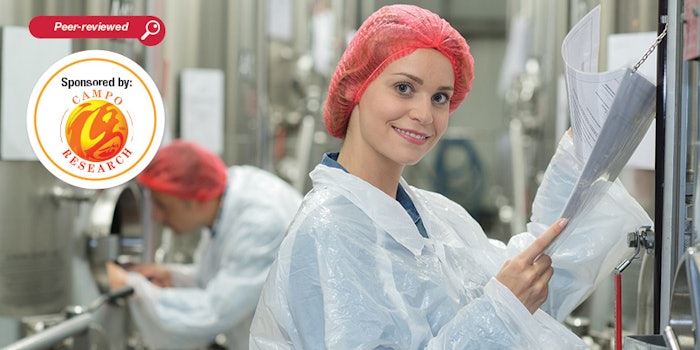
Read the full article in the April 2021 digital edition. . .
Editor's note: Cosmetics & Toiletries is pleased to present this four-part series featuring real-life scenarios of microbial contamination that occurred during product manufacturing—and the countermeasures taken. While all proper manufacturing practices may be followed, microbes are still living entities that adapt to survive, finding pathways into products and causing spoilage, contamination or worse. These case studies can serve as a guide to address and prevent microbial contamination during production.
Manufacturers of cosmetic and personal care products must fulfill their dual responsibility to ensure that the presence of microorganisms is within acceptable limits, both in quantity and quality,2 at the time of purchase by consumers. Companies must also ensure the growth of microorganisms in products does not affect their quality or safety during the intended use. In order to fulfill these responsibilities, preservation system design in product formulations and hygiene control in the manufacturing environment are fundamental—and these two must be highly synchronized.
Sidebar: Versatile, Nature-derived Preservation
Therefore, the first goal in product manufacturing is to design an appropriate preservation system for each given formula. Here, it is important to follow international standards such as ISO 119303 and guidelines issued by industry organizations. At the same time, it is important to use an appropriate palette of preservatives and preservation systems,4 and balance their use levels to maximize efficacy and ensure product robustness against contamination, while also minimizing exposure and potential concerns for human safety.5, 6
A second major goal is to achieve proper hygiene controls in the manufacturing environment, which are described in ISO 22716 Good Manufacturing Practices,7 in the Personal Care Products Council’s (PCPC’s) guidelines,8 etc. These should be used as a model, first and foremost; however, in the cosmetics and personal care manufacturing environment, microorganisms—which are living creatures, desperate to survive—may migrate into production control, sometimes by mutating their very natures, which affords them opportunities.
Many cases of microbial problems in the manufacturing environment will, with the benefit of hindsight, turn out to be pretty straightforward once their causes are identified. However, it can be quite difficult to predict and prevent problems in advance; especially their direct and root causes. Therefore, if the empirical wisdom gained from microbial problems in actual manufacturing environments is superimposed on existing standards and guidelines, this becomes real knowledge with great applicability. As most would agree, “failure teaches success.”
This article series is based on the experiences of authors who have been involved in the microbiological control of cosmetics and personal care products for decades. Here, microbial problems that occurred in manufacturing are put together in the form of case studies. Although most microbial problems are detected in microbiological testing before shipment, serious problems can arise beyond such repetition. Taking to heart the golden rule that “quality is built into the process, not into testing,” this series is meant to serve as a guide to help companies review their daily activities and raise awareness to predict and prevent microbial problems.
Microorganisms in the Manufacturing Environment
In order to explain problem cases and their countermeasures in future articles, it is first useful to review some basic knowledge and terminology that will be used throughout this series regarding microbiological control in the manufacturing environment. Outlined here are relevant microorganisms and their characteristics. Growth conditions are discussed next. Note that for the sake of practicality, in some instances, strict definitions of microbiology are not used, but rather expressions unique to this article series.
Bacteria, fungi (molds, yeasts): The main microorganisms that should be targeted in a manufacturing environment are bacteria and fungi, with the latter being classified into molds and yeasts. Since bacteria favor a high humidity environment, many cosmetic and personal care products can become their breeding grounds. Molds survive more easily in a dry environment than bacteria. These can be introduced into raw materials and products with less water content and can grow. Their growth is often more visually recognizable than that of bacteria.
Certain yeasts are used in the brewing, so some types clearly can grow in an environment where alcohol and salt concentrations are relatively high—even when the water content is low, like that of molds. These microorganisms can be controlled by the general sterilization conditions adopted in a manufacturing environment, such as high temperatures and 70% ethanol. However, microorganisms with resistance to preservatives and other antimicrobial compounds, described later, are much more difficult to control.
For example, in the case of massive microbial proliferation in an intermediate product, if microorganisms are killed by heating during processing and/or by adding preservatives, the product may pass microbiological testing before shipment. However, the product may still contain massive amounts of dead microorganisms, cell compounds and their metabolites, which had never been intended in the product and therefore become a quality assurance risk. As such, microbiological control of an intermediate product is also important.
. . .Read more in the April 2021 digital edition. . .
References
- Toshima, Y., Araki, H., ... Ookawa, M., et al. (2020). Case studies of microbial problems in the manufacturing genba of cosmetics and personal care products. Frag J 48(5) 53-64 (in Japanese).
- ISO (2014). ISO 17516:2014. Cosmetics–microbiology–microbiological limits. Available at: https://www.iso.org/standard/59938.html
- ISO (2019). ISO 11930:2019. Cosmetics–microbiology–evaluation of the antimicrobial protection of a cosmetic product. Available at: https://www.iso.org/standard/75058.html
- ICCR (2019). Report for the International Cooperation on Cosmetics Regulation (ICCR). Overview of key scientific elements and principles to be considered in ensuring access to an appropriate palette of preservatives. Available at: https://www.iccr-cosmetics.org//downloads/topics/2019-10_overview_of_key_scientific_elements_and_principles_-_preservatives.pdf
- Araki, H., Hamada, S., ... Ookawa, M., et al. (2018). An offensive defense: Minimizing preservatives, maximizing protection and resources. Available at: https://www.cosmeticsandtoiletries.com/formulating/function/preservatives/An-Offensive-Defense-Minimizing-Preservatives-Maximizing-Protection-and-Resources-475204783.html
- Araki, H., et al. (2018). An offensive defense: Minimizing preservatives, maximizing protection and resources. Frag J 46(11) 70-77 (in Japanese).
- ISO (2007). ISO 22716:2007. Cosmetics–good manufacturing practices (GMP)–Guidelines on good manufacturing practices. Available at: https://www.iso.org/standard/36437.html
- PCPC (2018). PCPC 2018 microbiology guidelines (PDF download). Available at: https://bit.ly/3dIaxxj
Captions/Footnotes:
* The word gemba or genba is a Japanese word that refers to “the actual place or site where value is created.” In the context of this article, it refers to the holistic environment of cosmetic manufacturing, encompassing more than the facility itself. While environment will be used throughout the article, note that the true meaning is deeper. This article is adapted with permission from the original, which appeared in the Fragrance Journal (in Japanese).