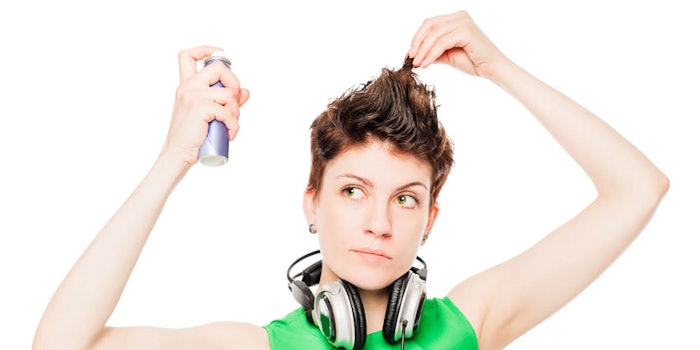
This article is the second of two discussing instrumental testing methods with applicability to the hair styling area. The previous article1 discussed consumer language associated with these products—in particular, the term hold. Instinctively, there is a tendency to equate this word with style longevity, but also discussed was the strong link of hair stiffness to consumer perception of this attribute. In short, while consumers profess the desire for products that do not adversely affect the feel properties of hair, this stiffness appears to act as the cue that the products are working.
Log in to view the full article
This article is the second of two discussing instrumental testing methods with applicability to the hair styling area. The previous article1 discussed consumer language associated with these products—in particular, the term hold. Instinctively, there is a tendency to equate this word with style longevity, but also discussed was the strong link of hair stiffness to consumer perception of this attribute. In short, while consumers profess the desire for products that do not adversely affect the feel properties of hair, this stiffness appears to act as the cue that the products are working.
In keeping with this discussion, the earlier article described the two most commonly used methods for evaluating styling products in the laboratory: high humidity curl droop experiments for style longevity, and mechanical bending experiments to assess hair stiffness. However, it is worth pointing out that the properties of polymer films deposited by styling products are not constant, and performance criteria can change dramatically as a result of formulation and environmental factors. This article discusses additional evaluation gauges to help hair product development scientists with formulation optimization.
Film Casting
Perhaps the simplest and undoubtedly one of the most insightful exercises involves casting polymer films from prototype and finished formulations. This is achieved by spraying or pouring the product into a suitable receptacle, then setting it aside for a few days to allow for the evaporation of volatile ingredients and drying of the film (see Figure 1). At the end of this duration, the visual properties of the film, i.e., color and clarity, can be observed while simultaneously gaining an appreciation of its hardness.
The mechanical properties of the resulting film are dictated by a number of variables. Most obvious is the selection of the polymer itself, but these characteristics can be significantly modified by formulation ingredients. The most common means of manipulating stiffness are through the selection and use levels of a neutralizing agent. The solubility of polymers containing carboxylic acid functionality can be achieved and facilitated by raising the pH, which generates the carboxylate ion and produces charged groups on the molecule. This is generally accomplished through the use of small organic bases, e.g., amino methypropanol (AMP), which also become entrapped in the polymer coating and in doing so, act as plasticizers that soften the resulting film.
The presence of other small molecules with hydrogen-bonding capability; e.g., propylene glycol and glycerol, will have a similar effect. A less obvious contributor can be the fragrance, where the solvent/diluent is often a strong plasticizer, e.g. dipropylene glycol, which may become present at a significant level in the dried down film, after evaporation of volatile solvents that constitute the majority of the formulation.
The hardness of the resulting film also will be strongly impacted by environmental conditions. Moisture is a powerful plasticizer of these water-soluble polymers, and its abundance in the film is dictated by the relative humidity. Therefore, it is insightful to examine the film properties under different conditions—where hard and brittle properties may be present at low humidity, but the film becomes soft and pliable at elevated humidity levels.
Dynamic Vapor Sorption
A previous article2 described the evaluation of water content in hair as a function of humidity by using the Dynamic Vapor Sorption (DVS) technique. This same approach can be used to determine the hygroscopic nature of the described polymer films. Re-capping, DVS involves using a sensitive microbalance to monitor the weight of a sample as it is allowed to equilibrate at differing humidity. Figure 2 shows the results of a film cast from a skeletal formulation based on a popular hair spray polymer that was allowed to equilibrate in 10% increments up to 90% RH. At lower humidity, the film adsorbs relatively low levels of moisture but this capacity increases greatly at high humidity values. At 90% RH, the polymer film contains approximately 30% water; it therefore becomes clear why the coating is considerably softer under these conditions.
Further Film Property Evaluations
The properties of the described films can be characterized by other techniques commonly used in the polymer chemistry field. The hard/rigid or soft/pliable nature of the film relates to its glass transition temperature (Tg); specifically, a Tg that is higher than room temperature yields a hard/glassy film, while a transition temperature below ambient results in a soft film. Incorporating exogenous molecules that disrupt the polymer structure will lower the glass transition, representing the underlying cause of plasticization.
It is common to determine glass transition temperatures using differential scanning calorimetry (DSC), where the phase change is seen as a step-like shift in the baseline. However, a much-valued boost in the sensitivity of this measure can be obtained using modulated DSC, which utilizes an oscillating heating rate rather than the conventional linear temperature program.3 Table 1 shows the glass transition results for films obtained from skeletal formulations based on two popular, commercially available styling polymers.
For polymer 1, the vendor literature suggests a 120°C glass transition temperature but this value represents the neat polymer in an anhydrous state. As such, Table 1 shows how both formulation and environmental factors play major roles. For example, after neutralization with an appropriate amount of AMP, and adsorption of moisture commensurate with 30% RH, the glass transition of the polymer 1 film has decreased to 63°C. This value is still considerably above ambient conditions, and consequently, a hard, glassy film results under these circumstances. If the film is allowed to equilibrate at higher humidity, it adsorbs more moisture (see Figure 2) and the glass transition falls further. At 80% RH, the mid-point of the glass transition is still above ambient but peak broadening also accompanies these declining values. As such, the low temperature tail of the transition can begin to infringe on room temperature, and some reduction in stiffness is observed.
Polymer 2 has a considerably lower glass transition temperature such that the Tg of its film at 30% RH is comparable to that of polymer 1 at 80% RH. Accordingly, polymer 2 has a softer, less-brittle feel. Indeed, at medium and high humidity, the glass transition temperature drops below room temperature, and the film develops a distinctly viscous consistency. The stiffness of these thin films can be further characterized by mechanical techniques; to do so, instruments must be housed in an environmental chamber to allow for the control and manipulation of relative humidity. For such measurements, small devices such as Dynamic Mechanical Analyzers (DMAs) are therefore advantageous.4
Bond Adhesion Testing
Hair sprays work, in essence, by spot-welding and seam-welding hair fibers together to create a three-dimensional structure that supports the newly-created style and provides longevity. Therefore, it is instinctive to presume that the strength of these hair-polymer bonds should be an important factor. This potentially tricky measurement can be performed using a carousel designed especially for use with the Diastron 600 series of mini tensile testers (see Figure 3). These testers were covered in a previous article5 describing how to measure the tensile properties of individual hair fibers.
For this modified approach, individual hairs are again crimped between two brass ferrules to yield a 3-cm fiber length. However, this alternate carousel also contains additional slots that house aluminum blocks, to which a second fiber has been glued. In short, the prepared carousel contains 25 perpendicular "crosshairs." A small droplet of polymer test solution is then applied to each junction using a micro-syringe. The droplets are allowed to dry and produce a series of spot welds. The back portion of each hair fiber is then cut using sharp micro-scissors to subsequently allow for mechanical testing of the bond itself.
As highlighted previously, it is necessary for the instrument to be housed and operated in a bench-top environmental chamber. The carousel is thus carefully placed on the instrument, and the test samples are allowed to equilibrate for a suitable period of time. The device then deforms each individual spot weld until breakage, generating a series of stress-strain curves from which the adhesive properties can be quantified as either a bond strength or energy.
The use of a fiber optic microscope can yield additional insights on bond adhesion results. Here, the eyepiece is focused on the crosshair test point, providing the ability to watch the bonds fail under deformation. Accordingly, it is evident how hard, glassy polymers yield low bond strengths due to their considerable brittleness, while low bond strengths also arise from especially soft films, which have limited cohesive strength. It is also possible to observe whether failure is cohesive, i.e., the polymer itself fails, or adhesive, i.e., the hair-polymer interface fails.
Figure 4 shows a schematic that illustrates the relationship between the bond strength of these spot welds and the stiffness of the polymer film. Especially stiff films are brittle and yield low bond strengths. In this situation, softening of the film reduces the brittleness and leads to increased bond strengths. However, if the film becomes too plasticized, it begins to lose cohesive strength and the bond strengths again decrease. Optimal adhesion occurs when the film is not too hard and not too soft, but it should again be noted that the film properties are not constant and will alter as a function of the environmental conditions.
Referring to the films in Table 1, the high glass transition temperature of polymer 1 at 30% RH dictates a relatively poor bond strength due to its brittleness, but this measure would increase with rising humidity and as the film is plasticized and becomes less fragile. Conversely, polymer 2 would produce relatively high adhesion at low humidity, which would decline sharply with rising humidity as the film becomes overly soft. A worthwhile formulation approach would seem to involve a blend of both polymers, such that good adhesion can be obtained across a range of humidity conditions.
Summary
A previous article discussed traditional measurements used to assess the properties of hair spray products. However, as has been emphasized here, the properties of polymer films that deposit on hair are not constant and can be altered by a multitude of factors. On the one hand, this provides the formulator a means of manipulating product properties but on the other, performance and aesthetics are at the mercy of environmental conditions. Simple casting of films demonstrates the extreme differences in polymer stiffness that accompany low and high humidity conditions, while well-recognized polymer characterization approaches can be used to quantify these differences. Consequently, one would expect different performances from hair sprays as a function of changing climatic conditions.
There are two additional factors to consider, both of which can provide significant and possibly over-riding influences. The first is polymer concentration, whereby deficiencies in film properties can be overcome simply by using more. The second factor is that the actual deposition of aerosolized polymer solution droplets on the hair is dictated by the actuation properties of the product package. Therefore, variables such as droplet size, spray force and spray angle will dictate deposition and, subsequently, performance. An additional consideration involves the consumers themselves, who clearly can control the level of deposition by spraying more or less.
This reiterates an important and recurring aspect of in vitro testing: the performance of any product is not dependant on the formulation alone, but will be hugely impacted by the manner in which it is used.
References
- TA Evans, Quantifying the performance of hair styling products, Cosm & Toil 129(5) 46-49 (2014)
- TA Evans, Measuring the water content of hair, Cosm & Toil 129(2) 64-69 (2014)
- Modulated DSC: A simple technique with significant benefits, TA Instruments Application Notes, available at www.google.com/url?sa=t&rct=j&q=&esrc=s&source=web&cd=1&ved=0CB8QFjAA&url=http%3A%2F%2Fwww.tainstruments.com%2Flibrary_download.aspx%3Ffile%3DTN34.pdf&ei=rd3HU9CDMseRyAT8v4CYDw&usg=AFQjCNHRPLtOC6h5mMy09LW0F5iDc-clgg&bvm=bv.71198958,d.aWw (Accessed Jul 17, 2014)
- Tensile modulus of plastic film, TA Instruments Application Notes, www.google.com/url?sa=t&rct=j&q=&esrc=s&source=web&cd=1&ved=0CCwQFjAA&url=http%3A%2F%2Fwww.tainstruments.com%2Flibrary_download.aspx%3Ffile%3DTA038.PDF&ei=Ht7HU5S1ONa3yASHv4K4Bg&usg=AFQjCNF0qIbdRe8MGP8sTXG2PdVTyFp-Tw&bvm=bv.71198958,d.aWw (Accessed Jul 17, 2014)
- TA Evans, Measuring hair strength. Part 1. Stress-strain curves, Cosm & Toil 128(8), 590-594 (2014)