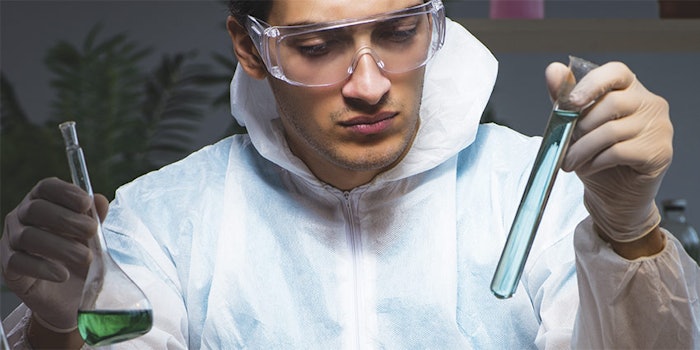
Click through to the Nov./Dec. 2019 digital magazine to read the complete article.
Editor’s note: Of all the interpretations for clean beauty, by far, the most widely accepted refers to products developed with a heightened focus on safety. In consideration of this facet, we present the following overview of product testing for safety, toxicity and irritation, as well as stability.
A product is successful when it sells on the market and brings profit and revenue for the manufacturer. In order for a product to succeed, quality is a crucial factor to gain consumer acceptance. To ascertain the quality of a product, it must be tested based on various parameters; without testing, one cannot be sure of its quality, safety and/or efficacy. The following is a primer for novice chemists and a refresher for more seasoned experts.
Stability Testing
Stability testing evaluates a product’s ability to maintain its original aesthetic, physical and chemical characteristics. It is performed under controlled conditions designed to accelerate a product’s aging. This “early warning system” can indicate problems that may occur with the formulation, package, etc. The results of stability tests can be helpful in many ways—not only to guide the chemist during product development and ensure the product will maintain its aesthetics, but also to determine whether the product will perform as intended and remain safe to use. Furthermore, testing can forewarn the manufacturer of potential problems that could occur after the consumer has purchased the product. Thus, stability testing can help to identify future risks and provide guidelines for future evaluations.
When to test: Stability testing is performed at various stages of development: whenever a new formulation is developed; when qualifying a new raw material; when a modification has been made to the formula or manufacturing process; and when a change has been made to the primary or immediate packaging.
What to test: Stability testing includes assessments of various product parameters. These include compatibility; physical changes that occur over time, i.e., viscosity, texture, color, odor, loss of volatile constituents and uptake of water; chemical changes, e.g., pH, degradation of or interaction between active constituents, microbiological spoilage; and changes that occur in the primary package, such as leakage, corrosion or stress cracking.
Accelerated Tests
To obtain stability data in a shorter timeframe than actual shelf-life, accelerated testing is conducted. This involves exposing the product to parameters including: elevated temperature and humidity, sunlight, condition cycling tests, freeze-thaw tests, mechanical tests and compatibility testing.
Elevated temperature: Storage at an elevated temperature is critical, since the rate of a chemical reaction roughly doubles for every ten degrees of temperature increase. As such, an elevated temperature test can reveal problems sooner than they would appear at room temperature. The drawback of this process, however, is that it may force reactions to occur that would not otherwise happen at lower temperatures.
The most common storage conditions for testing are: 45°C, 54°C, 37°C, 35°C, room temperature and 4°C. It is also recommended to store enough of a sample to make all the observations required as per your specification. At each checkpoint, the product should be examined for parameters including: physical attributes such as color, odor and viscosity; preservative efficacy and the prevention of microbial growth; percentage of actives; and functional attributes.
Elevated humidity: Since many products are adversely affected by moisture, storage at elevated humidity levels is typically a part of stability testing.
In order to establish a frame of reference to determine product efficacy, it is usual to include both positive and negative controls.
Freeze-thaw tests: Subjecting a product to alternate freezing and thawing can be of value to indicate the tendency of products to cloud or crystallize, and to understand the general physical stability of creams, liquid components thereof and other liquid emulsions.
Condition cycling tests: Testing products under conditions that are periodically changed also can impose greater stress on samples than would storage under constant conditions. The following is suggested as a general approach to cycling conditions: 37°C/80% RH, alternating every 24 hr with 20°C/ambient humidity; and/or mean maximum temperature and mean maximum humidity, alternating every 24 hr with 20°C/ambient humidity.
Exposure to sunlight: In cases where products are likely to be exposed to light in the marketplace or during use, it is necessary to investigate the effects of such exposure. In most cases, when sunlight negatively affects stability, the product changes color.
Mechanical tests: The vibration of samples can be useful to assess whether de-mixing is likely to occur in powder or granular products. It can also serve to indicate emulsion stability.
Compatibility testing: Finally, as noted, compatibility testing goes hand in hand with stability testing to highlight any interactions between a product’s contents and its immediate container. Interactions to watch for include: the sorption of formula constituents by the container; the leaching of container constituents into the formula; and adverse effects on the container, such as corrosion.
Safety Testing
In India, cosmetic product regulations of the Consumer Protection Act state that all cosmetics and personal care products should not harm users.1 Similarly, in the United States, adulterated cosmetics, i.e., “those that bear or contain any poisonous or deleterious substance which may render it injurious to users under the conditions of use prescribed in the labeling thereof…” are not permitted, per Chapter 9 of the Federal Food, Drug and Cosmetic Act.2
In Europe, Regulation (EC) No. 1223/2009 states,3 “Cosmetic products should be safe under normal or reasonably foreseeable conditions of use. In particular, a risk-benefit reasoning should not justify a risk to human health.” So, the underlying message is: all cosmetic products must be formulated with the safety of the end user in mind. Safety testing generally involves three types: microbiological, toxicity and irritation/sensitization.
Microbiological: Bacteria, mold and yeasts are everywhere, and most cosmetic products, particularly those containing water, potentially provide food and a hospitable habitat for micro-organisms. If these entities gain a foothold in a product, they will quite likely spoil it and could even present a health hazard to the user.
Since most users would prefer not to keep cosmetics refrigerated, or typically will not use them within two days of purchase as they would do with food, cosmetic products require some form of preservative to inhibit the growth of micro-organisms. Microbes should not be present in a freshly manufactured product; the intent of adding preservatives to the formula is to defend against microbes gaining entry during use; i.e., from consumer interaction or if containers are left open, exposing the product.
Continue reading in the Nov./Dec. 2019 digital magazine...