore, the motto for the Society of Rheology, attributed to the philosopher Heraclitus, is “πάντα ῥεῖ,” which translates to “everything flows.”
Since the aim of this article series is not philosophical or theological in nature, yield stress will instead refer to G.W. Scott Blair’s 1933 definition as “the stress below, which no flow can be observed under the conditions of experimentation,” (emphasis is this author’s).12 Such a definition does not restrict the yield stress to being either a useful engineering concept or a true intrinsic property; both interpretations are possible, depending on how long the observer is willing to wait and how sensitive his/her instruments are. This definition for the yield stress effectively avoids debate and relieves researchers from performing infinite-time measurements to determine a yield stress.
Long Timescales and Suspension
As discussed, timescales are important in the context of the yield stress. In fact, two distinct types of yield stresses depend on the relevant timescale: static and dynamic. The static yield stress is defined as the stress required to initiate flow from rest and the dynamic yield stress is defined as the minimum stress required to sustain flow from an already flowing state.13, 14 Static yield stresses are relevant for long-time processes such as sedimentation, whereas dynamic yield stresses are relevant in dynamic processes such as pumping. The static yield stress is often, but not always, larger than the dynamic yield stress.
Formulators and product developers often are concerned with the yield stress in the context of long-timescale processes, e.g., suspending ingredients including insoluble benefit agents, beads, pearlizers and sometimes air bubbles, for visual appeal. Before deciding how to measure a yield stress for this context, however, the timescale of interest in the context of ingredient suspension must be determined.
The force driving sedimentation or creaming is the buoyancy force, caused by the density difference between the suspended agent and surrounding fluid matrix. This buoyancy force is driven by gravity, and is opposed by the yield stress (if present). Since the timescale of deformation imposed by the density difference is driven by gravity, this force acts over an infinitely long timescale—i.e., gravity is a constantly applied force. So in this case, the timescale of interest is infinite.
In order to stay more practical, the timescale of interest can be trimmed down to the shelf-life of a typical product, generally round three years. However, the only way to absolutely ensure stability for three years is to conduct a stability experiment for three full years, since there is no measurement to speed up time. Yet, it is still impractical to wait three years for guaranteed stability results, so rheology allows us to anticipate longtime behavior through a few simple experiments. These experiments, outlined next, will determine whether a material has a yield stress at a timescale of interest.
Determining Yield Stress
Some formulations typically do not have yield stresses; for example, simple cleansers and other systems, where the microstructure is solely surfactant micelles, with or without micellar thickeners. On the other hand, products with microstructures consisting of networks such as colloidal gels, associative polymers, etc., generally exhibit yield stress behavior; examples include creams, lotions, scrubs and toothpaste. However, it can sometimes be difficult to differentiate when a formulation has a yield stress, or just appears stable over long times due to a high viscosity. The key factor, which determines whether a material has a yield stress, is the solid-liquid balance.
Solid-liquid balance: The solid-liquid balance is a measure of the amount of solid-like and liquid-like character a material exhibits. Since all materials are viscoelastic to some degree, they will have varying degrees of both solid-like and liquid-like characters. For example, mineral oil will exhibit a large liquid-like character and low solid-like character, and a rubber band will be the opposite. This section demonstrates how to measure the solid-liquid balance, then how to use this value to determine whether a sample of interest possesses a yield stress under the conditions of interest.
The solid-liquid balance is a concept commonly encountered in the field of rheology and is often referred to as tan(δ), the tangent of the phase lag δ between the input and output strain/stress waves of an oscillatory experiment conducted on a rheometer.5 Another definition incorporates the elastic and viscous moduli, as shown in Equation 3.
The elastic modulus Gʹ can be thought of as the amount of energy a material can store (solid-like) and the viscous modulus Gʹʹ can be thought of as the amount of energy lost due to viscous dissipation (liquid-like). The solid-liquid balance can vary from zero in a perfect solid, to infinity in a perfect liquid, with the transition point from solid-dominated to liquid-dominated behavior occurring at a value of one: where Gʹʹ = Gʹ. Thus, if Gʹ > Gʹʹ or tan(δ) < 1, the material exhibits more solid-like character and has a yield stress, since the yield point is the transition from more solid-like to more liquid-like behavior.5
However, tan(δ) does not have just one value for a given material, it is a time-dependent quantity, meaning it varies depending on the timescale of deformation. For example, the earlier puttya example showed the material behaved more like a solid under shorter deformations, bouncing on the floor, but more like a liquid under longer time deformations, flowing into a puddle if left on a table. It can therefore be stated that the putty has a tan(δ) < 1 (solid-like) under faster deformation rates (shorter times) and > 1 (liquid-like) under slower deformation rates (longer times).
Frequency sweep test: In the case of suspending ingredients, formulators are interested in longer timescales and the behavior of tan(δ) at these long timescales. To determine the behavior of the solid-liquid balance over varying timescales, a frequency sweep test must be performed. A frequency sweep is an oscillatory test performed in a rheometer by applying a sinusoidal deformation at a fixed amplitude while varying the frequency of oscillation. In a frequency sweep, the frequency of oscillation is equivalent to the reciprocal of the time of observation;this can be expressed as shown inEquation 4, where ω is the frequency of oscillation. It follows that the Deborah number for oscillatory flows is expressed as shown in Equation 5.
It is important to note for steady, not oscillatory shearing flows, the inverse of the shear rate is not equivalent to the timescale of observation.15, 16 In steady shearing flows, the timescale of observation is simply how long the sample is measured, which is independent of the shear rate. Since the longest timescale of interest is the shelf-life of the product—again, typically around three years—to guarantee absolute stability, one would need to measure a tan(δ) < 1 at a frequency of roughly 1 x 10-8 rad/sec, which is the inverse of three years in seconds. This is obviously not feasible as the experiment itself would take three years.
Unfortunately, there are no shortcuts here; a rheometer is not a time machine. However, one can take limiting values of tan(δ) since frequencies tending toward zero are useful estimations of long-time behavior. Typically, a frequency sweep is conducted from 100 to 0.1 or 0.01 rad/sec; and if tan(δ) < 1 at low frequencies tending toward zero, one can say with confidence the material likely has a yield stress at longer times, even though only a timescale of (0.01 rad/sec)-1 or 100 sec is measured. It is important to note each frequency sweep must be conducted in the linear viscoelastic regime, meaning the applied strain or stress does not appreciably disturb the microstructure.
Now that yield stress has been properly defined, and a determination made as to whether the material has a yield stress at the timescale of interest, the amount of yield needed for a given application can be determined.
How Much Yield Stress?
When designing a formulation to suspend an ingredient, the question arises, “How much yield is necessary?” To answer this, one must look at the forces involved. The suspended ingredients usually have densities differing significantly from the suspending medium, which most commonly is water. Thus, there is a driving force for the particles to rise or settle, depending on whether their density is greater or less than the suspending medium—i.e., the buoyancy force. This force is exerted by the particle on the fluid and is given by the particle volume multiplied by its buoyancy.
For a spherical particle, this force is calculated as shown in Equation 6,17 where R is the particle radius, g is the acceleration due to gravity, and ∆ρ is the absolute value of the density difference between the particle and the surrounding medium.
The fluid yield stress also exerts a force on the particle, which for a spherical particle is given by Equation 7.17 Here, σy is the yield stress. In order to suspend the particle, the force of the yield stress must be larger than the force exerted by the particle. Thus, one can define a ratio of the force exerted by the yield stress to the force exerted by the particle as shown in Equation 8;17, 18 note that Equation 8, as written, is for spherical particles; Y can be derived for other particle shapes as well.
If the fluid yield stress is larger than the stress exerted by the particle rising or falling (Y > 1), the particle will be suspended. If the stress exerted by the particle is larger than the yield stress (Y < 1), the particle will overcome the yield stress and begin to move. However, the value of Y at which particles are suspended, denoted as Ycrit, is found experimentally to be considerably less than one for various reasons, which are discussed elsewhere.18
Experimental and theoretical values of Ycrit have been shown to range from 0.05–0.6, depending on particle shape, experimental conditions and type of yield stress fluid. In fact, for identical particles, different values of Ycrit were reported for different types of yield stress fluids, namely an associative polymer (cellulose fiber, e.g., xanthan gum) and a colloidal gel (carbomer).18 Since the value of Ycrit for a given particle and yield stress fluid cannot be known a priori, a value of Ycrit ≥ 1 can be taken as a safe guideline when formulating.
Note with changing temperature, the yield stress and therefore Ycrit also will change. To ensure stability at an elevated temperature, the yield stress and Y must therefore be measured at said temperature. It is important to note yield stress measurements at elevated and room temperatures cannot account for chemical degradation, which sometimes occurs over time and leads to decreased yield stress values upon stability testing.
It also should be noted Equation 8 is not valid if the size of the particle is comparable to the size of the network mesh of the yield stress fluid. As an example, the network mesh size of a carbomer gel would be the size of the swollen carbomer domains (on the order of a few hundred micrometers) and the mesh size of an associative polymer network would be the average distance between associations. For particles or insoluble actives that are very small, i.e., on the order of the network mesh size, these can settle through the spaces in between the yield stress fluid network, without having to overcome the yield stress.18
Example 1: Jojoba Ester Beads
To illustrate the above concepts, consider whether a formulation having a yield stress of 1.7 Pa could suspend beads made of jojoba esters having a diameter range of 250–400 μm and a specific gravity of 0.907. To solve for the yield stress necessary to suspend the particle, Equation 8 is rearranged for σy and Y is set to one as the stability criterion (see Equation 9).
Note the density of water at 25°C is 997 kg/m3 and a quick check of unit consistency shows the units above are correct (see Equation 10).
A diameter of 400 μm was used in Equation 9 as a worst-case scenario; larger particles have a larger sedimentation force (see Equation 6). With a yield stress of 1.7 Pa, Equation 8 can be used to calculate a value of Y = 15. This is well above the safe value of Y = 1 and the formulation should be able to suspend the beads, barring any chemical degradation over time.
Example 2: Air Bubbles
As another exercise, one can calculate the size of air bubbles that can be suspended for a given yield stress. Rearranging Equation 8 for R and setting Y = 1, one canderive Equation 11.
Thus, the formula will suspend air bubbles with a diameter of about 520 μm (0.52 mm) or less; bubbles larger than this size will rise.
Robustness
It is important to note the yield stress value calculated from Equation 9 is the minimum yield value for infinitely long deformation timescales, and that the values measured are always time-dependent because measurements are conducted over a finite timescale. This is important in the context of formula robustness.
For example, one may measure a yield stress at 0.1 rad/sec that is sufficient to suspend the jojoba ester particles at long times when the formulation is at rest. However, the product may experience vibration and other deformation at faster timescales during transport and handling. One could check the stability of the product under faster deformation rates by performing yield stress measurements at these faster rates, which can be time-consuming. A more qualitative sense of stability can be gained by examining the behavior of the solid/liquid balance in the frequency sweep.
Remember, tan(δ) must be < 1 for the sample to possess a yield stress, so if tan(δ) is close to one or exceeds one at moderate frequencies, yield stress measurements should be performed at faster deformation rates to ensure stability under these conditions. For example, the frequency sweep of a cleanser containing wormlike micelles and an acrylates copolymer is shown in Figure 1. The yield stress measured by an amplitude sweep at 0.1 rad/sec was 1.7 Pa—more than sufficient to suspend the jojoba beads as calculated above. However, at frequencies between about 0.7 rad/sec to 60 rad/sec, tan(δ) is > 1, which means the sample does not have a yield stress under these conditions.
Thus, if the sample experiences deformations on a timescale between 0.02 sec to 1.4 sec, i.e., the inverse of the frequency range, the beads would settle. Any deformations faster than 0.02 sec or slower than 1.4 sec need to be large enough in amplitude to overcome the yield stress at that timescale for the beads to settle. Thus, this product may appear stable under quiescent stability conditions, but may not be robust under more rigorous conditions.
Conclusion
This article has robustly defined yield stress and outlined a process to determine if a sample of interest possesses a yield stress at a timescale of interest. It also has illustrated how to calculate the amount of yield needed to suspend an ingredient of interest; examples of jojoba ester beads and air bubbles were given. Taken together, these considerations provide the framework for a protocol to prepare and evaluate samples as follows:
- Determine type of yield stress relevant for application (static vs. dynamic).
- Determine if sample has a yield stress at a timescale of interest:
- Long timescales: tan(δ) < 1 as ω→0,
- Shorter timescales: tan(δ) < 1 at the times- cale of interest.
- If the sample has a yield stress, determine how much yield is needed (see Equation 8); and
- Measure yield stress.
As noted, in part two of this series, popular methods to measure yield stress will be explored, then compared and contrasted in terms of relevance, exactness and robustness.
Acknowledgements: The author would like to acknowledge Thomas Hu for input, and Don Harper, Tobias Fütterer, Davide Miksa, and Michael Fevola for general feedback and proofreading.
References
- HA Barnes and K Walters, The yield stress myth, Rheologica Acta 24 323–326 (1985)
- HA Barnes, The ‘yield stress myth?’ paper—21 years on, Applied Rheology 17 (2007)
- HA Barnes, The yield stress—a review or ‘panta rei’—everything flows?, J Non-Newtonian Fluid Mechanics 81 (1999)
- G Astarita, Letter to the editor: The engineering reality of the yield stress, J Rheology 34 275–277 (1990)
- CW Macosko, Rheology: Principles, Measurements and Applications, VCH Publishers, New York (1994)
- https://smp.uq.edu.au/pitch-drop-experiment (Accessed Aug 19, 2015)
- R Edgeworth, BJ Dalton and T Parnell, The pitch drop experiment, Eur J Physics 5 (1984)
- ED Zanotto and PK Gupta, Do cathedral glasses flow?—Additional remarks, Amer J Physics 67 260–262 (1999)
- M Reiner, The Deborah number, Physics Today 17 62 (1964)
- MM Denn, Just what did Deborah say, Rheology Bulletin 80 (2011)
- M Boehm, Why did the mountains do anything at all, Rheology Bulletin 81 (2012)
- GWS Blair, On the nature of “yield-value,’’ J Applied Physics 4 (1933)
- DCH Cheng, Yield Stress—A time-dependent property and how to measure it, Rheologica Acta 25 542–554 (1986)
- A Fall, J Paredes and D Bonn, Yielding and shear banding in soft glassy materials, Phys Rev Letters 105 (2010)
- AB Metzner, JL White and MM Denn, Constitutive equations for viscoelastic fluids for short deformation periods and for rapidly changing flows: Significance of the Deborah number, AIChE J (12) 863–866 (1966)
- J Dealy, Weissenberg and Deborah numbers—Their definition and use, Rheology Bulletin 79 14–18 (2010)
- AN Beris, JA Tsamopoulos, RC Armstrong and RA Brown, Creeping motion of a sphere through a Bingham plastic, J Fluid Mechanics (158) 219-244 (1985)
- H Emady, M Caggioni and PT Spicer, Colloidal microstructure effects on particle sedimentation in yield stress fluids, J Rheology 57 (2013)