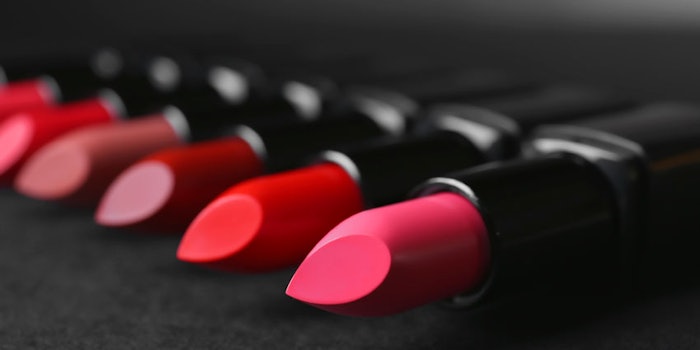
Although a basic lipstick may look like an easy product to formulate, there are as many pitfalls and details that will affect the final product as there are with emulsions. This is not only true for lipsticks, but also for any anhydrous products that require a variety of materials to coincide and achieve homogeneity. Developing these products requires understanding the physical characteristics of the ingredients as well as the mechanical process required to manufacture the product. Two essential material characteristics to consider are the ingredient’s melting point and its solubility behavior.
Log in to view the full article
Although a basic lipstick may look like an easy product to formulate, there are as many pitfalls and details that will affect the final product as there are with emulsions. This is not only true for lipsticks, but also for any anhydrous products that require a variety of materials to coincide and achieve homogeneity. Developing these products requires understanding the physical characteristics of the ingredients as well as the mechanical process required to manufacture the product. Two essential material characteristics to consider are the ingredient’s melting point and its solubility behavior.
Many anhydrous products are mixtures of oils, esters, fatty alcohols, waxes, preservatives, fragrances and various pigments.1 Combining these materials is a complex undertaking, and varying the concentration even slightly changes the dynamics and aesthetics of the final product; in the worst cases, it causes instability. Some examples of this can be seen when formulating lipsticks, solid foundations, lip balms and other hot pour products where melting and pouring into molds or packaging develops the structure. Formulators must therefore pay close attention to several stability parameters, notably sweating, bleeding, separation, streaking and softening.2 All of these issues cannot be addressed, therefore this column will concentrate on crystallization, whose disruption can often lead to some of these instabilities.
Crystallization and Its Disruption
Disruptions in crystal formation have several causes, including raw material incompatibilities, crystal inhibiting factors and mechanical disruption. The most common issues faced by chemists are softening and sweating, which are the results of inhibited crystal formation. These issues frequently occur together and tend to be most troublesome to formulators.
To understand what inhibits crystal formation, the process of crystallization must first be comprehended. It is during the crystallization process that the anhydrous product will develop its characteristics and physical properties. The process involves two discrete steps, nucleation and crystal growth, which are influenced by several factors including molecular compatibility, ingredient structure, nuclei composition and surface properties, and processing conditions.3, 4
Nucleation: There are two distinct types of nucleation, referred to as homogeneous and heterogeneous.5 While homogeneous nucleation consists of relatively uniform and pure substances that can spontaneously initiate nucleation, heterogeneous nucleation involves impure materials that will need to initiate a reaction. For nucleation to take place, a state of supersaturation must exist.
Crystal formation: In the process of crystal formation, several nucleation events occur before enough crystals are formed into micro clusters. These clusters will either re-dissolve or reach a critical size, and if this critical size is stable, a nucleus will form. Once a nucleus is formed, it becomes a convergence point for successive layers of crystals to form, similar to stacking pancakes. If these layers are formed and permeate the mass, the chances of having a stable product are likely. If several nuclei are formed throughout the mass and remain discrete entities without interlocking, then the potential for instability in the finished product is increased.
An ordered, aggregated wax phase is important, as it is usually the primary means of structuring the product and trapping oils from exuding out of the mass. This results in sweating, where droplets of liquid surface on the mass at temperatures ranging from 35–50°C and do not readily reabsorb as it equilibrates to RT.6, 7 In some cases, even wax crystals are exuded to form a thin, white layer; this is commonly referred to as blooming and is occasionally seen in cosmetic products. It is more commonly seen in chocolate bars.
Disruption: There are many ways in which wax crystallization can be disrupted. Described here are: the incompatibility of components comprising the product; the presence of an ingredient that sterically hinders the aggregation of wax crystals around a nucleus; and the mechanical disruption of the product—shearing at or below the crystallization temperature of the system.
Materials or components of materials in formulations that inhibit crystallization and disrupt the ordering of wax crystals are termed crystal poison. These materials retard the crystal formation of a compound that would normally exist in a crystalline state by sterically interfering with the aggregation of wax particles around a nucleus. If crystal poisoning occurs in a product, the end result is usually softening or sweating. This occurs because the primary gellant or structuring agents in most anhydrous products are usually waxes. By disrupting their formation, the product will lack uniformity and correct molecular packing, leading to instability.
In certain instances, anti-freeze proteins (AFP) are useful to inhibit the crystallization of fats and oils; one case that exists in nature is to prevent fats from converting into crystals in certain cold water fish species, such as the northern cod or winter flounder.8 More commonly, glycols are included in personal care emulsions that contain water to prevent crystallization by suppressing the freezing point of the water. Determining whether a system will be stable or unstable requires a systematic approach to the selection of ingredients, solubility testing in the primary solvents, and a methodical approach to testing the interaction of these ingredients. To check for potential future instability, the following challenges should be considered.
Incompatibility
The incompatibility of ingredients has a significant impact on the solubility and ensuing crystallization of waxes. If there is chemical incompatibility, wax crystals tend to be coarse, which is an indication that crystals are not packing tightly enough to prevent oil exudation/sweating.
To avoid such incompatibility, specifically in pigmented products, a step-wise approach must be employed to combining ingredients. Instead of adding all the ingredients at once in a first batch, it is wise to check certain characteristics, mainly solubility and compatibility, by combining certain ingredients in smaller experiments and checking their behavior. Before ingredients are selected, the characteristics and performance of the finished product must be considered. For example, if the objective is to create a long-wearing lipstick, materials with low surface tension such as nonvolatile dimethicone should be avoided.
Once the product’s intention is clear, the primary objective should be to use as few ingredients as possible to achieve the objective. This is invaluable if problems occur during the development process, whether immediately or during production. Each ingredient added to a formulation results in multiple interactions; therefore, subsequent additions increase the interactions significantly, leading to a greater potential for problems. The addition of each ingredient should be systematic, and the structure and function must be considered before it is included in the formula.
The first step is to carefully choose the primary oil/solvent. Each additional ingredient can then be checked for compatibility with the primary solvent, starting with oils. If the oils are compatible, the combination should be crystal clear. Once the oils have been chosen, each wax should be added to the primary oil to look for clarity once the wax is completely melted. Pouring a sample in a metal pan and observing how the wax crystallizes will show compatibility. If the crystallization is homogeneous, a second wax can be added. If the wax crystallizes in clusters with large grainy crystals, there is a potential problem. Adding a co-solubilizer to assist the solubility may be an option with certain ingredients.
Steric Hindrance
As noted previously, steric hindrance to crystal formation is common and caused by the presence of a compound that prevents stacking or interlocking of crystals around the nucleus. These compounds tend to be large and branched. In many instances, they are usually added inadvertently without knowledge of their properties, or formed in situ as a result of processing. The former are usually branched homo, copolymer or block polymeric compounds. The branched group can be as varied as an ester, ether acrylic or methacrylic group, etc. Those formed in situ are more difficult to detect when they occur. One of the most recognized examples of steric hindrance in situ is the reaction of free fatty acids in waxes and aluminum hydroxide that occur in products containing aluminum hydroxide lakes of organic pigments. At elevated temperatures, aluminum hydroxide reacts with fatty acids to form aluminum soaps, which will soften the structure. A higher concentration of soap results in a greater degree of softening. In formulations where high concentrations of aluminum lake pigments are required, waxes with little or, preferably, no free fatty acids should be used.
Mechanical Disruption
Mechanical disruption of wax crystallization occurs when shear is applied to the product at or below the crystallization temperature.7 Movement of the mass due to mixing makes it more difficult for crystals to aggregate around a nucleus and form a macrostructure. The result is the formation of small discrete aggregates that do not interlock to form macro-structures, making the product significantly softer. To prevent this from occurring, the crystallization temperature should be determined by conducting a differential scanning calorimetry (DSC) test (see Differential Scanning Calorimetry Test).9 Once the crystallization temperature is determined, the product should only be mixed several degrees above that point. Conclusion
In some cases, the destruction of crystallization can be prevented with simple modifications such as an increase in polyethylene. The addition of a bentone material or a powder can also help to improve wax lattice stability while increasing the reabsorption of the sweating. Some formulations also combine solvents or oil gellants to bind the oil in the product, preventing them from seeping out. By setting up a proper experimental design, a formulator can control what is needed and identify possible culprits if an instability issue arises. As with many other cases in formulation, it is difficult to predict success until a product is fully developed and tested but understanding the mechanisms to identify solutions can increase the success rate.
References
- J Hollenberg, Color cosmetics, chapter 26 in Harry’s Cosmeticology 8th Ed, MM Rieger, ed, Chemical Publishing Co., Inc, Gloucester, MA USA (2000) pp 523–572
- TS Wang and G Lee, The effect of formulation on the hardness and crystallization of emulsion lipsticks, J Soc Cosmetic Chemist 48 (1) 41–50 (1997)
- DS Grall and RW Hartel, Kinetics of butterfat crystallization, J Amer Oil Chem Soc 69 741–747 (1992)
- P Walstra, T van Vliet, and W Kloek, Crystallization and rheological properties of milk fat, chapter 5 in Advanced Dairy Chemistry, Volume 2: Lipids, Second Ed, PF Fox, ed, Chapman & Hall, London (1994) pp 179–211
- LW Phipps, Heterogeneous and homogeneous nucleation in supercooled triglycerides and n-paraffins, Trans Faraday Soc 60 1873–1883 (1964)
- SY Seo, IS Lee, HY Shin, KY Choi, SH Kang and HJ Ahn, Observation of the sweating in lipstick by scanning electron microscopy, Int J Cosmet Sci, Jun 21(3) 207–216 (1999)
- A Dweck, The Sweating of Lipsticks, Cosm & Toil 96(1) 29–32, (1981)
- Researchers Discover Which Organs in Antarctic Fish produce Antifreeze, Science Daily (Jun 28, 2006) www.sciencedaily.com/releases/2006/06/060628095927.htm (Accessed Aug 20, 2012)
- Thermal Analysis of Lipsticks Utilizing DCS, PerkinElmer Inc., www.perkinelmer.com/CMSResources (Accessed Aug 20, 2012)