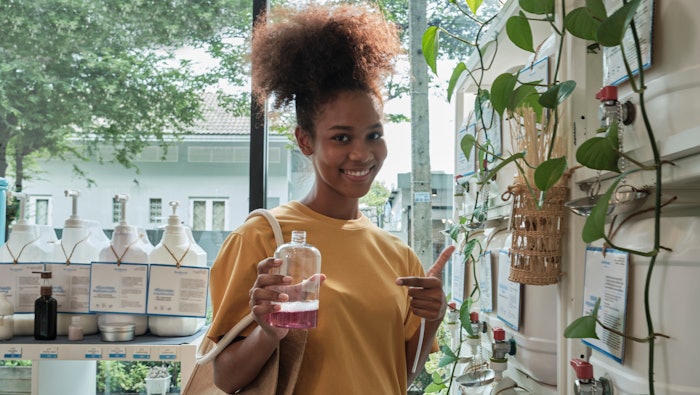
The commercial sale of eco-conscious, refillable products in bulk now includes liquid galenic formulas. Their diverse flow chains pose unique microbial challenges, as described in this article, underlining the importance of flow chain planning and assessment tools/strategies.
Log in to view the full article
The commercial sale of eco-conscious, refillable products in bulk now includes liquid galenic formulas. Their diverse flow chains pose unique microbial challenges, as described in this article, underlining the importance of flow chain planning and assessment tools/strategies.
Driven by an increasing awareness of environmental challenges, consumers are showing growing interest in purchasing refillable bulk products. Such products typically employ reusable packaging that consumers refill with the exact amount they desire, making these products more environmentally friendly and reducing waste. Initially devoted to food, refillable bulk buying has rapidly expanded to other sectors including cosmetics. While solid products paved the way, galenic formulas including oil/water emulsions, body oil, etc., have recently been made available.
Since first appearing in the 1980s, bulk buying has risen sharply.1, 2 Cosmetics are not excluded from this growth, representing up to 25% of the sales of specialized shops. Dedicated brands are springing up and traditional actors are joining the scene, in some cases to initially test the concept with dry solid products before expanding to galenic forms.
As this sector has grown, it also has organized. Non-profit groups were created to provide information about regulations and hygiene, as well as training. Along with the industry, these groups also defined standard cleaning/disinfection protocols for reusable containers of bulk cosmetics.
In France, the legal framework is ahead of many countries. In 2020, the Consumer Code defined bulk sales (article L.120-1) and set basic rules for (re-)usable containers (article L.120-2) as well as objectives for their use to reduce carbon footprint (decree-law 2022-507). Similar texts exist in other regions with variable scope and applications, such as the European Union’s action plan for a circular economy, or the SB 54 Plastic Pollution Prevention and Packaging Producer Responsibility Act in California, USA.
In collaboration with Anemcoli, a non-profit organization dedicated to cosmetic microbiology, the authors sought to assess the microbiological risks3 of aqueous and non-aqueous bulk liquid cosmetics dispensed in retail shops. These results are discussed in the present article.
The primary focus was to analyze whether well-known microbiological hazards were potentially heightened by this distribution process – and if so, by how much – as these products are handled by non-specialists. Indeed, the retailers selling refillable bulk cosmetics are part of the manufacturing chain, which requires them to comply with GMPs and hygiene standards – crucial elements they should master.
Bulk Cosmetic Flow Chain
Before microbial risk measurements were taken, the flow chain for bulk cosmetics was delineated (see Figure 1, below), beginning with manufacturing by a cosmetic company and ending with distribution to the final customer. As one might imagine, each step poses a new microbiological risk; note that the dynamics depicted in Figure 1 do not claim to be exhaustive of all possible flow chains or foresee any future developments.
In brief, the semi-bulk – i.e., the manufactured bulk product reaching a retailer – arrives directly in the distribution container used. Alternatively, the semi-bulk container requires the shop to transfer the product to its distribution container. In this case, the distribution container is refillable or disposable, which requires the additional consideration of storage when not in use.
The distribution system may or may not be re-usable or pre-installed on the container. Regardless of the system used, protecting the opening from microbial contaminations is an important aspect and this concern applies to the entire flow chain. The flow routes shown in Figure 1 consider four system types: gravity, push pump, peristaltic pump or pressurized pump.
The last point in the process is the container used by customers. For the assessments described next, reusable dedicated containers were the main focus. These are typically washed by the shop, brand or customer, with or without specific recommendations.
Besides the container used, several additional aspects should be taken into consideration: is dispensation assisted service or self-service? how are containers examined for cleanliness, and by whom? is the compatibility of the container verified (i.e., volume, shape, composition, etc.)? also, are optimal cleaning/disinfection procedures ensured?
Flow Chain Ground Survey
To confront the depicted flow chain with facts and evaluate the potential for microbiological contamination, a ground survey was carried out in physical shops that used different distribution systems. The shops selected specialized in selling: cosmetics, bulk cosmetics or general bulk goods.
Fourteen different products were evaluated: rinse-off foaming products (10), white emulsions (3) and a shower oil (1). Evaluations of these products included determining their pH and quantifying antimicrobials generally used in cosmetics (EC Regulation 1223/2009 - Annex V) to assess if preservation strategies were equivalent to traditional products or reinforced to guarantee increased protection. Also evaluated were their microorganism flora according to ISO21149 and ISO16212. Results, detailed next, are summarized in Table 1 (see below).
Findings: Labeling Failures
Only 12 of the 14 products were labeled to indicate their compositions. Also, five presented differences between the composition labeled and that found upon analysis. In some cases, antimicrobials that were not mentioned on the label were also found, while others that were mentioned were not detected.
Such labeling errors could be due to failure to remove previous labels on reusable containers, or using incorrect labels. These errors could have occurred on the semi-bulk, the distribution container or the customers' container.
Findings: Poorly Adapted Preservation Strategies
Of the products evaluated, one used a preservative strategy that is not compliant with EU regulations for non-rinse-off products. In addition, the shower oil had no preservative, relying instead on its galenic properties, while two products contained antimicrobials at one-tenth of the concentrations generally used. What’s more, five of the eight cosmetics protected by organic acids had a high pH, rendering their protection poorly efficient. All of these issues are especially problematic considering the distribution path of bulk liquid cosmetics, which requires robust preservation strategies.
Findings: Two Contaminated Products
Of the 14 products tested, two shampoos showed contaminations exceeding the 1,000 CFU/g ISO17516 threshold (460,000 and 18,300 CFU/g). Identification of the two contaminations by MALDI-TOF mass spectrometry indicated both were Pluralibacter gergoviae. While ISO17516 does not list this bacterium as pathogenic, its presence is undesirable and reveals a general hygiene failure that could lead to the alteration of a product.
In both cases of contamination, the products reached shops in their distribution containers where the distribution system, a reusable tap, was installed. Unprotected, the tap's opening was turned upward between distributions to avoid product spillage. In this scenario, even if the distribution was assisted, the unprotected tap opening could have been the source of contamination, either by air or user hands.
Contamination also could have occurred upon installation of the distribution system (again by air or hands) or by cross-contamination from the previous batch, as it is reusable. Alternatively, the semi-bulk could have been contaminated during manufacturing, considering P. gergoviae is a known industrial contaminant.
Both products additionally showed inadequate preservative strategies, relying only on salicylic acid while presenting relatively high pH values (5.15-5.28), which enable poor antimicrobial protection.
Discussion: Thorough Planning of Bulk Distribution
The results of this ground survey, in addition to previous experience, highlight these critical points to consider before marketing bulk liquid cosmetics. Such a development should involve a multidisciplinary team to enable a global view.
Indeed, strong knowledge of the containers and distribution systems used is necessary. Their compatibility with the product, along with the product’s microbiological quality, handling steps and any other business constraints, is essential. From there, a risk analysis can be performed to propose solutions to control these risks, guaranteeing the quality of the cosmetic to avoid contamination across the entire flow chain.
In cases of reusable containers and/or distribution systems, management methods must be applied such as permitting (or not) multi-formula filling, cleaning and disinfection, validation of protocol effectiveness, etc. To be complete, recommendations should also be provided to the consumers using the packages to ensure they are aware of storage, use and hygiene rules.
Small-scale testing also could assess the robustness of the chosen approach. After validation, full-scale tests in a limited number of shops would seem reasonable as well. Quality controls would then enable the qualification of the process under real conditions.
Mitigating Microbiological Risks Along the Flow Chain
Based on the described flow chain survey and practical experience, several points along the bulk liquid cosmetic flow chain were identified. Figure 2 (see below) indicates the risks (in red), as well as control points where these risks require further development to mitigate them – e.g., specifications, testing, controls, etc. (in blue); and/or where shops should consider implementing guidelines (in green). Further developments are required, as well as the involvement of retailers, however, mitigating these microbiological risks is within reach.
Preservation and contamination prevention: While the manufacturing of cosmetics for bulk distribution appears to present no specificities and minimal microbiological risks, robust preservation strategies are essential to ensure the product can safely withstand the additional risks posed by the flow chain – and that customers have the safest products possible.
Avoiding contamination requires attention from the shipping stage on; if not sooner. Consider if the shipping container used is usual for the manufacturer and/or the packaging sub-contractor; whether a feasibility study is needed; and what the sampling rules should be before release.
Note that while using traditional materials such as plastics or stainless steel may seem safe, the storage conditions of empty containers could increase contamination risks. Similar risks exist with dispensing systems used for the first time. Acceptable microbiological specifications therefore must be defined.
In addition, if the dispensing system is already present on the semi-bulk container, consider how to prevent its contamination during transport and storage. If it is installed in the shop, determine the best practices to prevent contamination on-site, as well as how the semi-bulk should be stored.
GMP practices and training in shops: While GMP practices may be standard during manufacturing, they are not in retail shops. Therefore, the shop staff should be trained in GMPs, covering all aspects of the flow chain.
Extended support should also be provided; for example, if the semi-bulk is transferred to its distribution container on-site in the shop, clear guidance should be provided about how to do such, so as to prevent airborne or hand-carried contamination. Additional considerations include the environment, any intermediate equipment or hygiene requirements for transferring the semi-bulk to the container.
Previous product residual contamination: Also be mindful that previous product residuals in refillable dispensing containers and reusable systems could be a source of contamination – not only microbiological, but also chemical. Efficient cleaning and disinfection procedures must be defined and validated.
What’s more, residual water can enable microorganism growth, so its presence should be avoided; or at least the quality of the residual water should be assessed.4 Alternatively, if the container is dried (wiping, open air, etc.), the risk associated with drying should be evaluated. Again, clear instructions must be provided.
Dispensing system: Another essential point is the dispensing system, which depending on the type, can be a major source of contamination by hand-carried contaminants transferred during the system’s installation or through product distribution.
If the system consists of a simple tap that is turned upside down between uses, airborne and/or hand-carried contamination is easy. Here, staff-assisted dispensing could be an element of control, which was observed in most shops during the described one-site survey. This further stresses how staff training is crucial.
When the dispensing system is contaminated, depending on its physical characteristics, another risk is back-contaminating the bulk product present in the dispensing container. It is therefore important to assess such a risk and test products as needed using previously proposed approaches.5-7
Additional considerations: Several additional points should be considered to ensure the microbiological safety of bulk liquid cosmetics. For one, transparent containers could potentially jeopardize the integrity of light-sensitive preservative systems such as sorbic acid. In addition, peristaltic or pressurized distributing pumps require specific cleaning/disinfection protocols to avoid residual water.
Another aspect is to determine whether any container can be (re-)used by customers, including that which previously held a different type of cosmetic product. Then there is the question of how to check the container’s integrity and cleanliness – and whether current solutions proposed by bulk product shops are appropriate.
As stated, note that the present risk assessment does not pretend to be exhaustive or prioritize foreseen challenges. Precise evaluations must absolutely be carried out in each case, depending on the chosen model.
Conclusions
Consumer interest in refillable bulk liquid products is booming, as are different dispensing models. All stakeholders agree on the importance of hygiene, which the present flow chain and ground survey show can be an issue with such products. And as the sale of bulk liquid cosmetics continues, additional issues must be addressed such as batch transition; the compatibility of reusable containers with formulas – and whether they are interchangeable; responsibility scopes; skill levels of shop staff; traceability; etc.
Even if limited, results of the present ground survey revealed microbiological, chemical and regulatory deviations. Thus, by changing the traditional distribution model to that of a refillable bulk process, marketers pose new microbiological challenges that should be considered early in product development to ensure formulations are robust and can withstand the flow chain.
Identifying the specific risk of a distribution model, developing adapted controls and implementing appropriate procedures are essential; the present analysis and suggested control measures can serve as a starting point. Existing and upcoming guidelines cannot replace specific risk analyses and the development of relevant control methods such as dilution tests, iterative tests, disinfection validation, etc.4-6 Setting up such tests will be the continued focus of Anemcoli's research.
References
1. Reiner, C. and Desaint, S. (2021). Produits cosmétiques en vrac: Situation à date, analyses des produits du marché et recommandations techniques. Lille, France, Anemcoli.
2. Théry, E. (2021). Le vrac emballe la cosmétique. Les Echos. Available at: https://www.lesechos.fr/weekend/mode-beaute/le-vrac-emballe-la-cosmetique-1295586
3. Michalek, I.M., John, S.M. and Caetano Dos Santos, F.L. (2019). Microbiological contamination of cosmetic products - Observations from Europe, 2005-2018. Available at https://pubmed.ncbi.nlm.nih.gov/31166041/
4. Tintilier, P. (2004). Evaluation des risques de contamination - Méthode d’objectivation et exemples d'application. Lille, France. Anemcoli (2004)
5. Lepage, C. (2005). Protocoles d’essais simulant les conditions d’utilisation - Premiers résultats et conclusions. Lille, France: Anemcoli (2005)
6. Bresiciani (2006). Test d’usage: Proposition d’un protocole adapté à l’évaluation de l’efficacité de la conservation. Lille, France: Anemcoli (2004)
7. Cosmetic Valley (2019). Guideline for evaluation of physical antimicrobial protection provided by packaging. Available at: https://www.cosmetic-valley.shop/11-publications