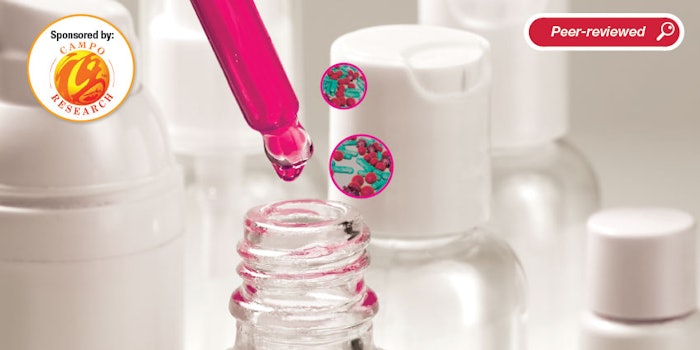
Editor's note: This fourth and final installment in our four-part series provides real-life scenarios of microbial contamination that occurred during cosmetic product manufacturing—and the countermeasures taken.
Follow all four parts, including:
- Part IV, featured here, wrapping things up with a look at filling and microbiological testing;
- Part III, which appeared in June, covering bulk production;
- Part II, debuting in May, which addressed raw material problems; and
- Part I, introducing microbes and growth conditions, appearing in the April edition.
Thanks go to Campo Research for sponsoring the series.
For cosmetic and personal care products manufacturing, various filling methods and machines are used, according to the type of formulation. Generally, a multiple number of pipes, pistons, filling nozzles, etc., are involved, so microbiological control risks tend to be overlooked.
The basic countermeasure response is thorough washing. Sterilization should be considered as insurance. In fact, washing should be completed to a level where sterilization is not required; particularly when chemical sterilization such as alcohol is used since sterilization would not remove dirt, for example, and this can eventually form biofilms.
Also, if there are a number of nozzles and only one is contaminated, any product that went through the contaminated nozzle may escape pre-shipment microbiological testing. Therefore, it is important to properly maintain the condition of all the nozzles.
In reference to microbiological testing, this measure is used to confirm whether raw materials or products have been treated hygienically. Unless the type and number of microorganisms in products are appropriately identified, in a worst case scenario, contaminated products could be continuously supplied to the market. There is also a risk that products without issues are kept from being shipped to market.
As previously stated, the cases in microbial contamination during filling and testing described next are not the exact problems encountered in the manufacturing environment. However, those who understand the limitations of the information provided by microbiological testing and the interpretation of its results can make correct judgements based on these examples and countermeasures.
Issues During Filling
• Problem: Residual washing water in a filling machine caused microbial contamination.
Product at the time of initial filling was contaminated by a large number of microorganisms. It was recognized that the number of detected bacteria declined in the later fillings. We suspected the problem was with the filling process and investigated. We found that washing water remained in part of the mechanical section of a filling nozzle, where bacteria and yeasts proliferated.
Countermeasure: The problem was solved by completely drying the mechanical section of a filling nozzle using clean air.
• Problem: Washing without disassembling the filling machine caused contamination by adaptation bacteria.
Adaptation bacteria were detected in some products but not in others in the same lot. Our investigation revealed that the surrounding parts, including the nozzles, were not disassembled when washing so we believed that residual product liquid and residual washing water caused adaptation bacteria to proliferate in one of the filling nozzles.
Countermeasure: The problem was solved by disassembling, washing and sterilizing the filling nozzles thoroughly.
Note 1: Washing without disassembling means that dirt could remain near the gaskets of connecting parts, which in many cases can lead to the formation of biofilms.
Note 2: In cases of multiple numbers of filling nozzles, contamination can occur in only some of the nozzles. This can be addressed by increasing the number of microbiological tests but before that, by ensuring the microbiological quality of product through thorough washing.
• Problem: Microbial contamination occurred when filling was carried out in another factory.
When part of the filling process was outsourced, only the products that were filled in the outsourced factory were contaminated by microorganisms. We found that washing and sterilization conditions of the filling machine in the outsourced factory were more relaxed than in our internal factory.
Countermeasure: Communicating with the outsourced factory to apply similar microbiological control methods and daily microbial management systems for washing and sterilization conditions as in our internal factory resolved this issue.
Note: Even if an outsourced factory is equipped to the general hygiene level appropriate for manufacturing cosmetics and personal care products, it is important to share information on product property-based washing and sterilization.
• Problem: Contaminated cooling water was introduced into a lipstick molding die.
Molds grew on the surfaces of lipsticks that were stored for shipment. Discoloration and a foul odor were noted. Our investigation revealed that cooling water contaminated by microorganisms spilled into gaps between the die and lipstick bulk material. This occurred during the process in which lipstick bulk material melted by heating was poured into a molding die and the die was cooled with water (see Figure 1).
Countermeasure: The problem was solved by adjusting the cooling water depth and flow rate in order to prevent the water from spilling into gaps between the die and the lipstick bulk material.
• Problem: Condensation in the molding process of a foundation caused microbial contamination.
Microorganisms proliferated on the surface of a foundation that was filled by heating and melting. The lid of the foundation container had been closed and packaged immediately after molding and before solidification. We assumed that condensation caused by cooling during the molding process led to microbial proliferation.
Countermeasure: The problem was solved by closing the lid of the container and package after cooling and solidification were completed.
• Problem: Molds were introduced into products via product containers.
Molds grew in products. Our investigation discovered molds having the same resistance to preservatives as those detected in products in an air cleaner and a device that removed static electricity, both for product containers. The equipment had not been maintained from the viewpoint of microbiological control.
Countermeasure: We regularly cleaned and sterilized the equipment, improved the temperature and humidity control of the filling area, and took other measures to reduce floating mold spores.
Note: Some molds are intrinsically resistant to preservatives. Therefore, if you allow large numbers of them in a production environment, it increases the risk of preservative-resistant molds being introduced into products.
• Problem: Molds grew on a cosmetics inner package.
Darkening caused by molds was found in an embossed part of a cosmetics inner package. A detailed investigation into the production line revealed that condensation occurred in the embossing die of an inner package, and molds grew on the damp inner package.
Countermeasure: The problem was solved by enclosing the embossing process line with an acrylic cover, installing a small fan and controlling temperature and humidity in the filling area to eliminate condensation.
• Problem: Spray products were contaminated due to spray mechanism performance testing.
Bacteria were detected in spray products. No microorganisms were detected in the bulk product before filling. A further investigation revealed that numerous bacteria were detected in spray components. We had been informed that the container manufacturer conducted performance testing with water for all the spray components and shipped them after they were dried. However, we found condensation inside plastic bags of the spray components upon receipt at our factory. This revealed drying was not sufficient.
Countermeasure: In sharing information with the container manufacturer, we learned that quality of the spray mechanism could be ensured by strict control of the manufacturing process. Therefore, we asked them to stop the water tests for all sprays. In instances where performance testing using water was required for their data collection, we asked them to set the tested components aside and to reinforce their controls so as not to mix them with the products for shipment.
• Problem: Spore-forming bacteria in adherence inhibitor for pouch films caused microbial contamination.
Spore-forming bacteria over the specification were detected in hair care pouch products. The number of bacteria in bulk products, however, was within the specification. With further investigation, numerous spore-forming bacteria were detected in a powder-form film adherence inhibitor that was used in the process to rewind the pouch films from a big roll to a small roll.
Countermeasure: The use of adhesive inhibitor was ceased and reserved for a previous generation of pouch film, where necessary, as the current pouch film was made of different materials and did not require the adherence inhibitor.
• Problem: Pouch films were contaminated by microorganisms transported by insects.
Pouch films, which should be extremely clean, were contaminated by microorganisms. Investigations revealed they were contaminated by microorganisms that were transported by insects as the pouches were kept in the warehouse awaiting packaging materials.
Countermeasure: We reinforced measures against insects.
Note: Various microorganisms can attach to the legs and body surface of an insect, which sometimes serves as the transporter for microorganisms. In this case, insect control is the matter to address first, before microbiological control.
• Problem: Spore-forming bacteria were introduced into products from a damaged ceiling.
Spore-forming bacteria were detected in products. Investigations revealed there were gaps in the joints of ceiling panels directly above the filling machine, and spore-forming bacteria with dust continuously dropped onto the machine and were introduced into products.
Countermeasure: We resealed the joints of the ceiling panels to prevent microorganisms from being introduced into products via the filling machine.
• Problem: Ethanol for sterilization was contaminated by yeasts and spore-forming bacteria.
Yeasts and spore-forming bacteria were detected in products. In the manufacturing environment, disassembled parts of a filling machine were sterilized by immersing them in 70% ethanol but the immersion liquid had not been changed for one week and its lid had been left open. Ethanol volatility weakened the sterilizing effect, which led to contamination by yeasts. Spore-forming bacteria also accumulated because the immersion liquid had not been changed, contaminating parts of the filling machine. It was presumed that filling using the filling machine assembled with contaminated parts caused microbial contamination in products.
Countermeasure: We defined in the SOP that the lid of a 70% ethanol container should never be left open in order to maintain its concentration, and the immersion liquid should be changed regularly.
Note: In immersion sterilization, it is important to immerse the parts completely in the sterilizing liquid after disassembling those parts that can be disassembled and washing them sufficiently.
• Problem: Operators washed parts on the floor and not using a washing sink.
In a factory in one country, we often noticed small parts of a filling machine were left uncleaned even though we had developed the SOP on the method of cleaning and had conducted training. It was discovered that in some cases, operators washed larger parts at the exhaust water pit in the floor instead of using the installed washing sink.
Countermeasure: After a series of discussions with local factory workers, the sink was lowered closer to the floor so that operators could sit on low stools while they washed the parts. This idea was inspired by the local practice of sitting on small, low stools or on the floor while cooking and washing clothing. Workers therefore started washing the parts of the filling machine more carefully and the number of uncleaned parts decreased. Also, for larger parts, workers could carry them to the lower washing sink more easily and stopped washing them at the exhaust water pit, in which a large number of adaptation bacteria could exist.
Note: In some cases, organizing the environment from the workers’ point of view so that operators feel comfortable at work can prevail over education and training.
Microbiological Testing
• Problem: Adaptation bacteria cannot be judged by a single test.
A microbiological test on bulk product before filling detected a small number of bacteria but it was within the specification. It was believed that this could be decreased by using preservatives. However, bacteria levels far exceeding the specification were detected in products filled a few days later. A detailed investigation revealed that the detected microorganisms had adapted to the preservatives and developed a resistance.
Countermeasure: Even if the number of detected bacteria is within specification, if they are adaptation bacteria or resistant microbes, they can proliferate at a later stage. Therefore, we tested again after a certain storage period to confirm whether or not they had proliferated.
Note: Adaptation bacteria that exist below the detection limit can pass the microbial test and then proliferate after shipment. Do not rely only on testing. More than anything, it is important to ensure microbiological quality in the manufacturing process.
• Problem: Swarming bacteria appear to be more than the actual number.
During the microbiological testing of raw materials, many microorganism colonies over specification were detected. When we closely observed the media after incubation, we found that a small number of highly swarming bacteria within specification had divided and proliferated while moving around on the media, forming many colonies.
Countermeasure: We shared information among the inspectors about the characteristics of the colony of swarming bacteria (see Figure 2) and about the implementation of an additional confirmation test method using agar overlay medium.
Note 1: The agar overlay medium method involves pouring another layer of medium and solidifying it—after having spread the diluted product liquid onto a monolayer of agar medium. Highly swarming bacteria are blocked in by the agar and cannot swarm.
Note: Sometimes the same phenomenon can occur when excessive water remains on the surface of the medium just after it is created, even if swarming bacteria are not present.
• Problem: Spore-forming bacteria have covered colonies of other bacteria.
As a result of the microbiological testing of a product, we found that a few large, flat, spore-forming bacteria colonies had formed on the medium. We suspected the contamination originated in raw materials and carried out microbiological tests on all of them. The same spore-forming bacteria were found in one raw material, and bacteria that formed small colonies without producing spores were also found in other raw materials. Therefore, we tested products again and as a result of closely observing the cultured agar medium, we found that small colonies were covered over by larger colonies of spore-forming bacteria.
Countermeasure: Since we could miss finding adaptation bacteria, resistant microbes and other harmful bacteria, the inspectors agreed to carefully observe colonies from multiple angles to check whether there are covered colonies.
• Problem: Bacteria are slow to grow in test medium.
When we investigated species of microorganisms in the manufacturing environment by wipe testing in a few hundred places, we found bacteria that potentially degrade product quality. Close investigation revealed these bacteria were difficult to grow in within the usual incubation time duration.
Countermeasure: We immediately reviewed hygiene control of the manufacturing environment and temporarily extended the incubation time for shipment microbiological testing, in order to detect the degrading bacteria found in the environment.
Note: In some cases, the identification of a tiny colony depends on the experience of the inspectors and, occasionally, his/her eyesight. When you encounter a difficult case, it is good for inspectors to adjust their judgement to meet the accurate criteria with colleagues.
• Problem: Colonies turned out to be the crysterization of products.
In microbiological testing, numerous colonies were found on the medium. Our primary judgement was product contamination. However, the colonies did not grow larger with continuous incubation. They turned out to be the crysterization of product ingredients on the medium.
Countermeasure: We established a test flow to confirm, by microscopic observation, when we were unable to confirm a colony after continuing incubation.
Note: In some products that contain low-solubility ingredients, this crysterization phenomenon is recognized.
• Problem: Bacteria that were unevenly distributed in raw materials were overlooked.
Bacterial contamination occurred in products. Various investigations revealed that the contamination source was a raw material that had passed the microbiological test upon receiving. This raw material was a liquid mixture comprising multiple ingredients, and bacteria were unevenly distributed according to the concentration gradient. It was considered that the bacteria just happened to not be detected in the sample that was taken at random, and so contamination was overlooked.
Countermeasure: For the microbiological testing of raw materials with concentration gradient properties, we took samples after stirring, etc., to ensure a uniform state.
Note: Similar consideration is necessary for sampling powder-form raw materials. If stirring is not realistic, multiple sampling points should be used and all samples should be mixed thoroughly in an appropriate manner prior to testing.
• Problem: Contamination by spore-forming bacteria was actually due to contamination at the time of testing.
The laboratory reported that spore-forming bacteria had been detected in the product. However, repeated tests of the same product and the other products in the same lot did not detect the spore-forming bacteria. Investigations revealed that spore-forming bacteria accumulated in 70% ethanol in which a glass cell spreader, i.e., the hand tool used to smoothly spread samples on the agar medium, was immersed for microbiological testing. It was believed that spore-forming bacteria were transferred to the test medium via the cell spreader. The products themselves had not been contaminated.
Countermeasure: The 70% immersion ethanol was changed regularly.
Note 1: If your budget allows, you may have the option of using disposable cell spreaders.
Note 2: This type of contamination is not only limited to spore-forming bacteria. It is worth suspecting contamination during testing when microorganisms are occasionally detected during microbiological testing.
Conclusions
As readers may have noted, all the case studies explained here deviate from basic microbiological control in a manufacturing environment. As we mentioned at the outset of this series, with hindsight, problems such as these turn out to be fairly straightforward once their causes are identified. However, it is not easy to accumulate empirical knowledge from failures, nor to widen its application and firmly establish daily prediction and prevention activities.
To predict and prevent microbial problems, there are many things we should do. These include: identifying and predicting which equipment and operations need improvement; defining challenges and policies and sharing them between related parties; implementing and confirming improvements; and training and regular inspection. As these activities require human resources, time and budget, however, they will have a short-term impact on production efficiency.
For example, when a problem has been resolved, the motivation to maintain and improve the Plan-Do-Check-Act (PDCA) cycle could decline. Staff in charge may also gradually lose focus or maintain their focus but lose support staff, and serious microbial problems may then be repeated every several years. In order to avoid this, it is essential that each division in charge of quality, production, technology, etc., and even the research division determining the preservation systems works together to coordinate and establish a system that can safeguard these activities systematically and sustainably. All of these activities and systems are fundamental to the “quality control culture,” which is an essential element of core corporate values.
Needless to say, products contaminated by microorganisms must never cause health problems to consumers. So, as a starting point, it is crucial for each company to enhance its reliability by establishing a culture to always maintain the microbiological cleanliness required for cosmetics and personal care products in a manufacturing environment. Despite the differences in resources of each company, sharing the basic approaches and best practices is the foundation to reinforce trust in the whole industry.
References
- Toshima, Y., Araki, H., ... Ookawa, M., et al. (2020). Case studies of microbial problems in the manufacturing genba of cosmetics and personal care products. Frag J 48(5) 53-64 (in Japanese).
* The word gemba or genba is a Japanese word that refers to “the actual place or site where value is created.” In the context of this article, it refers to the holistic environment of cosmetic manufacturing, encompassing more than the facility itself. While environment will be used throughout the article, note that the true meaning is deeper. This article is adapted with permission from the original, which appeared in the Fragrance Journal (in Japanese).1