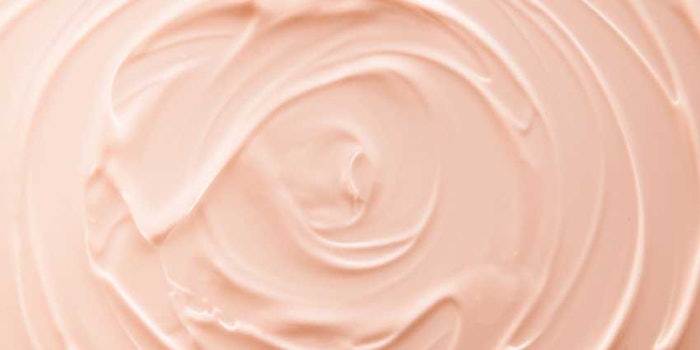
In the development of cosmetic products, rheology modifiers play a priority role in viscosity, appearance and texture, therefore a variety of such ingredients with different characteristics is commercially available. Rheology modifiers can be classified according to their origin and preparation process as: natural, semisynthetic and synthetic.1 Natural polymer rheology modifiers such as xanthan gum, carrageenan and agar are obtained without any chemical modification mainly by extraction. Synthetic and semisynthetic modifiers involve chemical processing via polymerization or grafting. In contrast to semisynthetic modifiers, which involve more complex raw materials, synthetic modifiers including carbomers, acrylates/C10-30 alkyl acrylate crosspolymers, and polyvinyl alcohols typically are prepared by polymerizing low molecular weight compounds such as acrylic acid or vinyl acetate. By controlling the process conditions and monomers used, rheology modifiers with different chemical structures and characteristics can be obtained.
In the fast-moving cosmetics industry, companies include added value materials in their products to differentiate them from the competition;2, 3 examples include skin whitening, anti-aging and natural ingredients. The incorporation of such ingredients brings incompatibilities, though; a typical example occurs with dicationic actives such as L-ascorbic acid magnesium phosphate, which is widely used in skin whitening and anti-aging products. In the presence of electrolytes, its dications can modify the medium ionic strength and act as cross-linking agents between polyacrylate chains, obstructing polymer expansion and decreasing thickening performance—and in many cases, leading to polymer precipitation. In this environment, formulators seek new means to achieve rheology performance.4
One of the greatest challenges and notable deficiencies in the area of rheology modifiers is electrolyte resistance. Figure 1 shows the relationship between the texture and electrolyte resistance of typical rheology modifiers. To address this, blends and complex formulations are used. For instance, xanthan gum or carboxymethyl cellulose rheology modifiers are incorporated, which have higher electrolyte resistance, although they also significantly decrease sensory properties (see Figure 1). On the other hand, the texture of carbomer is significantly better but light and fresh textures are difficult to achieve using it and again, low electrolyte resistance limits its application. In the end, formulators often are forced to choose between the available anionic rheology modifiers and other formula components.
Moreover, the quest for new textures to provide users with a surprising experience is an important yet time-consuming part of formulation. Indeed, the sensory properties of a product are one of the most important factors in its success. To meet these needs and the formulating challenges described, new acrylic rheology modifiers with novel capabilities are being developed,5 two of which are described in the present paper. One is a pre-neutralized sodium carbomer with a fresh texturea, and the other is a highly electrolyte-resistant acrylates/C10-30 alkyl acrylate crosspolymer associative thickener, referred to here as the super electrolyte-resistant (SERK) thickenerb. The properties and efficacies of these rheology modifiers are described and investigated in the present paper.
Pre-neutralized Sodium Carbomer
As noted, due to thickening and texture capabilities, carbomers are widely used in cosmetic products such as creams, gels and emulsions. Despite these benefits, however, manufacturers have expressed the need for improvements in carbomers, such as easier handling and faster dispersion and swelling into water, as well as the capability to give lighter and fresher gel textures. In carbomers, fine particles (< 10 μm) with indefinite shapes (see Table 1) are difficult to flow and disperse into water during gel preparation. Their use typically requires special equipment and slow addition, increasing process costs and time.
In contrast, sodium carbomer provides easy handling, both in solid form and in dispersions. This is due in part to the spherical shape of the sodium carbomer particles (10-20 μm, see Table 1), which flow more easily. As noted, a new pre-neutralized sodium carbomera was therefore developed to minimize lump formation during manufacture (see Figure 2) and bypass the neutralization step, shortening processing time and saving costs. The properties of this sodium polymer were compared with conventional carbomers in aqueous gels prepared by adding water to the concentrations shown in Figure 3.
Note that when dispersed in water, conventional carbomer must be neutralized by NaOH, amines, or citric or lactic acid to reach the desired pH. In the case of the pre-neutralized sodium carbomer, however, the dispersion (gel) already had a pH close to neutral (pH = 6). Sodium carbomer is suitable for use between pH 5 and 10, wherein its carboxylic acids are neutralized to carboxylates—although at pH levels lower than 5, this thickening capability decreases. Further, considering that neutralization of the sodium carbomer is not required, viscosity control can be achieved by adding the sodium carbomer even at the end of the process, resulting in easier manufacturing and process flexibility.
Viscosity: The repulsion between carboxylates expands polymer chains, increasing internal friction and therefore viscosity. This ability to build viscosity and thicken formulations was notably higher than conventional carbomers. As Figure 3 shows, even at low concentrations of sodium carbomer, a significant increase in viscosity was obtained. To gain a better understanding of the flow properties of the sodium carbomer gels, rheology properties including flow curve (see Figure 4) and yield value (see Figure 5) also were measured. While viscosity is a single point in the flow curve graph, i.e., viscosity vs. shear rate, rheology measurements provide more information about the gel’s flow behavior, including performance during application, yield value and storage. As expected, flow curves of 0.5% aqueous gels of sodium carbomer showed shear-thinning behavior typical of carbomers (see Figure 4) and when shear rates increased, viscosity decreased, which would make application to the skin easier.
Sensory properties: The yield value of sodium carbomer (see Figure 5) suggests that its difference in flow, which imparts better sensory properties, seems to lie in a correlation between yield stress and strain (see Figure 6). Yield stress and strain are related to the lightness and smoothness of gels, respectively, and since sodium carbomer gel particles are spherical, they allow easier movement than standard carbomer polymers, lowering yield strain and stress, and therefore imparting a lighter and smoother feel. Moreover, the deposition of the polymer or pilling that occurs when a product is rubbed onto the skin is reduced significantly with the sodium carbomer (see Figure 7 and Table 2).
Rheology: Standard moisture gels were prepared next using the carbomers (see Table 3) and their rheologies were compared to determine whether the beneficial properties of the sodium carbomer observed in the basic gel could be obtained in a more complex formulation. As Figure 8 shows, the yield stress and strain of the sodium carbomer-based moisture gel were significantly lower than those of the conventional carbomer, again showing that lighter and smoother formulations could be obtained using the sodium carbomer.
SERK Thickener
As previously stated, the thickening capabilities and clarity of polymers are affected by the presence of electrolytes such as sodium chloride (NaCl).6 According to the proposed mechanism, the increase in viscosity by a polymer relies on its ability to expand thanks to ion repulsion, but the presence of electrolytes lowers this repulsion. In contrast, the associative mechanism inherent to acrylates/C10-30 alkyl acrylate crosspolymers increases viscosity by decreasing hydrophobic interactions between amphiphilic molecules such as surfactants due to hydrophobic moieties present in the polymer structure. This, in turn, decreases the impact of electrolytes on polymer performance, resulting in an increase in medium viscosity. Considering these mechanisms, as noted, a new SERK thickenerb was designed based on two principles: high thickening capacity in highly ionic mediums, and strong interactions with surfactants; two versions (150C and 300C) were developed to address different formulating challenges such as different salt concentrations or pH levels.
Viscosity vs. NaCl: In order to compare the viscosity of the SERK thickener with carbomer, three gels were prepared; one containing carbomer and the others containing SERK thickener 150C or 300C. Ten grams of polymer were dispersed into 1,000 g of deionized water, 18% NaOH aqueous solution was added to neutralize the dispersion, and each was uniformly mixed. NaCl was then added to the neutralized gels, mixed uniformly, and the gel viscosities were measured (see Figure 9).
While the conventional carbomer exhibited a sharp loss in viscosity and clarity as the concentration of electrolyte increased, the viscosity of gels with the SERK thickeners did not; in fact, they increased significantly. The clarity of the SERK gels also was excellent, even in the presence of NaCl (see Figure 10a). Moreover, the two versions of SERK thickener showed different profiles against NaCl. While the positive effect of salt addition in the case of thickener 300C ranged between 1% and 3%, yielding a maximum viscosity between 0.5% and 2%, thickener 150C had stronger electrolyte resistance, producing a maximum viscosity between 1% and 3% and maintaining high viscosities even at 6% NaCl.
Viscosity vs. pH: The pH ranges where the two SERK thickeners were most effective differed as well (see Figure 11 and Figure 12), and could be modified by the addition of NaCl. Thus, considering the pH and electrolyte concentration required by various formulations, one or the other could be used to overcome the inherent formulation incompatibility of carbomer and electrolytes.
Viscosity vs. other electrolytes: Considering the excellent results obtained in the presence of NaCl, the capability of the SERK ingredient to thicken medium containing L-ascorbic acid magnesium phosphate was tested. As noted, despite interest in formulating with this divalent salt, its negative effects on the thickening capability of carbomers is significantly stronger, making formulation thickening difficult to achieve using conventional carbomers or acrylates/C10-30 alkyl acrylate crosspolymer. Even trace amounts of divalent cations such as Mg2+ or Ca2+ lead to notable drops in viscosity and clarity.
In contrast, the SERK ingredient thickened even in the presence of L-ascorbic acid phosphate magnesium salt (see Figure 13). Furthermore, it enabled the addition of acid to the formula in order to adjust the pH. Following this technique, the pH of the solution containing the divalent salt was raised to above 7, allowing the polymer chain to expand and therefore increasing the viscosity. A weak acid such as citric or lactic could then be back-added to decrease the pH without affecting viscosity.
Viscosity with surfactants: Additionally, a positive effect on the viscosity of the medium thickened by the SERK ingredient was observed with the addition of surfactants. This effect can be explained by the interaction of the hydrophobic moieties present in the thickener with the hydrophobic parts in the surfactant. It is also worthy to note that this effect was significantly higher than that of conventional acrylate copolymers (see Formula 1 and Figure 14).7
Dispersion of pigments: Pigments are widely used in cosmetic products to improve their final appearance. Pearlized shampoos, for example (see Formula 2), are perceived as luxurious and therefore appreciated by consumers. A key factor to obtaining this appearance is pigment dispersion; and fine, homogenous dispersion leads to better gloss and brighter formulations. Unfortunately, solutions using conventional carbomers and acrylates/C10-30 alkyl acrylate crosspolymers generally do not disperse hydrophilic pearl pigments evenly due to their aggregation, which makes dispersing pigments a difficult task. In contrast, the SERK thickener improved the dispersion uniformity of hydrophilic pearl pigments in aqueous solutions and due to this, the final appearance of pearlized SERK gel was significantly better than that of conventional acrylates/C10-30 alkyl acrylate crosspolymers, giving a more lustrous final product (see Figure 15 and Figure 16).
Conclusion
Two new thickeners have been developed. The first, a pre-neutralized sodium carbomer, imparts high thickening and increases viscosity even at low concentrations. Due to its pre-neutralized state, it is also easy to use, giving some flexibility to manufacturing processes and reducing cost; since no neutralization step is required, processing time is reduced. The rheology of the sodium carbomer shows shear-thinning behavior with lower yield strain and stress, resulting in a lighter and smoother texture. Moreover, formulations based on the sodium carbomer generate less pilling.
The second ingredient, a SERK thickener, is highly efficient in high ionic strength medium. It can thicken low pH formulations, ~ pH 5-6, processed by the back-addition of acid without affecting viscosity, even in the presence of divalent salts such as L-ascorbic acid phosphate magnesium salt. It also shows strong interactions with surfactants, leading to significant increases in viscosity via synergic associations. Moreover, the SERK thickener evenly disperses hydrophilic pigments. Not only have the two new thickeners solved some of the most important challenges with anionic thickeners, opening new routes to formulating, they also impart improved properties such as lighter and smoother textures.
References
- M Hayase, Technology and marketing of gelation and stabilization agent, in Gels in Cosmetics (in Japanese), CMC Publishing Co, Ltd, Tokyo (2012) pp 87–94
- Overseas developments of cosmetic industry have large potential (in Japanese), available at www.kagakukogyonippo.com/headline/2013/03/13-10472.html (Accessed Apr 9, 2014)
- C Shimada, Rapid change of cosmetic market with low price—Considering strategy of cosmetic manufactures adding high-value to products (in Japanese), available at http://toyokeizai.net/articles/-/3692 (Accessed Apr 9, 2014)
- H Iwata, Formulas, Ingredients and Production of Cosmetics, CMC Publishing Co, Ltd, Tokyo (2011) p 56
- A Nakatsuka and U Morimitsu, Development of new acrylic thickener suitable for cosmetics (in Japanese), Frag J 40(4) 50-52 (2012)
- The Society of Rheology, Japan ed, Course of Rheology, publication of Polymer Ltd, Kyoto (1992) pp 31–74
- H Yamaguchi, U Morimitsu and A Nakatsuka, Acrylic thickeners, in Technology and Marketing of Gelation and Stabilization Agent, CMC Publishing Co, Ltd, Tokyo (2012) p 104