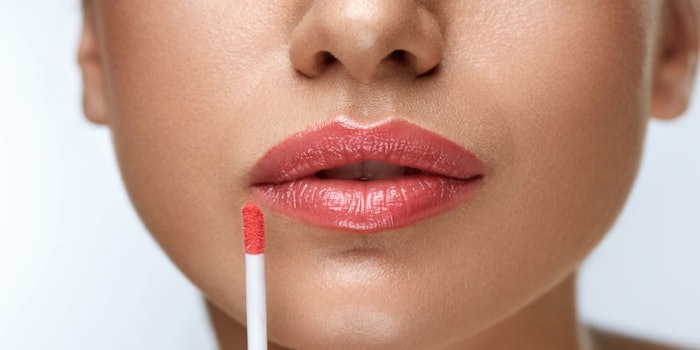
Lip gloss formulas intersect two multidimensional systems: color cosmetics, which include pigments, pearls, waxes and high-shine oil; and lip balm, with soothing, restoring and emollient ingredients. As such, lip glosses face many of the same challenges as these systems. All are used on the same site, and so require the easy and precise application of a relatively thick layer of product. In relation, they must counteract capillary forces around the lips that drive the product into wrinkles. Furthermore, they must take the potential for ingestion into consideration, and provide a positive user experience by imparting a good smell and pleasant taste. Many of these aspects can be combined into one goal: lips that are pleasantly enhanced.
Sensorially, most lip glosses require high shine and luster effects, special rheological properties during application, long-term use, and high plasticity and elasticity. They must also not be tacky. Physically, lip glosses usually are semi-fluid, honey-thick products. For ease of application, they are filled in small bottles and applied using either small brush or flock applicators, or a ball roll-on. In cases where their viscosity at room temperature is high enough, they can be cast into a metallic or plastic container and applied using a small spatula, sponge applicator or the fingertips. In the present article, these major aspects of formulating lip glosses are discussed, and examples are given.
Formula Characteristics
Of all the physical parameters of a lip gloss formula, the most important is its thixotropic behavior. The product should be applicable to the lips with simple movements, and flow easily under the pressure of the applicator or when lips are pressed together; bear in mind that lips have an average temperature of 36-37°C. The layer applied should be thick enough to visually equalize the surface of the lips, leveling wrinkles and roughness to hide and not enhance them. For these reasons, the formula viscosity measured at a low shear rate should be very high, to avoid any unwanted product flow from the lips to the surrounding skin. In other words, a thick, thixotropic fluid should be obtained.
One must also take into account that lips move, and are touched and stretched continuously during the day. Consequently, the applied film should be elastic enough to follow all lip movements without any stiffness or stickiness. Further, the applied film should leave a single smooth line during application, with no additional fluid ingredients appearing as strips along either side of the applied trace. The relatively high viscosity at a low shear rate also is necessary to maintain the stability of the pearls and pigments suspended in the fluid. Lip glosses typically contain low levels of pigment, if at all, since the focus is on gloss rather than color intensity. Nevertheless, when pigments and pearls are present, they should not settle; settling is usually not a problem for products filled in metallic gaskets or glass pots since these are almost solid at room temperature.
Recent studies1 have calculated that an average 15-µm layer of lip balm remains on the lips for about 2.5 hr. During this period, water does not evaporate from the skin and the product works as a sealant, increasing the moisture content in lips. Lips do not have a horny layer but instead are made of a pseudo-mucosa structure, so water evaporation is usually very high—mainly when the surrounding air is cold and dry. However, when the protective layer disappears, water is again lost, and quickly. This explains the need to reapply lip protectants.
An example lip gloss is shown in Formula 1.2 Here, an abundant amount of bulky, lustrous and viscous ester is employed, which is thinned slightly by the stable oil isostearyl alcohol. Like other branched chain compounds, this oil has a high refractive index. The viscous ester and oil combination is supported by the waxy triglyceride, while luster is provided by the combination of two pearls. Low amounts of lake pigments provide some pink color, which is illuminated by the pearls, and stabilizing antioxidants complete the formula. Flavor provides taste for sensory acceptance. The equilibrium between the fluid oil, thick oil and wax determines the final flow characteristics.
Pigments and Pearls
Pigments, coated or uncoated, can be used in variable amounts in lip glosses. They generally are employed at low levels to maintain the transparent or semitransparent look of a gloss, especially if being applied over lipstick. In some cases, stains may also be added to the gloss for lasting color performance, whereas color may be completely omitted in others to impart only luster to the lips.
Many types of mineral and synthetic pearls are used in lip glosses. The difference between them is subtle. Mineral pearls use the mineral mica, while synthetic pearls use synthetically prepared silicates with the same platelet structure as mica. The only natural pearl is guanine, which is not used in lip gloss. Being transparent, the formulas can be enhanced by synthetic pearls, which impart brilliance; glitters are rarely used because they are easily swallowed. In addition, different pearl sizes enable frost-like, pearlescent, icy and/or pearlescent effects.
As with most makeup, pigments are pre-milled into a fluid polar oil—in the case of lip gloss, isostearyl alcohol—while the waxes and oils are blended by slow mixing and heated to 70°C until complete dissolution. Dispersed pigments and pearls are successively added and blended. The formula is then filtered with a metallic sieve to eliminate any foreign materials, analyzed and filled into the final bottles. The only difficulty in this otherwise simple process is the need for perfect and reproducible side-milling of the pigments. This operation requires an adequate wet-milling device and is essential for color-matching reproduction in different batches.
Tackifiers and Thickeners
Due to the desired properties, most lip glosses are anhydrous; and since lips do not have sweat glands, occlusion is not a problem. As described previously, lip gloss formulas essentially are based on one or more viscous oils having a very high refraction index. To obtain the necessary flow characteristics, including brake flow, i.e., stopping flow to eliminate spreading after application ends, these oils must be properly thickened. One category of ingredients to assist in this area is tackifiers, which can also provide high luster to the lips. However, if the resulting flow after their addition is not adequate, more oil thickeners can be added.
Besides the mentioned properties, oil thickeners impart transfer-resistance, skin adhesion, a thick and non-shear thinning application layer and resilience to formulas, along with volume to the lips. They are selected on the basis of their gloss, transparency, flow behavior, polarity, residual feel and, of course, cost. Their performance depends on the nature of the oil blend and additives, the amount used and the temperature during application or storage conditions.
In comparison with the variety of ingredients that thicken aqueous phases, the number to thicken oil phases is meager. Those that are available include organically modified smectic clays; smoked silica with a specific 200 m2/g surface area; β-cyclodextrin derivatives, e.g., palmitate; long chain fatty alcohols; and waxes. Note that metallic soaps such as magnesium stearate are not used because they tend to decrease the gloss effect. Polyethylene polymers or copolymers such as ethylene/propylene/styrene copolymera and butylene/ethylene styrene copolymer (and) isopropyl palmitatea also can be used. Swollen silicone gums having a 60-1,000 x 103 MW are useful in silicone-inspired formulae, as they provide low surface tension, high spreading and gas permeability, and emollient effects, together with luster. Polyglycerin-10 behenate/eicosadioate is another efficient thickener, and rosin derivatives such as methyl hydrogenated rosinate are excellent tack providers—although in some cases, they are not well-tolerated by the skin.
Determining the use levels for thickeners requires balancing the low viscosity required for production at medium-high temperatures, with the viscosity of the cold formula in the final bottle; also, the viscosity at room temperature, for appropriate flow during application onto the lips, with the viscosity of the layer on the lips at temperatures ~36°C, as noted. For this complex of reasons, formulae frequently include two types of thickeners/tackifiers to adequately cover this range of temperatures. As an example (see Formula 2),3 waxes are good thickeners at room temperature while their effects fade at high temperatures. Adding smoked silica helps to protect the viscosity at higher temperatures. Generally, such blends are efficient. The use of wax modified with added emulsifying power also improves the adhesion of the film to the lips, as it improves wetting by the formula. This is a good starting point for trial-and-error in changing the oil blend, finding the right wax, adding other suitable thickener systems, or introducing soothing active ingredients.
Another example, shown in Formula 3,4 reiterates the importance of branched chain hydrocarbons for high-gloss systems. Different molecular weights of the poly-isobutenes provide optimized flow performance. The mineral oil could be substituted with branched chain, glossy and bulky esters such as pentylene glycol neopentanoate, tri-isodecyl trimellitate and octyldodecyl stearoyl stearate, although these are more expensive. Exotic oils such as macadamia seed also could increase the emollient feel and improve lip protection.
Actives and Other Ingredients
Beyond the basics, other ingredient types often are added to lip glosses. UV filters, for one, are incorporated due to the transparency of glosses, which typically affords poor sun protection. Formula 4 provides a good example of this application.5 In traditional formulae, antibacterial agents also were added; although oils are not prone to contamination by bacteria. Also, preservatives do not protect against spores, and swallowing preservatives is unsafe and could lead to allergies. Therefore, avoiding the use of preservatives is recommended in anhydrous systems. In contrast, a good antioxidant system is strictly necessary, as oils dissolve discrete amounts of oxygen, the plastic walls of containers have a discrete permeability to oxygen, and flavors are oxygen-sensitive. Especially when using unsaturated oils, antioxidants are mandatory. Other desired benefits in lip gloss include moisturization and lip-plumping. This latter effect can be physically performed by the film on the lips, although additional moisture organizers such as ceramides or poly-unsaturated lipids can be added. For ingredient labeling’s sake, the so-called “non-additives” are important, and gluten-free is a growing concept; although ingestion is not an issue with other product types, so making this claim appears unwarranted. Furthermore, in the case of lip products, there is a real possibility of ingestion, and use of gluten derivatives is potentially harmful for coeliac individuals.6
Perfumes and Flavor
In the case of lip gloss, perfumes should be referred to as flavor since their effects on the sense of smell are also perceived in the mouth. Fruity notes, e.g., strawberry, as well as mint generally are preferred. The cooling sensation given by mint in particular induces an increased blood flow to the lips, adding a plumping effect. Note that since glosses are generally produced at high temperatures, the perfumes used should be specifically designed for this application. Also, their addition should take place after cooling to 50°C.
Functional Additives
Functional additives added to lip gloss generally include tocopherol and tocotrienols, aloe vera extract and polyunsaturated vegetal oils such as those shown in Formula 5. This formula includes protective ingredients and a non-oily emollient that forms an efficient, lasting film.
Two modern examples7 include developments in gloss using esters (see Formula 6) and oils (see Formula 7). In the first example, propoxylated castor oil takes the place of traditional castor oil. This shiny cholesterol ester gives high gloss, together with the branched chain esters. Viscosity is provided by the modified silica gel. Pigments are milled in the polar oil by a roll mill and heated at 90°C, then silica dimethyl silylate is added. Finally, before cooling, flavor is added. It is evident in this formula that the aim was to increase the apparent size of the lips by the inclusion of an active peptide.
In this second example,8 the oils should be heated to ~90°C until homogeneity. The pearl pigments are then blended in, and the product is discharged after cooling. This formula demonstrates the importance of bulky, brilliant esters and their wise blending to achieve the right balance in a product. Lastly, one must not forget that an applicator-mediated product requires a suitable applicator. A new sponge applicator that is activated by turning the container9 is one of the more recent launches in this innovative field.
References
- https://ecommons.cornell.edu/handle/1813/28296 (Accessed Dec 22, 2014)
- Lip Gloss formula, modified from Croda Inc, Cos &Toil 101 (4)115 (1986)
- Lip Gloss formula, Uniqema, Cosm &Toil 108 (6)75 (1993)
- Modified from Personal Care Magazine 3 (Nov 2004)
- Lip Gloss with Sunscreen formula, modified from Mearl, Cosm &Toil 105(12) 132 (1990)
- www.cosmeticdesigneurope.com/content/view/print/979940 (Accessed Dec 12, 2014)
- Modified from Cosm &Toil 126(5) 384 (2011)
- Modified from SCS Formulate Program and Exhibition Catalog 62 (2011)
- Miracle Skin Transformer Lips Rewind, www.totalbeauty.com (Dec 12, 2014)