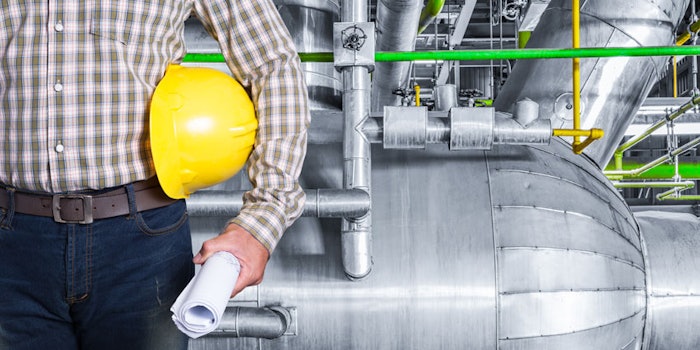
Editor’s note: In cosmetics production, the safe handling of potentially hazardous or flammable materials, as well as the use of the proper equipment, is crucial. The present article offers a refresh on some of these facets of cosmetics manufacturing.
In cosmetics and personal care product manufacturing, potentially flammable and hazardous chemicals such as ethyl alcohol are often stored in 55-gallon or larger drums for dispensing into smaller containers or the point of use.
In addition, manufacturers may receive 10-20 other chemical ingredients for formulations that range from benign to extremely flammable. In high production environments, including contract manufacturing, these raw materials are typically accessed by several different employees throughout the day, over several shifts.
Great care must be taken when workers transfer materials between containers. Mishandling can have serious consequences—from serious health risks to potential inventory loss and facility shutdown. For example, manually tipping chemicals from large drums, often called the “tip and pour” method, is a widespread practice but can lead to overfilling, spillage and even bodily injury due to the weight and awkward positioning required to manipulate the drum.
See related: From the Top, Technical Issues in the Cosmetic Business
In addition, because some chemicals and branded formulations are flammable, hazardous or potentially combustible, the environmental, health and safety directors are often charged with the task of identifying the best type of pump for a given liquid. The utilization of the wrong type of pump can be catastrophic if toxic or highly flammable materials are accidentally released.
Safety Data Sheets
When hazardous chemicals are brought into a facility, they must be accompanied by a safety data sheet (SDS) and Globally Harmonized System (GHS)-compliant labels. The GHS was established by the United Nations to create a unified system for identifying and communicating information about hazardous chemicals.
The SDS outlines details about the material’s potential environmental hazards, what to do in the event of small and large spills, and suggestions for treating injuries related to breathing in or coming into physical contact with chemicals. For example, the SDS for ethyl alcohol, mentions its “extreme flammability” and how, “vapors can flow along surfaces to distant ignition sources and flash back… even minimal static discharge can ignite acetone vapors.”
The SDS additionally identifies required personal protective equipment (PPE) and safe storage guidelines. For flammable and combustible liquids, specifically, depending on the chemical substance, the SDS may also include descriptions of severe injuries, “transgenic” damage to cells and organs, and even the alarming possibility of fatalities in the workplace.
See related: Formulators Can Avoid Quality Disasters
With such dire potential consequences in mind, proper storage and handling are outlined in an attempt to prevent these dangerous situations from occurring. For flammable and combustible liquids, that advice is consistent and unwavering across most, if not all, SDSs.
This advice includes:
- Avoiding breathing fumes or vapors;
- Keeping away from heat, sparks, open flames or hot surfaces (for fear of ignition);
- Keeping containers tightly closed;
- Bring in grounding or bonding devices for the container and receiving equipment;
- Using explosion-proof electrical, ventilating or lighting equipment to prevent ignition sources; and
- Taking precautionary measures against static discharge (another potential ignition source).
To punctuate the point further, most states and municipalities across the U.S. have adopted the National Fire Protection Association (NFPA) 30 Flammable and Combustible Liquids Code and the Occupational Safety and Health Administration (OSHA) 29 CFR 1910.106, which are fire codes that address the equipment, handling, storage and use of flammable liquids. Of course, this is only part of the solution. Ensuring the safe delivery of chemicals also requires proper safety training, the use of PPE and, in some cases, further engineering controls.
Transfer Equipment Requirements
Whether following mandatory rules or guidelines, ensuring the safe transfer of these chemicals means utilizing some type of sealed or closed-loop pump system that will not allow vapors to escape and will also prevent chemicals from coming into contact with the person dispensing them. Fortunately, these types of pumps are available and utilized throughout manufacturing, alongside many other industries that face similar challenges. The systems also must be designed using materials and seals that can withstand extended contact and grounded so as to prevent static discharge.
See related: Scale-up Basics for Formulators and Process Engineers
Highly volatile solvents are especially hazardous because any vapor released can reach ignition sources several feet away and flash back to the liquid. In addition, when transferring flammable liquids from large containers (> 15 gallons) to a smaller container, even the flow of the liquid can create static electricity that could result in a spark—notably, this static electricity build-up is possible whether using a pump or simply pouring the liquid. If the bulk container and receiving vessel are both metal, it is important to bond the two by firmly attaching a metal bonding strap or wire to both containers as well as to ground, which can help to safely direct the static charge to ground.
This is why containers used in the transfer of Class 1 liquid, i.e., those considered flammable with a flash point below 100°F; and Class 2 and 3, i.e., those considered combustible with a flashpoint above 100°F, must be grounded and bonded to prevent electrostatic discharge that could act as an ignition source. NFPA 30 Section 18.4.2.2 requires a means to prevent static electricity during transfer/dispensing operations.
Pump Selection Guidelines and Construction
Chemical compatibility databases and other guidance documents make selecting the correct pump for cosmetics and personal care products manufacturing a straightforward task while maintaining workplace safety. Given the variety of chemicals and branded formulations, it is critical to identify the correct pump for each application. Ultimately, it often comes down to the materials used to construct the pump, as it will come into contact with these chemicals.
Each chemical clearly has specific characteristics, so the selection of the appropriate gasket, housing and hoses is critical not only for safety, but also for the longevity of the equipment. In addition, flammable liquids require that the pump be grounded, as stated above.
To find the right match, cosmetics and personal care products manufacturers can also contact the pump supplier. Established pump manufacturers compile detailed chemical compatibility databases that document the type of pump, gasket and hoses—and whether or not the chemical requires the pump to be grounded. If the chemical is in the database, the pump will often come with a one-year warranty because either it has been tested or compatibility verified by the chemical manufacturer. When a chemical is not already on the list, the pump manufacturer will review the SDS and, if necessary, conduct tests to determine the right pump for the application.
See related: Scale-up Success Requires Compromise
Testing for Chemical Compatibility
In the case of the latter, testing can be performed by simply soaking the standard gaskets for 5 to 7 days in the chemical. When appropriate, vapor tests are also conducted in which elastomer gasket options are suspended over the liquid. The pumps are then fully built and tested with each elastomer. With some complex aromatics, aliphatics and flammable liquids, the plastic pump housing may also need to be tested. This test is a 60-day soak in the chemicals to see if the parts swell or bind with each other, which can cause the pump to fail.
Conclusions
The bottom line for cosmetics and personal care product manufacturers is to bear in mind the dangers of transferring flammable and combustible liquids, which are very real. By following the recommendations of the NFPA, OSHA and other regulatory bodies, personnel can avoid hazards outlined in the SDS that could lead to physical injuries, chronic respiratory ailments and even death. Fortunately, protecting workers from harm can be relatively straightforward with proper safety training, the use of PPE and the use of engineering controls to prevent dangerous spills and chemical accidents.