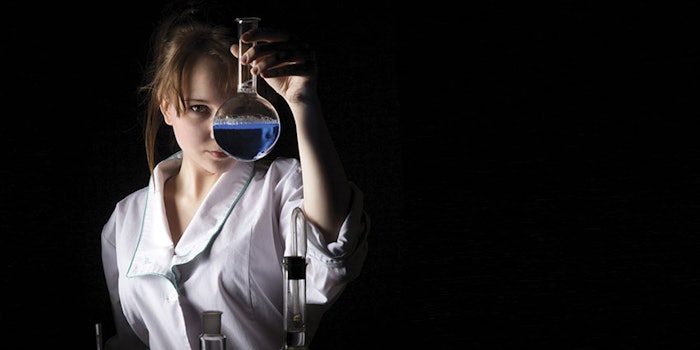
Editor’s note: As most formulators know, emulsions are the basis of products such as hair conditioners and skin moisturizers, among others. They often incorporate emulsifying surfactants to stabilize their increasingly complex systems. With current projections for the hair conditioning market to increase with a CAGR of 5.42% between 2014 and 2019,1 and skin care to surpass $131 billion in 2019,2 formulators will be called upon more than ever to find new solutions to make the immiscible miscible.
Log in to view the full article
Editor’s note: As most formulators know, emulsions are the basis of products such as hair conditioners and skin moisturizers, among others. They often incorporate emulsifying surfactants to stabilize their increasingly complex systems. With current projections for the hair conditioning market to increase with a CAGR of 5.42% between 2014 and 2019,1 and skin care to surpass $131 billion in 2019,2 formulators will be called upon more than ever to find new solutions to make the immiscible miscible.
While the hydrophilic-lipophilic balance (HLB) is the conventional “tool” used, it does not translate to nonaqueous systems. As such, the present article describes a new approach—the cohesive energy ratio (CER)—as a universal means for formulators to characterize surfactant behavior and effectiveness with all liquids to be emulsified.
The empirical expression of hydrophile-lipophile balance (HLB) for aqueous emulsions3 is widely known. More recently, the 3-D HLB4, 5 approach was presented to characterize emulsifiers having silicone, hydrocarbon and/or polyoxyalkylene segments to make o/w, w/o, s/w, w/s, o/s and s/o emulsions; where s represents silicone oils and o, aliphatic hydrocarbon oils. The 3-D expression retained the HLB convention of a 0–20 numerical range for o/w emulsions with the addition of two empirical ranges of 0–20 for silicone-water emulsions and silicone-hydrocarbon emulsions, designated herein as HSB and LSB respectively, where S = silophile.
However, numerous other liquids are immiscible with water, silicone and aliphatic hydrocarbon oils, such as: polyesters, polypropyleneoxide, epoxy resin, butylbenzylphthalate (BBP) plasticizer, aromatic hydrocarbons and other polar oligomers, which can produce non-aqueous emulsions and, accordingly, would require an L1L2B descriptor for each pair of liquids.
The cohesive energy ratio (CER) appears to be a universal balance descriptor. The CER was developed6, 7 to describe surfactants based on the chemical structure of their lipophilic and hydrophilic segments as a quantitative alternative to the aqueous HLB concept. As will be shown, it answers the need for a suitable means to characterize surfactant behavior and effectiveness with other liquids to be emulsified, as expressed in a recent overview on non-aqueous emulsions and their current applications.8 This approach can also be combined with the solubility parameter as a polarity descriptor of surfactant segments and the liquids desired to be emulsified.
Non-aqueous Emulsions
First, consider some fundamentals. Emulsification of two immiscible liquids of differing polarity (LL = lower polarity, LH = higher polarity) is possible if a suitable amphipathic surfactant can be found that will stabilize emulsion particles. Surfactant segments, differing in polarity, provide an amphipathic nature with respect to the two liquids (see Figure 1). They generally lower the equilibrium interfacial tension between the two liquids.
Surfactants used in aqueous emulsions are typically unable to stabilize non-aqueous emulsions because their lipophilic portion is soluble in both liquids. Surfactants intended to emulsify a silicone oil with an organic oil are composed of portions that may be referred to as silophilic and organophilic. An example of an s/o non-aqueous emulsion is 1,000-cs dimethicone in BBP.
Octylphenylpoly-10-ethoxyethanol, a typical o/w surfactant, cannot stabilize such an s/o emulsion because the octylphenyl group is soluble in both liquids. In contrast, a silicone-polyether block copolymer surfactant contains a polydimethylsiloxane silophile, which is soluble in the silicone oil and insoluble in the BBP, and a polyether organophile, which is soluble in the BBP and insoluble in the silicone oil. A highly stable s/o emulsion results from using this type surfactant.
Surfactant Selection
Selecting a surfactant having the necessary amphipathic character to emulsify oil in water is relatively simple due to the large polarity difference of water with most oils. However, establishing sufficient amphipathic character to emulsify two liquids having a smaller difference in polarity can be challenging and requires careful selection.
Matching the LL liquiphile to the LL liquid, and the LH liquiphile to the LH liquid is of critical importance. In relation, the Hildebrand Solubility parameter (δ) has long been used for selecting suitable solvents to dissolve a specific polymer.9 For solution to occur, the free energy of mixing (ΔGm) must be negative; where: ΔGm = ΔHm − TΔSm.
The heat of mixing (ΔHm) is expressed as: ΔHm = Vm(δ1 − δ2)2 φφ; where: δ = solubility parameter, Vm = the average molar volume of solvent and polymer, and φ = volume fraction of each species. The solubility parameter difference (δ1 − δ2) of polymer and potential solvent must be sufficiently small for solution to occur:10 less than approx. 1.7 (cal/mL)1/2 or in SI units, 3.5 (J/cm3)1/2.
However, Hildebrand solubility parameters are not reliable for polar materials. As such, Hansen11 developed a three-dimensional solubility parameter suitable for both polar and non-polar materials. Here, the solubility parameter is treated as a vector having three vector components: dispersion (δd), polar (δp) and hydrogen bonding (δh) partial parameters. These partial parameters define a three-dimensional space, where any solvent is located as a point, and any potential solute (e.g., polymer, oil) has a spherical region of solubility that is centered at its partial parameters with a radius, R. Thus, any solvent located in that region will dissolve the material.
Using Hansen’s solubility parameters, the (δ1 − δ2) term in the heat of mixing equation becomes: (δ1 − δ2) = ((δ1d – δ2d)2 + 0.25(δ1p – δ2p)2 + 0.25(δ1h – δ2h)2)1/2.
Twenty-one combinations of seven liquid organic polymers, of varied structure and polarity, were blended one-to-one in our laboratory and tested for compatibility, i.e., clear versus opaque mixtures, to identify the two regions depicted in Figure 2. Solubility is expected if δ1 − δ2 is less than approx. 3.5 (J/cm3)1/2 for liquids having Vm less than 1,000, and less than approximately 2.0 for Vm less than 10,000. Figure 2 provides a general pictorial description of the effects of the difference of solubility parameter between two molecular species and the average molar volume (i.e., molecular weight) on solubility versus insolubility.
This approach may be used to assess the suitability of potential emulsifier segments with respect to the two liquids desired to be emulsified—i.e., the requirements of Figure 1 are satisfied. The partial solubility parameters for example liquids, lipophiles, hydrophiles, organophiles and a silophile are provided in Table 1,12, 13 where: δ = (δd2 + δp2 + δh2)1/2. Values of PEG/PPG-18/18 were determined in our laboratory.
Establishing sufficient amphipathic character to emulsify two liquids having small differences in polarity can be challenging and requires careful selection.
The CER of Emulsifiers
From this information, an emulsifier may be identified that has an appropriate CER to favor the desired type of non-aqueous emulsion. A broadened CER method utilizing Hansen solubility parameters can then be used to develop block copolymeric surfactants for producing stable non-aqueous emulsions. For simplicity, the present discussion is narrowed to silicone-based emulsions with polar liquids.
The CER equation for silicone-organic emulsifiers becomes:
CER = (VSMS [δd2 + 0.25δp2 + 0.25δh2]S)/ (VOMO [δd2 + 0.25δp2 + 0.25δh2]O)
where S and O refer to silophile and organophile, respectively. MS and MO designate the number of silophilic and organophilic segments in the surfactant molecule. If the molecule is a “rake” or “comb” type of structure, with the silophile as the backbone, MS is one and MO is the number of pendant segments present. Note that CER is dimensionless but one must be consistent in using either CGS or SI units for solubility parameter values.
Applying the CER
Many silicone-organic emulsions were prepared and tested for stability, utilizing block copolymers having a CER of 0.05–10.0 as an emulsifier. In general, a copolymer having a CER of approximately 0.5 is satisfactory to produce s/o emulsions such as dimethicone in PEG or in propanediol. For example, PEG/PPG-18/18 dimethiconea, with its major polyol component and a CER of 0.19, is suitable for this type emulsion. Here, the organophile is a PEG/PPG random copolymer having an approximate molecular weight of 2,600; to be sufficiently silophobic, its molecular weight should be at least 500.
The polydimethylsiloxane silophile must have a minimum degree of organophobicity as well, which is achieved by increasing its molecular weight (see Figure 2, point A). Model emulsions of 1,000-cs dimethicone in a liquid epoxy resin, employing a series of emulsifiers having varied molecular weight silophiles, show that a minimum molecular weight of about 3,000 is needed to provide a stable s/o emulsion.
The liquid epoxy resin and BBP are miscible, and therefore have similar solubility parameters. Thus, a possible correlation between surfactant silophile molecular weight and interfacial tension was examined using BBP and 100-cs dimethicone, due to its much lower viscosity.
The interfacial tension of 100-cs dimethicone with BBP (4.8 mN/m) decreased with increasing silophile molecular weight (see Figure 3). For silophile molecular weights greater than about 2,000, the interfacial tension was approximately 2.0 mN/m.
In contrast, octylphenylpoly-10-ethoxyethanol surfactant had essentially no effect on the interfacial tension (4.7 mN/m). As previously stated, this surfactant is unable to stabilize an emulsion of these two liquids because its octylphenyl group is soluble in BBP (see Figure 2, point B).
In another example, it was not possible to emulsify 1,000-cs dimethicone in PPG-67b liquid using PEG-12 dimethicone surfactant. However, replacement of the PPG-67 polar liquid with a lower molecular weight homolog, PPG-12c, resulted in an excellent white emulsion that was stable at room temperature and at 100°C.
While the polar organic PPG-67 liquid was immiscible with PEG-12, PPG-12 was miscible with the PEG-12 organophile (see Figure 2, points C and D, respectively). Thus, emulsion stability was due to the increased organophilicity of the EO12 segment with the PPG-12 organic liquid, establishing amphipathicity of the surfactant with these two liquids.
Conversely, a CER of approx. 2.0 is optimum for o/s emulsions. In this case, a surfactant having a much higher molecular weight silophile is needed, along with a large organophile. Consequently, the surfactant is highly viscous and is necessarily provided as a solution in a cyclosiloxane.
For example, PEG/PPG-18/18 dimethicone, with its major dimethicone component, in cyclosiloxaned has a CER of 1.7 and effectively stabilizes PEG/dimethicone non-aqueous emulsions. Surfactants such as this are especially suitable for making w/s emulsions, where various water-soluble ingredients may be pre-dissolved in the water. Their extensive use in cosmetic and personal care products was recently reviewed by Starch.14
Liquids to be emulsified must match the right liquiphiles of the emulsifier by assuring similar solubilities and suitable molecular weights.
CER vs. HLB
CER functions much the same as the empirical HLB, as shown by the correlation of CER with HLB provided by Beerbower and Hill (see Figure 4).7 By converting HLB to CER, one may compare the general ranges of surfactant CER used to make aqueous emulsions with silicone-polar organic liquid emulsions made during our research (see Table 2).
It is readily apparent that the CER ranges are essentially the same for both aqueous and non-aqueous emulsions and their invert emulsion types. Thus, CER is a common fundamental descriptor for these two emulsion types and perhaps with any emulsifier for emulsifying any two immiscible liquids.
For example, stable emulsions of mineral oil in liquid polyoxyalkylene (1/1 PEG/PPG) glycols were made using silicone-polyether copolymers having CERs over the range of 0.12 to 0.90. The most stable emulsion was obtained using an emulsifier having 0.34 CER. The CER may also be calculated for various block copolymers of PEG and PPGe. It should then be possible to make non-aqueous emulsions of two immiscible polar organic liquids using the appropriate CER PEG/PPG surfactant, if the necessary amphipathic nature is also present.
Conclusion
While HLB cannot be used for non-aqueous emulsions, CER can be used for any liquid/liquid emulsion. To assure the surfactant has an amphipathic nature with respect to the two liquids, an estimate of the Hansen partial solubility parameters of each liquid and the segments of the surfactant is needed. The liquids to be emulsified must be matched to the appropriate liquiphiles of the emulsifier by assuring similar partial solubility parameters and suitable molecular weights. The molecular weights of such emulsifier segments are then increased, if needed, to enhance liquiphobicity with the other liquid.
The emulsifier CER is then chosen to make the emulsion or invert emulsion. In general, an emulsifier CER of approx. 0.5 for LL/LH emulsions and 2.0 for LH/LL emulsions is satisfactory. Once the amphipathic nature of surfactant with the two liquids is satisfied, the relationship of aqueous and non-aqueous emulsions may be illustrated in two dimensions, as shown in Figure 5. The general utility of CER and solubility parameter for emulsions of any two immiscible liquids is then apparent.
References
- researchandmarkets.com/reports/3339710/global-hair-conditioner-market-2015-2019#pos-0 (Accessed August 2, 2017)
- euromonitor.com/the-future-of-skin-care-game-changing-trends-and-influencers/report (Accessed August 2, 2017)
- W Griffin, Classification of surface-active agents by “HLB,” J Soc Cosmet Chem 1(5) (1949)
- A O’Lenick and J Parkinson, Three-dimensional HLB, Cosm & Toil 111 37-44 (1996)
- A O’Lenick and J Parkinson, Applying the three-dimensional HLB system, Cosm & Toil 112 59-65 (1997)
- A Beerbower and M Hill, The cohesive energy ratio of emulsions—A fundamental basis for the HLB concept, in McCutcheon’s Detergents and Emulsifiers, MC Publishing Co, New Jersey (1971) pp 223-235
- A Beerbower and M Hill, Application of the cohesive energy ratio (CER) concept to anionic emulsifiers, American Cosmetics and Perfumery 87 85-89 (Jun 1972)
- P Thau, Nonaqueous emulsions: History and current specialized applications, Cosm & Toil 8 (Aug 2013)
- J Hildebrand and R Scott, The Solubility of Non-electrolytes, 3rd edn, Dover Publications, New York (1964)
- F Billmeyer, Textbook of Polymer Science, Wiley Inter-science, Hoboken, NJ (1971) pp 24-25
- C Hansen, The three-dimensional solubility parameter—Key to paint component affinities, J Paint Technology 39 (505) 104-117 and (511) 505-510 (1967)
- C Hansen and A Beerbower, Encyc Chem Tech, supp., John Wiley and Sons Inc. (1971); in CGS units
- Zemea (propanediol) Technical Bulletin, DuPont Tate & Lyle Products Co (2017)
- M Starch, Applications of silicones in cosmetic and personal care products, in Y Liu, ed, Silicone Dispersions, CRC Press/Taylor and Francis Group, Boca Raton, FL USA (2017)