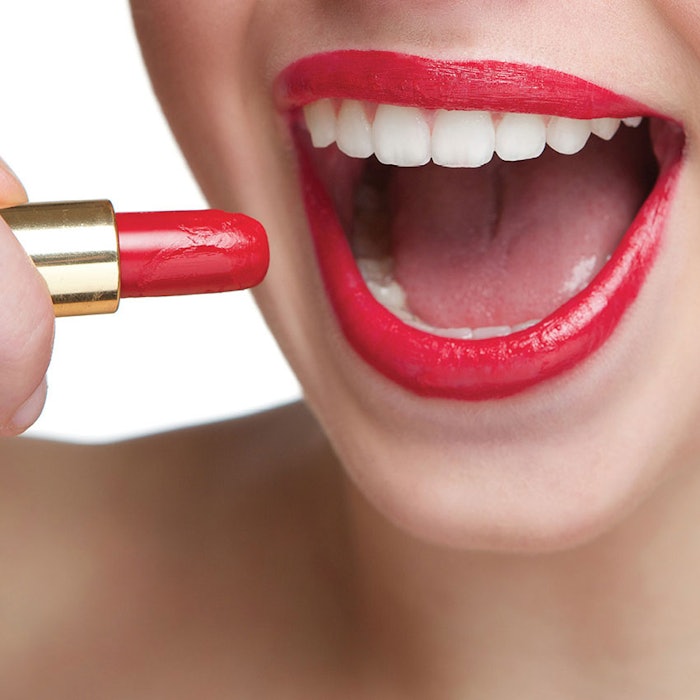
In lipsticks, oils mainly are used to promote wax swelling, pigment wetting and gloss.1 Waxes are esters of long-chain fatty acids reacted with fatty alcohols, and are important for obtaining the desired viscoelastic properties, stick structure and thermal stability.2-4 Pastes aid in the formation of a microcrystalline or gel-like stick structure, increasing the firmness and elasticity of the lipstick.5
Fundamentally, a lipstick must have sufficient stick strength to withstand the force during application, but also have the appropriate pay off characteristics. To optimize these competing traits, several formulation approaches were considered. Due to the number of variables involved, traditional empirical approaches are inefficient for lipstick development. Alternative approaches include Factorial Design, Cross Design and Mixture Design. For lipstick mixtures, where proportions of ingredients are more important than total quantities, the use of Mixture Design was deemed most appropriate.
This article explores Mixture Design for lipstick development. The approach models the blending surface with a suitable mathematical equation to identify the ideal mixture that fulfils the defined responses and their criteria for optimality.6 A key trait of this approach is that the factors, e.g., the ratios of different waxes, must add up to one. Compared with approaches that focus on one variable at a time, Mixture Design, which is capable of assessing several variables concurrently, with a minimum number of observations, can shorten development time and reduce costs.
This study was carried out to evaluate Mixture Design for optimizing the wax and oil phases of a conventional lipstick. It was also provided a better understanding of the complex interactions between waxes and oils, and the effects of those interactions on the final lipstick characteristics.
Materials and Methods
Materials: A simple formulation containing standard waxes, oils, pastes and pigments was used for the described tests (see Formula 1). The proportions of total waxes, oils, pastes and pigments were fixed at 20%, 50%, 15% and 15% w/w, respectively. As benchmarks, two samples from a contract manufacturer and a commercial French product were used.
Sample preparation: In a beaker, all the waxes, pastes and pigment dispersion were heated to 85-90°C until completely melted. The oil was then mixed into the wax mixture. Once the mixture was thoroughly melted and mixed, it was quickly poured into a lipstick mold that was preheated (to 45°C) and lubricated without introducing any air bubbles. The filled mold was conditioned at ambient temperature for 5 min, and then cooled in the freezer at 0°C for 20 min. The mold was removed from the freezer and conditioned at ambient temperature for 5 min. The lipstick samples were then removed from the mold and evaluated the next day.
Experimental design: Commercial Design of Experiment (DOE) softwarea was used to carry out the Mixture Design test. The purpose of Mixture Design is to calculate the values of the responses for all possible mixtures in the chosen experimental domain on the basis of a limited number of experiments. The domain was defined by different ratios of waxes or oils in the lipstick, where the proportions of components (factors) were between 0 and 1.
In this study, Scheffé’s simplex-lattice design was used.7 A total of 13 blend points were produced according to the augmented simplex-lattice design shown in Figure 1. The nine points on the sides of the triangle were used to calculate the coefficients of the model. The simplex was augmented with three interior design points, to allow for prediction in the interior of the simplex area and validation of the model used.
Three points were replicated at random for the estimation of experimental error, giving a total of 16 blend points, as displayed in the experimental matrix (see Table 1). Scheffé’s cubic model was used for modeling the response data (see Equation 1). X1-X3 represent the factor variables, which in this study, were the different waxes or oils tested. The response data obtained was analyzed by means of ANOVA table with a significance level of p < 0.05. The statistical parameters provide information about how well the model fits the responses, the effect of each factor variables and their interactions, as well as the significance of these effects. The experimental study consisted of two stages: determining the wax ratio, then the oil ratio (see Table 2).
Lipstick Characterization Methods
Breaking point measurement: The breaking point was determined by measuring the quantity of water in grams required to break the lipstick. This indicated the hardness of the stick. The bottom end of the stick was secured in a metal piece attached to a stand. A small bucket was then “hung” on the stick, placed as close as possible to the lipstick case without touching it. Water was then allowed to flow from an ampoule flask into the bucket until the stick broke; at which point the release of water was immediately stopped.
The water was then weighed and its quantity in grams determined the breaking point of the stick. Each test was repeated in triplicate, and the mean and standard deviation (SD) were calculated. A standard deviation of below 30 was ensured, to reduce the variance. Finally, the breaking point target was set to 300–400 g.
Softening point measurement: A ring and ball method was used to determine the softening point of the lipstick, which indicates its stability at elevated temperatures. The higher the softening point, the better the lipstick’s stability.
An assembly was prepared by setting the lipstick sample in a ring and then loading it with a metal ball. This assembly was placed on a metal support, immersed in a water bath and heated at a prescribed rate. The temperature at which the ball flowed through the lipstick sample and fell to the bottom of the metal support was recorded. The targeted softening point was between 68°C and 74°C. Duplicate readings were taken for each test sample.
Glide evaluation: The glide performance of the lipstick was evaluated to determine how easy and evenly it spread across the skin. Lipstick was applied on the inner forearm in a standard forward and backward motion three times. A hedonic point scale of 0-10 was used to score its glide performance, with 0 being very difficult glide and 10 being very easy glide. The optimum score range was set from 7–10.
In principle, the lower the oil polarity, the softer the lipstick.
Stage 1A: Optimizing Wax Ratio with HP
When hydrogenated polyisobutene (HP) was used as the base oil, none of the test samples met the targets for breaking point (300 g) or softening point (68ºC) (see Table 3). This indicated HP did not provide hardness and structural stability to the lipstick. It was postulated that this was due to the non-polar nature of HP, which forms swollen crystals with non-polar ozokerite wax, and micelle-like structures with polar candelilla wax and beeswax, which are less rigid than a lipstick containing more polar oil such as sweet almond.5 In principle, the lower the oil polarity, the softer the lipstick will be.
A comparison between different waxes showed that candelilla wax provided higher breaking and softening points than ozokerite and beeswax. This is because candelilla wax contains terpenes, which enable the wax to retain oil within its structure and improve the lipstick’s stability. Beeswax, on the other hand, gave the lowest breaking point due to its soft wax structure, which is contributed by its high ester content and very fine crystal structure.8
Related to low breaking and softening points, all samples showed good glide with scores above 8, with HP giving the highest overall score amongst the test oils due to its branched structure. Additionally, beeswax gave the best glide, in comparison with ozokerite and candelilla wax. This is probably due to the presence of complex polyesters in beeswax that make it highly plastic, imparting flexibility and lubricity during application.9 Overall, the results showed that the addition of HP had a higher influence on glide than the type of wax used. It can therefore be suggested that HP is not efficient as the main stabilizing oil for the lipstick, but could be used in low amounts to improve its gliding properties.
The model graphs below were used to determine the optimum areas of each response. From the contour plots in Figure 2a-b, Figure 3a-b and Figure 4a-b, both the highest breaking point of 270 g and softening point of 56ºC are identified toward higher levels of candelilla wax (CW), as circled. Since a good glide can be found all over the simplex, an optimum area toward higher CW was chosen in order to harmonize the requirements for higher breaking and softening points. Hence, the ideal zones for all responses contained nearly 100% CW and were predicted to have a ~270 g breaking point, a ~56ºC softening point and 8-9 score for glide (see Figure 2, Figure 3 and Figure 4).
Stage 1B: Optimizing Wax Ratio with Octyldodecanol
From the results of stage 1A, oil polarity was known to directly influence stick hardness. Due to the low polarity of octyldodecanol, all test samples were below the targets for breaking and softening points, although their results were generally higher than those of HP (see Table 4). By comparing the different waxes separately, ozokerite showed the highest breaking point (275 g) and softening point (59.5ºC), closely followed by CW. However, when used in combination, a higher level of CW (lipstick 16: 13.33% CW) in the formula gave a higher breaking point than ozokerite (lipstick 14: 13.33% OW). Overall, octyldodecanol gave slightly higher breaking point across all the wax combinations than HP, hence was deemed a suitable secondary oil to aid in the formation of the stick structure.
Generally, octyldodecanol interacts well with all the wax mixtures to provide good gliding properties, except when 20% CW was used. This suggests octyldodecanol does not have good affinity toward CW alone and should be combined with other waxes to achieve the desired glide.
As shown in contour plots in Figure 5, Figure 6 and Figure 7, the best areas were identified toward higher concentrations of ozokerite for a high breaking point, softening point and glide score. The circled best areas were expected to give a ~260 g breaking point, a ~59ºC softening point and a score of 9 for glide.
Sweet almond oil acted as a primary stabilizing oil to promote the structural integrity and stability of the lipstick.
Stage 1C: Optimizing Wax Ratio with Sweet Almond Oil
Compared with HP and octyldodecanol, sweet almond oil generally provided higher breaking point due to its high polarity, which strengthens the structural integrity of the stick (see Table 5). Collectively, observations from stages 1A, 1B and 1C were in line with Takeo’s observation10 that the hardness of oil-wax gel increases with the oil polarity. From Table 5, it can be seen that nine samples met the breaking point target (as highlighted). Here, the individual waxes (lipsticks 1-3) showed similar interactions as with HP, where the breaking point was highest with CW, followed by ozokerite and beeswax. Lipsticks 11, 12 and 16 showed a higher breaking point with more CW than the other waxes combined.
Since CW contains 50% hydrocarbons and 50% esters, the balance of non-polarity and polarity of the wax enables it to form lamellar bilayers and micelle-like structures with highly polar sweet almond oil. These molecular arrangements reduce any movements within the structure and increase stick hardness.5
The softening point also increased slightly with sweet almond oil, compared with HP and octyldodecanol but was still below the target. At 20%, ozokerite gave a slightly higher softening point than CW but when both were used together, they showed comparable results (see lipsticks 7 and 11 in Table 5).
Although lipstick with sweet almond oil generally showed slightly lower glide than with HP and octyldodecanol, it was considered acceptable except for lipsticks 3, 12 and 16, which contained higher amounts of CW. This suggests higher amounts of CW are favorable for stick hardness but this compromise glides. The best glide score was shown in lipsticks 6 and 13, which had higher levels of beeswax and ozokerite at 13.33%, respectively.
Hence, to find the optimum formulation, it was necessary to find a middle ground between the lipstick’s stability and glide properties. These results suggested sweet almond oil acts as a primary stabilizing oil to promote structural integrity and stability of the lipstick. For the contour plots in Figure 8, Figure 9 and Figure 10, the selected areas were predicted to have a higher breaking point of ~419 g and a softening point of ~61ºC with the slightly compromised glide score of ~7.
Determining Optimum Wax Ratio
Since the ideal areas selected for stages 1A, 1B and 1C differed, a compromise between the competing requirements was necessary. In determining the optimum wax ratios, it was deemed important to first achieve the required breaking and softening points, which meant compromising glide properties. Hence, the optimum wax ratio (20%) was determined as 2% ozokerite, 2% beeswax and 16% CW.
Based on this ratio, the predicted responses were calculated from the Mixture Design plots for each stage (see Table 6). In the order from highest to lowest breaking and softening points, the results were: 1C with sweet almond oil > 1B with octyldodecanol > 1C with HP. Glide scores were inversely related to the breaking and softening points.
Stage 2: Optimizing Oil Ratio
From Table 7, a total of seven formulations (highlighted) achieved the breaking point target of 300 g with at least 16.67% of sweet almond oil. Below that amount of sweet almond oil, the lipstick did not meet the target. It was apparent the breaking point increased with higher levels of sweet almond oil while the addition of other oils could reduce this response. Some samples achieved the breaking point target but none met the softening point target of 68-74°C. Nevertheless, the softening point of lipstick was higher when there was more sweet almond oil in the mixture.
Generally, all the oil mixtures tested in Stage 2 interacted well with the waxes to meet the glide target of 7-10. While the highest score went to lipstick 10, containing only HP and octyldodecanol at 33.3% and 16.65%, respectively, the presence of sweet almond oil in the mixture reduced the score to 8-9, to give a more balanced and desirable gliding effect.
From the contour plots in Figure 11, Figure 12 and Figure 13, the best area for breaking and softening points was identified at approximately 70-80% of sweet almond oil. This region was predicted to give a ~361 g breaking point, a ~58°C softening point and glide score of just below 8. The glide score was slightly adjusted in order to correspond with the ideal breaking and softening points.
Determining Optimum Oil Ratio
Using the DOE software, the optimum oil ratio (50%) was calculated to be 38.1% sweet almond oil, 0.75% HP and 11.15% octyldodecanol, with predicted responses of a ~350.8 g breaking point, a ~58ºC softening point and a 7.8 glide score.
New Lipstick Formula and DOE vs. Experimental Results
With the optimum wax and oil ratios determined, a final lipstick formula was proposed (see Formula 2) and prepared. Readings showed the breaking and softening points obtained experimentally were slightly lower than the predicted ones, which may be due to imprecise methods. In terms of glide, the predicted results closely replicated the experimental results.
Overall, the proof of concept was successful despite the slight differences for breaking and softening points. Based on the optimum wax and oil ratios, the softening point of the lipstick was still below the target. Thus, further investigation must carried out to optimize this characteristic by increasing the total wax content to 25%. Also, while the softening point increased slightly, the target was still not met and the glide was significantly reduced. It is therefore suggested the best way forward would be to replace one of the waxes with one having a melting point above 80°C.
Conclusions
The results of this study revealed the quantitative relationship between the hardness of a lipstick, expressed as its breaking and softening point, and its glide performance. The use of Mixture Design made it possible to effectively select the samples with the best overall characteristics on the basis of limited but focused experimental work. For the given range of ingredients, the optimum wax ratio was found to be 2% ozokerite, 2% beeswax and 16% CW, while the optimum oil ratio was 38.1% sweet almond oil, 0.75% HP and 11.15% octyldodecanol, for a total 70% of the lipstick formulation.
This study thus demonstrated the effectiveness of the Mixture Design experimental approach to optimize lipstick formulations and study the effects of a range of ingredients on lipstick characteristics.
References
All websites accessed Feb. 8, 2017.
- http://search.proquest.com.arts.idm.oclc.org/professional/kosmet/docview/766157623/13DD00821DF46BC2067/43?accountid=10342 (requires login)
- happi.com/contents/view_features/2008-02-29/the-physical-chemistry-of-cosmetic-formulatio
- R Sandewicz and G Finkenaur, Lipstick, in ML Schlossman, ed, Chemistry and Manufacture of Cosmetics, vol 2, Formulating, 4th edn, Allured Business Media, Carol Stream, IL USA (2009) pp 433-456
- creative-developments.co.uk/pages/pres/new/33.pdf
- croda.com/home.aspx?s=157&r=267&p=2008
- D Rasch, A Gebhardt J Pilz and R Verdooren, Mixture designs, in: Optimal Experimental Design, R Taylor and Francis, Abingdon, UK (2012) pp 279-289
- stat.rutgers.edu/home/buyske/591/lect09.pdf
- P Riley, Decorative cosmetics, in N Butler, ed, Poucher’s Perfumes, Cosmetics and Soaps, 10th edn, Kluwer Academic Publishers, Dordrecht, London (2010) pp 204-215
- docstoc.com/docs/47410454/BEESWAX-THROUGH-THE-AGES-Koster-Keunen-Global-Supplier-of--Bees-wax
- tandfonline.com/doi/pdf/10.1080/15421406.2012.697420