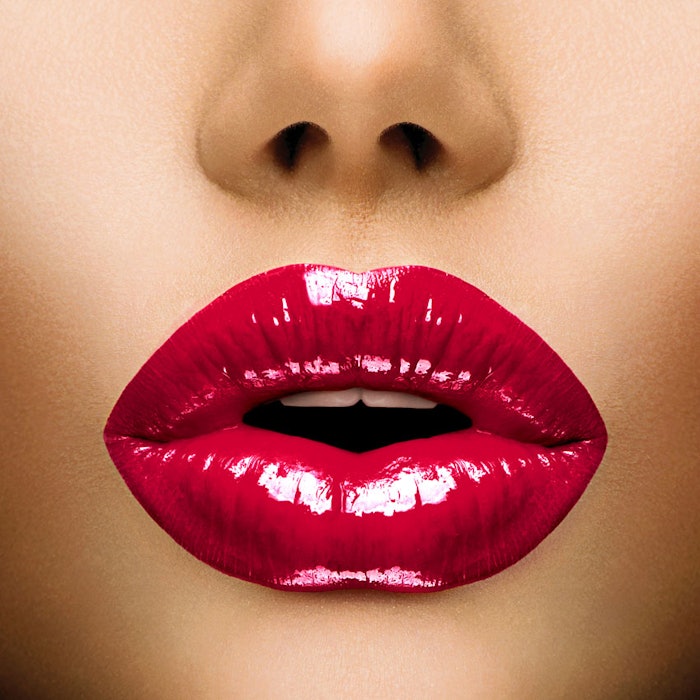
Lip color remains the largest color cosmetic subcategory. Data shows that one in five women uses lipstick every day. While shade is the first selection criteria for all women, the main claims driving sales are brightening/ illuminating and moisturizing the lips, followed by long-lasting color. Other buying trends, although niche, are for specialized skin care-inspired benefits,1 ranging from plumping (11%) and collagen-increasing (2%), to anti-aging (3%), firming (1%) and reducing fine lines and wrinkles (1%). In fact, 69% of Spanish women who use makeup look for anti-aging ingredients, compared to 42% of American women and 32% of British women.2For more on cultural preferences, see the Market Intelligence sidebar.
In any makeup product, pigments play the key role of imparting color and brightening effects according to the trend of the moment. In lipstick, two of the most important functions pigments provide are the aforementioned lasting effect and the shade of the bullet itself, which must match the shade on the lips after application. While formulators have access to a wide range of raw materials to create sophisticated lipsticks, they always face the same technical difficulties of pigment dispersion and final shade matching. To address these challenges and economically improve aesthetics, a new amphiphilic copolymera was developed. The present article explores its effects on lipstick texture, wettability and pigment spreading. Tests are performed using three roll mill and drawdown methods, as well as microscopy. Two lipsticks are compared, with and without the copolymer.
Dispersion and Polymer Design
Cosmetic pigments are typically provided as dry powders, largely consisting of aggregates and agglomerates with a small percentage of primary particles. Aggregates are formed by primary particles of pigment being tightly cemented together by pressure and heat during the pigment production process. Although they are relatively small, they are difficult to break apart. Agglomerates occur when aggregates and primary particles come together. These are much larger than aggregates and not as tightly bound, so they are easier to disaggregate.3
The molecular structure of the copolymer was therefore designed to facilitate the separation of pigment agglomerates based on van der Waals forces, allowing the anhydrous matrix to replace air entrapped in the pigment powder. The copolymer combines octyldodecanol, an emollient used widely in lipsticks for its moisturizing properties and light touch, with VP/hexadecene copolymer, a well-known medium viscosity polymer. The VP/alkyl ratio of the polymer was chemically modified (see Figure 1)4 by increasing the VP amount and the polarity, to break apart agglomerates into smaller aggregates. This results in better, easier and faster dispersion of the pigments, and consequently optimizes the production process, requiring less energy and time.
Materials and Methods
The following studies evaluated the properties of the copolymer in lipstick formulas to determine its effects on pigment dispersion and texture. To assess pigment-wetting effects, three roll mill and drawdown test methods were employed. Viscosity measurements of the pigment dispersions in castor oil also were made. Lastly, effects on dispersion were examined microscopically, and visually in finished lipsticks (see Figure 2).
The test pigments included: titanium dioxide (anatase), D&C Red 7 Ca Lake and yellow iron oxide. Titanium dioxide and D&C Red 7 Ca Lake were chosen because their primary particles are hard and form aggregates and agglomerates that are not easily dispersible. On the contrary, yellow iron oxide is a softer and easier pigment to disperse. Castor oil was used for the pigment premix since it is one of the most commonly used oils in lipsticks. It is low in cost, exhibits good pigment wetting properties, and imparts high viscosity and shine to formulas. For each pigment, two different premixes were prepared: one with 2.5% copolymer and the other without the copolymer.
Three Roll Mill
To put the efficacy of the new ingredient to the test, the premix without the copolymer was passed twice through a three roll mill, whereas the premix with the copolymer was passed through only once. The differences between the premixes, shown in Figure 2, without the new copolymer (a, c and e) and with (b, d and f) were evident. Those without it were viscous and pasty, whereas those with it were more fluid and flowing. It is interesting to note that this phenomenon was more pronounced in premixes containing titanium dioxide and D&C Red 7 Ca Lake, which are more difficult to disperse. This test confirmed that the copolymer better wetted the pigments than premixes without the dispersant. Those with the dispersant were more fluid than the ones without, allowing the three roll mill to disaggregate the larger particles into smaller ones and resulting in better and more homogenous pigment dispersion in the oil.
Drawdown Test
In this experiment, the previous premixes were compared in a drawdown test. Each sample was spread onto a card imprinted with a chart designed specifically to assess film thickness. The cards are white on the upper half to evaluate the masstone of the dispersion, and black on the lower half to evaluate the transparency of the dispersion. Figure 3 shows the results of the tests conducted using premixes of titanium dioxide (a), yellow iron oxide (b) and D&C Red 7 Ca Lake (c) in castor oil, with or without the copolymer.
The left side of each card shows the results of the pigment premix without the copolymer, passed twice through the three roll mill. The right side of each card shows the pigment premix with the copolymer, passed only once through the three roll mill. The differences are evident—the black parts of the drawdown cards show much stronger color with better coverage in the samples containing the copolymer, even though they were passed only once through the three roll mill. These results match those observed with the three roll mill test, confirming better color dispersion and suggesting more brilliant and even coverage in the final product.
Viscosity
The viscosities of the test pigment dispersions were measured under the same conditions using a viscometerb and the results were compared. The viscosity of the titanium dioxide pre-dispersion was 68,000 mPas without the copolymer and 6,000 mPas with the copolymer. The yellow iron oxide pre-dispersion was 35,600 mPas without the copolymer and 22,100 mPas with the copolymer; and the red 7 pre-dispersion was 99,200 mPas without the copolymer and 55,800 mPas with the copolymer (data not shown).
Adding the polymer decreased the viscosities of the samples, meaning the pigments were better wetted and dispersed. This behavior was more evident with the titanium dioxide, indicating the copolymer could also be used to wet UV physical filters.
Microscopy
The described premixes in castor oil also were evaluated using a microscope with 1,000× magnification and LED lighting. Figure 4 shows the premixes of titanium dioxide (a), yellow iron oxide (c), and D&C Red 7 Ca Lake (e) in castor oil without the copolymer, passed twice through the three roll mill. These dispersions are not homogeneous and contain many agglomerates despite the grinding action of the three roll mill and the presence of castor oil, which has good wetting properties. Figure 4 also displays the premixes of titanium dioxide (b), yellow iron oxide (d), and D&C Red 7 Ca Lake (f) in castor oil with the copolymer, passed once through the three mill roll. These dispersions are more homogeneous and agglomerates are disaggregated into smaller particles, giving a more uniform result.
Finished Product Test
A final test was conducted to evaluate the characteristics of the copolymer in a finished formulation, to confirm its functionality not only in singular pigment premixes, but also in a complex anhydrous structure. Two identical formulations were developed (see Table 1), one with 5% copolymer and one with 5% octyldodecanol. The pigment percentages and processing techniques used were exactly the same.
From Figure 5, it is evident that the lipstick on the left without the copolymer has a darker surface than the lipstick on the right. Touching the surface of the lipsticks reveals a lighter color beneath in the lipstick on the left, whereas the one on the right presents no visible difference. This difference in the first stick is due to the lack of pigment dispersion. The lipstick without the copolymer is not optimized, so during molding, some D&C Red 7 Ca Lake particles migrated to the surface to create a darker film. Under this film is the intended color shade.
The consumer buys lipstick based its color, but the non-optimized formula will not impart the color she sees to her lips. On the contrary, the lipstick with the copolymer is optimized, thus eliminating the dark film from forming on the surface, so the resulting color the consumer sees is imparted to her lips.
Conclusions
Independent from specialized trends, the quality and intensity of color remains a key feature for color cosmetics, especially lipsticks and lip gloss. Described here is an amphiphilic copolymer that enables better pigment wetting and dispersion, providing an intense and real color to lipstick formulas.
Acknowledgments: The authors with to express their gratitude to: Fiorio Colori SpA for their support with pigments and the drawdown test and Optika srl for their support with microscopy photographs.
References
- S Invenizzi, Category insights editorial, Lip color cosmetics, Mintel report (May 2014)
- Mintel GNPD database, www.gnpd.com/sinatra/gnpd/category_page/category_id=6#cat_review=20012192 (login required) (2014)
- EB Faulkner, Coloring the Cosmetic World, Allured Business Media, Carol Stream, IL (2012)
- Internal Induchem technical documentation