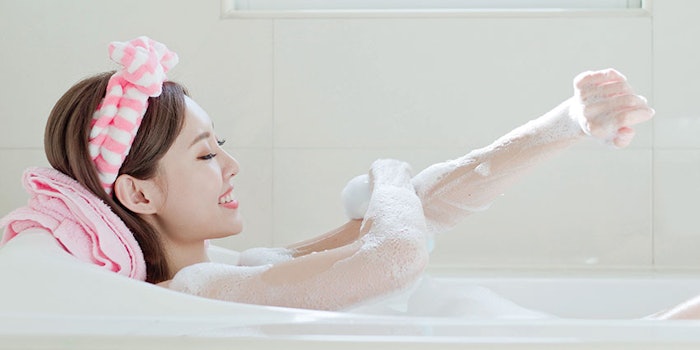
Read the full article in the January 2021 digital edition. . .
Coco-glucoside is a nonionic, naturally derived surfactant in the alkyl polyglucoside (APG) family. Derived from plant sugars and fatty alcohols, it is very mild compared to traditional anionic surfactants. It has become a popular surfactant, acting as a foaming, cleansing, conditioning and viscosity-building agent in liquid cleansers and shampoos. It is also biodegradable and green, with structural similarities to the glycolipids and other biological surfactants.1,2
Chemical Structure
Coco-glucoside has a chemical structure consisting of a hydrophilic monomeric or oligomeric glucoside head group linked to a hydrophobic C12 alkyl tail group, as shown in Figure 1; where n denotes the degree of polymerization. This degree is very low, ~1-2; thus, these materials are referred to as oligomers—olig being Greek for "few" or "little."
Coco-glucoside used in personal care products is a mixture of glucosides, which arises due to the variability in stereochemical orientations of the glucose moieties, polydispersity of oligo-glucoside and varying alkyl chain lengths.3
Chemistry and Properties
Coco-glucoside is produced by combining glucose with fatty alcohol from coconut oil feedstock in the presence of acid catalysts at elevated temperatures.4-6 The fatty alcohol used for synthesis can be obtained either from synthetic (petrochemical) or natural sources (fats and oils). Due to their renewable nature, fatty alcohol blends from natural resources are preferred to build up the hydrophobic part of the coco-glucoside molecule.
The hydrophilic part is derived from both polymeric and monomeric carbohydrates. Polymeric carbohydrates include starch or glucose syrups, while monomeric carbohydrates can be any of the various forms in which glucose is available, such as anhydrous D-glucose, D-glucose monohydrate (dextrose) or highly degraded glucose syrup.1, 3
Coco-glucoside synthesis from polymeric carbohydrates requires higher reaction temperatures to achieve efficient depolymerization and conversion to the glucosides. This process results in degradative side reactions generating undesirable by-products and colored impurities. On the other hand, coco-glucoside synthesized from monomeric carbohydrates such as glucose can be condensed with fatty alcohols at lower temperatures, resulting in a cleaner and higher quality grade coco-glucoside.1, 3
Coco-glucoside is a nonionic, amber, cloudy viscous liquid (2,000 cps at 75°F; crystallizes at < 60°F), with good water solubility due to its hydroxyl groups. The carbon chain distribution for coco-glucoside is usually between C8-14. The cloudiness of the product is due to its magnesium oxide content (max. 500 ppm) and the pH value at which it is supplied. The cloudiness disappears when the pH value is adjusted below 7. The product is usually supplied at 50-60% active levels4-6 and a high alkaline pH, typically around 12, making it self-preserving as-is.
It is stable in neutral and alkaline solutions but unstable in strong acid solutions, in which it hydrolyzes to sugar and fatty alcohol moieties. Since the sugar unit is more water-soluble, coco-glucoside is more hydrophilic than its polyoxyethylene-based surfactant counterparts (e.g., polysorbates). It has an excellent toxicological profile and is biodegradable since it is synthesized from renewable raw materials. It has a high tolerance to electrolytes, exemplifies good synergy with anionic surfactants and is compatible with cationics.
Two Process Variants
The first alkyl-glucoside was synthesized in a laboratory by Emil Fischer in 1893;7 the synthesis of coco-glucoside by the namesake Fisher Process leads to a complex isomer and oligomer mixtures using two process variants—direct synthesis and the two-step transacetalization process (see Figure 2).1, 3, 8-11
In direct synthesis, the carbohydrate reacts directly with an excess of coconut alcohol in the presence of an acid catalyst to form coco-glucoside. The glucose used is often dried before the actual reaction to remove the crystal-water from glucose monohydrate to minimize side reactions that take place in the presence of water. Furthermore, monomeric solid glucose types are used as fine particle solids along with a reducing agent and an acid catalyst. The reducing agent minimizes colored by-products by preventing any oxidative degradation reactions. This process is simpler and cheaper from an equipment point of view, and results in coco-glucoside with an improved odor profile. The ratio of glucose to coconut alcohol is monitored to ensure that the target degree of polymerization range is achieved.
. . .Read more in the January 2021 digital edition. . .
References
- Hill, K., von Rybinski, W. and Stoll, G. (1997). Alkyl Polyglycosides: Technology, Properties and Applications. VCH Publishers, Inc. New York.
- Balzer, D. (1993, Dec 1). Cloud point phenomena in the phase behavior of alkyl polyglucosides in water. Langmuir 9(12) 3375-3384.
- Balzer, D. and Lüders, H. (2000). Nonionic surfactants: Alkyl polyglucosides. Surfactant Science Series 91 Marcel Dekker, Inc. New York.
- The Dow Chemical Company. (Accessed 2020, Dec 15). Technical data sheet: EcoSense 919 Surfactant. Available at: https://www.dow.com/content/dam/dcc/documents/en-us/productdatasheet/324/324-00595-01-ecosense-919-surfactant.pdf?iframe=true
- LG Household & Healthcare. (Accessed 2020, Dec 15). Elotant Milcoside 301V2: Material safety data sheet. Available at: https://www.kalekimya.com/admin/msds/1417089433_NGHS_-_Elotant_Milcoside_301V2.pdf
- BASF Care Creations. (Accessed 2020, Dec 15). Product datasheet: Plantacare 818 UP. Available at: https://e-applications.basf-ag.de/data/basf-pcan/pds2/pds2-web.nsf/D2A40CF69E17C275C12576570041971E/$File/PLANTACARE_r__818_UP_E.pdf
- Fischer, E. (1893. Oct-Dec). Mittheilungen: Ueber die glucoside der alkohole. Euro J Inorgan Chem 26(3) 2400-2412. Available at: https://chemistry-europe.onlinelibrary.wiley.com/doi/abs/10.1002/cber.18930260327
- Kahsnitz, J., Schmidt, S. and Marl, A.O. (1995, Oct). Process for the preparation of alkyl polyglycosides. Patent number 5,461,144.
- Borsotti, G. and Pellizzon, T. (1994, Mar). Process for preparing alkyI polyglycosides. Patent number EP0619318A1.
- Behler, A., Biermann, M., Hill, K., Raths, H.C., Saint Victor, M.E. and Uphues, G. (2001). Industrial surfactant synthesis. Reactions and Synthesis in Surfactant Systems: Surfactant Science Series 100 1–44.
- Fiume, M.M. (2011, Jun 3). Decyl glucoside and other alkyl glucosides. Cosmetic Ingredient Review. Available at: http://www.cir-safety.org/sites/default/files/119_draft_decylg.pdf