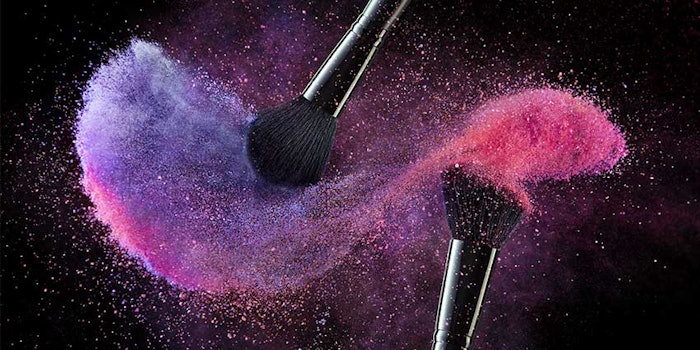
Though many people associate color cosmetics with anhydrous lipsticks and emulsion foundations, powder formulations have always been a core product category that drives brand growth and consumer loyalty. The U.S. powder market alone is set to grow by almost 7% by the end of fiscal 2014.1 This category has been steadily gaining share in the makeup market, with new technologies entering the market in both packaging and raw materials. Currently, powder formulations contribute approximately 12% to annual global makeup sales.
The skill set for complete powder formulating can only come from years of experimentation and development using a variety of powder-based products. It requires thorough knowledge of raw materials, color matching techniques and processing. Besides being a formulator, this is one case where the formulator must also unofficially play the role of a packaging analyst to ensure compatibility with the proposed components. Whether the powder-based product is loose or pressed, its stability in a packaging component can dictate its performance.
As noted, powder cosmetic products (both pressed and loose powders) include foundations, eyeshadows, primers, blushes, bronzers and all-over shimmer powders. Though the raw materials used in them often are similar, the processing, texture, packaging, applicators and application, along with color development, vary for each type; these are described here.
Raw Materials and Uses
Powder formulations involve the blending of pigments, fillers, and dry and wet binders to develop a uniform product. The coverage and shade provided by a product is defined by the levels of organic dyes, iron oxides and titanium dioxide in the formula—as well as processing techniques.
Dry binders: Dry binders are a necessity to powder formulations. They compact easily and use their adhesive properties to assist other ingredients in compacting. Some common dry binders are polyethylene, kaolin and fatty acid derivatives—including their metallic soaps, such as zinc stearate.
Surface treatments: Surface treatments on fillers like talcs, sericites and micas are used to provide smooth application while assisting with wear and adhesion to the skin. Their use will change the overall coverage of the makeup. The addition of surface-treated materials may reduce the need for wet binders in the system, as they can be readily incorporated into the formula. Some popular surface treatments are based on alkyl silane and dimethicone chemistries. These treatments impart greater hydrophobicity and skin adhesion to the formula, as well as a smoother and more spreadable application. Other treatments may include phospholipids or lecithin, which provide similar benefits and deliver a more lubricious end feel.
Wet binders: Wet binders are added to wet the pigments in a formula and help dictate the overall feel of the product. They are essential in ensuring pigment dispersion, and commonly are the ingredient/phase to adjust when formulation issues such as uneven application arise. These materials are usually silicones, esters or synthetic hydrocarbons. They may also include solid materials that are not always liquid at room temperature, such as waxy polymers and esters.
Fillers: Fillers are used to maintain product texture and compressibility throughout a shade family, as well as to provide improved wear benefits, depending on the surface treatment. Talc, mica and sericite are predominantly used.2 Ingredients that prevent caking, such as silica, may also be added to loose powder formulas, in cases where texture differences are desired.
Stability Concerns
Powder-based formulations come with their own set of concerns that are different from typical skin care or makeup formulations. Many problems relate to pressing that can, therefore, only be seen once the powder is pressed; for example, dusting after touching the surface or glazing, i.e., a shiny appearance after the applicator is used. Others include stability concerns that develop over time, such as the clumping of particulates or difficulty with pick-up, making the product too hard to press. Visually inspecting the surface and removing some product to apply it will reveal the product’s consistency and aesthetics. When a glaze develops or product becomes overly rigid, it is often due to binder migration through the tablet toward the surface of the product.
In the lab, potential stability problems can be identified by traditional tests, whereby the product is exposed to a variety of extreme temperature conditions. Further tests include drop tests and shaker stations to challenge the tablet’s ability to survive shipping conditions. While binding the product correctly will result in good stability, the formulator must balance this with production concerns related to difficulty in compressing the tablet. Using both a dry binder such as zinc stearate and an anti-caking ingredient like silica is usually helpful for balancing the powder and avoiding unexpected pressing issues during production. Note that the described tests may also be package-specific; i.e., what works in a one-inch round pan may not work in a four-inch square pan—scenarios that may be proposed for a special marketing program.
Process Basics and Equipment
Many powder-based formulation issues can be avoided by using the same process and systems in production that were successful in the laboratory. Processing powder products typically involves the steps of de-agglomerating particulates via pulverizing/milling, adding liquids and other powders, and blending.3 The formulator must efficiently advance through this process in as few steps as possible.
Processing equipment in the lab is often limited to blenders, coffee and spice grinders, and simple blenders. A blender or coffee grinder, which contains spinning blades, is supposed to simulate pulverizers and mills in production. These appliances are similar to hammer mills, which use a hammer to break down and deagglomerate pigments. While these appliances process pigments, the production mill does a more uniform and consistent job, leading to undispersed pigments in laboratory batches. The powder shades in the lab would therefore neither be fully developed nor attain maximum color distribution throughout the product. Thus, with all manufacturing equipment, color development can be affected if the mixing is not the same. In relation, temperature also must be controlled, especially in smaller equipment where excessive heat can be generated, extending product processing and causing agglomeration.
Formulators who use multiple types of blenders during development can, therefore, expect different results in the pressing and color development of powders. Correlating what a formulator does in the lab to what the results are in production can take some effort, but after moving a product from the lab to production, standardizing the techniques will minimize inconsistencies from one formulator to the next and generate successful production processing results—at least for that formula family.
Also during scale-up, it is important to consider the potential for loss of ingredients; e.g., of liquid binder, though the transfer and spraying apparatus. Accounting for loss will help to maintain the proper powder to liquid ratio. Adding extra liquid binder will keep the formula balanced so it compresses in a consistent manner. Another consideration is properly loading the powder in the mixing vessel to ensure the binder is sprayed on the powder and not on the walls and impeller.4 Binder that is lost in the lines or stuck on the walls can make the powder drier and looser, and will affect the pressing and stability of the product.
Color Consistency and Pearl Level
Achieving the final powder color and coverage is key, so to fully develop shades and minimize undispersed pigments, processed extenders can be used; for example, Red 7 in talc extender. Quality-controlled pre-pulverized or jet-milled pigment extenders can help the formulator develop shades in the lab that are consistent to the pilot and production batches. While this approach may not always be the easiest or most cost-effective, it is the most controlled. Such extenders are usually not the full formula; they typically contain the pigment at a relatively high level, mixed and milled with fillers used in the product family and others. They do not easily separate, so storage and long-term stability are rarely issues.
During shade-matching, it is also important to maintain consistent levels or percentages of pearl and mica from batch to batch. This will give the consumer a more consistent feel and application, as it helps to dictate the spreadability of the product. Formulators should also maintain similar-sized pearl particles from shade to shade within a family to maintain texture and application parameters. As with most particulates, smaller-particle pearls feel smoother and lay more evenly, compared with larger pearl particles that tend to be raspy and lay unevenly. When employing borosilicates and synthetic fluorophlogopites, it is advisable to use them sparingly to maintain the feel as much as possible. Milling these special materials will reduce grit as well as their ability to provide the special light effects for which they were added; further, milling these types of pearls is not cost effective.
Maintaining a consistent product while color-matching is usually a big hurdle, and formulators should know the threshold of their formula when it comes to color adjustments. If the adjustment addition is equal to 20% of the batch, for example, the overall adjustment also should include corrective measures for liquid and dry binders, as well as preservative, to bring the formula back to 100%.
Issues in Packaging
Most technical issues with powders involve processing and packaging, since problems that arise during formulating and pressing are easily corrected at a lab scale. Therefore, packaging components should be consistent throughout the development phase and into manufacturing, specifically in relation to the shape and depth of pan.
The formula is built around packing and binding particulates and solvents in a stable formula that is specific to a component size. If a formulator uses a relatively large pan when filling and pressing in the lab and suddenly changes to a smaller pan, glazing in the powder is sometimes the result. If the opposite occurs and a formulator switches to a larger-sized pan, the powder may not pass the drop test, forcing the formulator to press the powder harder, in turn compromising its application and feel. There is also a concern when it comes to the shape of the pan. A formula can sometimes act differently if the formula was created in a round pan in the lab and the final pan is square, for example; in this case, production will usually see the pressed pieces breaking at the corners and edges.
When it comes to loose powders, an obvious issue is when dispensing orifices in the sifter are not compatible with the formulation. The size and number of orifices play a role in proper dispensing. Changing the sifter will affect the delivery of the product onto the applicator and onto the skin. In addition, the applicator is a key component to fully deliver the benefits of the product. Whether the applicator is a brush or sponge, its early identification for formulation compatibility will avoid problems during launch. Applicators can help to develop the product’s proper shade and deposition on the skin, as well as minimize glazing or dusting. And although brush sizes may be the same, whether the bristles are natural or synthetic can impact optimal application. Neither is necessarily superior; each has benefits depending on the formula and package.
Conclusion
Makeup companies will continue to focus efforts on new innovations and formulations in the powder category. To attract new consumers, new packaging and processing techniques will bring novel ways to press design shapes or personalized logos on products. Furthering formulations with additional consumer benefits while maintaining proper stability will continue to make this a growing market.
References
- US Make-up Retail Sales Fiscal 2014, NPD Beauty Trends report (2014)
- J Hollenberg, Color Cosmetics, ch 26 in Harry’s Cosmetology, 8th Edition, Chemical Publishing Co., Revere, MA USA (2000) pp 560–588
- H Rumpf, Science of Agglomeration, Chem Tech 45 (1) 1–11 (1974)
- D Buell, K Barclay, P Block, J Junker, B Victor, D Melenkevitz and D Yacko, The Manufacture of Cosmetics, ch 35 in Harry’s Cosmetology, 8th Edition, Chemical Publishing Co., Revere, MA USA (2000) pp 787–874