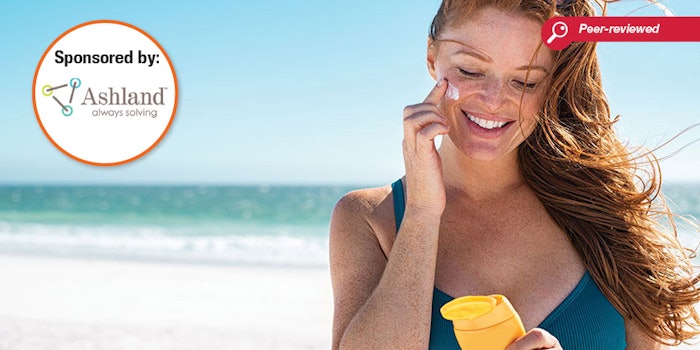
Since the development of the first sunscreen or “attenuation” grades of titanium dioxide (TiO2) and zinc oxide (ZnO) about 35 years ago, these inorganic materials have gradually increased their share of the UV filters market. The advantages of TiO2 and ZnO are well-known: an excellent safety profile, high SPF efficacy, broad spectrum protection and photostability. Despite these advantages, however, the market share for inorganic sunscreens grew slowly to begin with, mainly due to the poorly perceived aesthetics, i.e., skin feel and whitening, associated with them.
Then they were caught up in the “nano debate,” with speculation that the small particles might penetrate through the skin, leading to as-yet-unknown hazards. Fortunately, these concerns have proven to be unfounded, and nano-sized inorganic sunscreens have now been recognized as safe for use in all major sunscreen markets around the world.
A Quickening Trend
In recent years, the use of inorganic sunscreens has begun to increase more rapidly. One recent presentation1 noted the percentage of globally launched sun care products containing only inorganic filters has more than doubled in just five years; from 14.3% in 2014 to 29.6% in 2019, with the biggest jump in 2019 itself. There are several reasons for this surge in popularity:
The natural megatrend: Inorganic sunscreens come from natural mineral sources and are therefore seen as more natural than organic UV filters, which are synthetic chemicals.
Regulatory developments: In February 2019, the U.S. Food and Drug Administration (FDA) published new sunscreen proposals2 naming only TiO2 and ZnO as Generally Recognized As Safe and Effective (GRASE) for use as active ingredients in over-the-counter (OTC) sunscreen drug products. While traditional organic sunscreens remain on the Sunscreen Monograph for now and can continue being used, the FDA has indicated that more data is required to classify these filters as GRASE.
Furthermore, studies commissioned by the FDA have indicated that some organic filters penetrate through the skin and into the bloodstream.3 This has prompted concern over the safety and long-term regulatory future of some organic filters, leading many sun care manufacturers to look to inorganic filters for future developments.
“Reef-safe” claims: Increasing concern that some organic UV filters, particularly oxybenzone and octinoxate, could damage corals has led to legislation in some territories—e.g., Hawaii, Key West, the U.S. Virgin Islands and Palau—banning sunscreens containing these materials. In contrast, current evidence indicates inorganic sunscreens are not harmful to coral.
Technical developments: Advances in the technology of inorganic sunscreens also have made them more attractive to both manufacturers and consumers. Particular improvements have been achieved in transparency on skin, skin feel, efficacy, ease of use and compatibility with other ingredients.
Taken together, formulators are increasingly being tasked with creating new sun care formulations based on TiO2 and/or ZnO. But these materials are not always straightforward to formulate with. This paper will review and update current knowledge on how best to use inorganic sunscreens to develop effective and elegant sunscreen products.
Choice of Active
The choice between TiO2 and ZnO used to be a simple one: TiO2 for UVB protection and high SPF efficacy, and ZnO for UVA protection. However, recent advances in particle design and formulation technology have blurred the lines, somewhat. Firstly, a broad range of TiO2 grades is now available, with different particle sizes and size distributions. For example, Figure 1 shows the attenuation spectra of a conventional sunscreen grade TiO2 alongside a grade with a larger particle size that delivers enhanced UVA protection.4 The latter can give both high SPF and broad spectrum protection by itself, albeit at the cost of increased whitening; note the relatively high attenuation in the visible region.
ZnO has also progressed from being “only” a UVA filter. Advances in ZnO particle technology include “index matching,”5 in which the ZnO particles have a porous structure. This reduces the difference in the refractive index between the ZnO and its carrier medium, thus reducing the scattering of visible light and facilitating a high degree of transparency and efficacy even from relatively large particles. By combining this with SPF boosters in an optimized system (see Formula 1), a high SPF can be achieved with only ZnO as the active. Historically, ZnO has typically given about 1 SPF unit per 1% active but Formula 1 is claimed to deliver an SPF 60 from 25% ZnO, with no additional UV filters.
Another recent development6 involves ZnO particles with a platelet morphology that is claimed to deliver improved coverage on skin and hence greater efficacy. This technology is claimed to typically deliver 1.5-2.0 SPF units per 1% ZnO.
Dispersion vs. Powder
Perhaps the most important decision—beyond the fundamental choice of whether to use TiO2, ZnO or a combination of the two—is whether to use a pre-dispersed form of the particulate or a dry powder. Dispersions hold several advantages:
• Ease of use, in terms of both handling and incorporation into the formulation;
• Worker safety: Note that in some territories, powder TiO2 is now classified as a carcinogen by inhalation. This classification is intended to protect workers handling the TiO2 by compelling the use of appropriate protective measures such as PPE and exhaust systems. With dispersions, there is no inhalation hazard, so these are inherently safer for the workforce; and
• Efficacy: Dispersions usually give higher SPF efficacy than powders, although this does depend on the formulation, and greater stability against particle agglomeration over time, hence maintaining SPF during stability testing.
The main advantage of using powders is cost; powder grades are usually cheaper in terms of cost per % active than dispersions. However, one should also factor in the additional production costs of using powders and also consider whether using a dispersion might facilitate the use of a lower active content to achieve the target SPF. It can sometimes be the case that even though the dispersion option appears more expensive, it can ultimately be more cost-effective.
If using a powder, it is best to include a dispersing agent or dispersant. This is typically a surfactant that helps to wet out the powder in the carrier medium and prevent the particles from agglomerating once dispersed. The optimum dispersing agent depends on the surface properties of the particulate and the medium into which it is to be dispersed. If the medium is an oil phase, typical dispersing agents include polyhydroxystearic acid or polyglyceryl-3 polyricinoleate. Different dispersants will, of course, be required if dispersing into a water or silicone phase.
Dispersant Demand Experiment
The optimum level of dispersing agent to use can be determined by a dispersant demand experiment. Here, increasing amounts of dispersant are added to a slurry of the particulate in the desired medium and after each addition, the viscosity of the dispersion is measured. This gives a “dispersant demand curve,” as illustrated in Figure 2.
The optimum level of dispersant is the concentration at which the viscosity reaches a minimum. To allow a margin of safety, it is usually best to use a slightly higher concentration than that indicated by the minimum point of the curve.
Formulating Maximum Efficacy
Once the active has been selected, the next fundamental requirement to create an effective sunscreen formulation is to ensure the active(s) is/are evenly distributed in the vehicle, usually an emulsion. In the case of inorganic filters, this means the particles must be evenly dispersed, with aggregation/agglomeration prevented as much as possible.
Titanium dioxide: TiO2 is available in both hydrophilic and hydrophobic grades and as pre-dispersions in oil, water or silicone. It can therefore be incorporated in either phase of an emulsion, or even in both phases. In some cases, using a combination of oil-dispersed and water-dispersed TiO2 can be advantageous, as it avoids “overloading” one phase with particles and gives a more even distribution overall (see Formula 2).
Generally, formulating is easier and effective dispersion is best achieved by placing the TiO2 in the external phase, i.e., the water phase of o/w emulsions or the oil phase in w/o systems. However, good results can also be achieved with oil-dispersed TiO2 in o/w emulsions because this helps with the third fundamental requirement for good sunscreen efficacy—achieving good distribution of the UV filter(s) on skin when the product is applied.
When an o/w emulsion is applied to the skin, the external water begins to evaporate, and ultimately what is left on the skin is a film consisting of oils, emulsifiers, actives and any other non-volatile ingredients. In the case of a sunscreen, this film is required to be as continuous and homogeneous as possible, with the active(s) evenly distributed therein. Having TiO2 in the oil phase helps this process.
This part, though, introduces an apparent contradiction: How is it that water-dispersed TiO2 can be effective? Intuitively, one might expect that once the water has evaporated, this TiO2 will have nowhere to go and would agglomerate, thus reducing its efficacy. Fortunately, there are two ways that water-based TiO2 dispersions can still be effective:
Liquid crystal networks: Liquid crystal structures are present in many cosmetic o/w emulsions, formed from lipid emulsifiers such glyceryl or polyglyceryl esters, sorbitan esters, fatty acids and fatty alcohols. Studies have shown7 that aqueous dispersions of TiO2 can be incorporated into these structures, which then form part of the film left on skin after the bulk of the water has evaporated. In this way, the TiO2 can remain well-dispersed on the skin.
Hydrophobic coatings: While it may seem counter-intuitive, some aqueous TiO2 dispersions are based on hydrophobically coated particles, with suitable dispersing agents enabling these particles to be dispersed in water. Thus, when the final product is applied on skin and the water evaporates, the hydrophobic surface of the particles facilitates their incorporation into the oil film on skin.
Zinc oxide: ZnO presents some unique challenges when formulated into o/w emulsions. The solubility of ZnO in water increases significantly below a pH of 6.5; this makes it difficult to make a stable dispersion of ZnO in water, and also reduces its effectiveness as a UV filter when in the water phase. It is for this reason that the vast majority of commercial ZnO dispersions are oil or silicone-based, and ZnO powders are also usually incorporated in the oil phase. However, the hydrophilic nature of ZnO means that even when incorporated in the oil phase, it tends to migrate to the water phase. This manifests as an increase in pH, as Zn2+ ions tend to form alkaline complexes in water.
The following guidelines help to prevent migration of Zn2+ ions to the water phase, and/or mitigate the effects if some migration does occur:
• Control pH: Perhaps the most important point is to ensure that the pH of the water phase is above 6.5, and preferably above 7, when the oil phase containing ZnO is added. A lower pH encourages migration due to the solubility of ZnO in water at such pH, as mentioned above.
• Use a chelating agent: Adding, for example, disodium EDTA to the formulation helps by chelating any free Zn2+ ions in the water phase.
• Consider using a coated zinc oxide: An effective coating prevents migration and pH drift.8
• Use nonionic thickeners such as xanthan gum; avoid ionic thickeners such as carbomers.
• Adjust the pH: If the initial pH after production is > 8, organic acids such as citric acid can be used to adjust the pH to an acceptable range. This should only be done once, immediately after production. Some pH drift may be observed in the following 24-48 hr but usually the pH should stabilize in the range of 7 to 7.5.
In w/o emulsions, the situation is simpler. Here, the evaporation of the water, as it is enclosed in droplets, is much slower and the film on skin can be considered the emulsion itself. As the oil phase is the continuous phase, it is logical that incorporating inorganic sunscreens in the oil phase usually gives the best efficacy. In fact, w/o emulsions in general tend to give higher SPF efficacy from inorganic sunscreens, compared with o/w systems.
Also, in the specific case of zinc oxide, there do not appear to be any problems with migration to the water phase in w/o emulsions, which makes them easier to formulate than o/w emulsions with ZnO. Guidelines for achieving optimal efficacy with inorganics in w/o emulsions include:
• Determine the optimum phase volume fraction for stability; often oil the phase amount is higher than if no particulate were present;
• Use low concentrations of emulsifiers; polymeric emulsifiers are preferred; and
• Add waxes or other rheological aids to improve SPF—however, too much wax can have an adverse effect, so the optimum amount for any given system must be determined by experiment.
Optimizing Cosmetic Elegance
In sun care, it is tempting to think that efficacy and aesthetic appeal are separate and even mutually exclusive objectives. Formulators including this author have often said to marketers that some compromise on cosmetic properties must be accepted if efficacy is to be optimized, or vice versa. Certainly, there are cases where this is true, at least if we think of efficacy just in terms of passing the clinical SPF and UVA tests. However, in the real world, efficacy and elegance are intimately linked.
Among the reasons most frequently cited by consumers for the under-use or complete avoidance of sunscreens are aesthetic issues; for example that the products feel too greasy or sticky, or they make the skin look shiny or leave a white residue on skin. It can therefore be expected that products with improved aesthetics encourage consumers to apply more product and therefore get closer to the labeled SPF. Conversely, maximizing the efficacy of the actives enables high SPF products to be created with minimal levels of UV filters, which allows the formulator greater freedom to optimize skin feel.
Transparency: With inorganic sunscreens, one of the most important aesthetic elements is transparency on skin. Achieving this is primarily dependent on the particle design, discussed earlier in this article. The formulator’s role in achieving transparency is to ensure that the particles remain as close as possible to the designed particle size and size distribution; in other words, that they remain well-dispersed. Since this is also critical for good efficacy, it follows that good efficacy and good transparency often go hand-in-hand. It is also worth noting that, weight-for-weight, ZnO is significantly more transparent than TiO2, which perhaps suggests another reason for the increasing trend for ZnO-only formulations.
Skin feel: The other aesthetic issue to be addressed with inorganic sunscreens is skin feel. Parameters relating to particulate filters that might be expected to influence skin feel include particle size, surface treatments and, in the case of dispersions, the carrier medium in which the particles are dispersed. Of these, the surface properties of the particles are particularly important. The right surface treatment can go a long way toward optimizing skin feel. Inorganics with a hydrophilic surface tend to impart a “dry” skin feel, which can be perceived as “draggy” when the particles are dispersed in the water phase. This effect is lessened when the particles are dispersed in the oil phase, particularly if an effective dispersing agent is included.
Particles in which the primary surface coating is already hydrophobic, however, generally give a more preferred skin feel. In one interesting example9 a transparent TiO2 grade similar to that described earlier was surface-treated with a three-part coating system comprising an inorganic silica coating, a hydrolyzable bifunctional silane and a hydrophobizing agent. A dispersion of this TiO2 was incorporated into a w/o emulsion, which was then compared against the same formulation prepared with a TiO2 dispersion of the same particle size distribution but in which the coating consisted of alumina and aluminum stearate. The two formulations were assessed by a trained panel using descriptive sensory analysis. The formulation containing the silane-coated TiO2 showed the following characteristics, in comparison with the alumina/stearate coated material:
- Higher spreadability during rub-out;
- A higher wetness score during rub-out;
- Quicker absorbance;
- Much lower gloss in the after-feel, both immediate and after 20 min; and
- Less oily and more waxy in the after-feel, both immediate and after 20 min.
In summary, the new coating was superior in several characteristics that are desirable for modern sun care products.
Summary
Market trends, regulatory issues and safety/environmental concerns are driving the increasing use of inorganic actives for sun protection. Technical improvements to these materials are helping to optimize efficacy and cosmetic elegance but the formulator still has an important role to play in converting these developments into effective and aesthetically pleasing end products.
References
- Croda (2020, May 13). Solar formula TiO2 fundamentals. Available at www.crodapersonalcare.com/en-gb/technical-library/webinars (data from Mintel GNPD).
- FDA (2019, Feb 26). Sunscreen drug products for over-the-counter human use: Proposed rule. 84 Federal Register (FR) 6204.
- Matta, M.K., Zusterzeel, R., Pilli, N.R., et al. (2019). Effect of sunscreen application under maximal use conditions on plasma concentration of sunscreen active ingredients: A randomized clinical trial. JAMA 321(21) 2082–2091; doi: https://doi.org/10.1001/jama.2019.5586
- Staniland, P. and Hewitt, J.P. (2010, Sep). Meeting the UVA challenge: Inorganic-only sun protection. Cosm & Toil 125(9) 32-38.
- McCormick, P., Fletcher, R. and Jones, C. (2010, Feb). Micron-sized zinc oxide dispersion for transparent, high SPF formulas. Cosm & Toil 125(2) 50-57.
- Suvaci, E,, Kesim, T., Sapan, Z. and Kang, C. (2019 Apr). A clear choice for UV protection. SPC 92(4) 70-72.
- Dahms, G.H. (1992, Oct). Formulating with a physical sun block. Cosm & Toil 107(10) 87-92.
- Hewitt, J.P. (2017, Sep 16). Zinc oxide: New opportunities with an old sunscreen. Presentation at the Florida SCC Sunscreen Symposium, Lake Buena Vista, FL.
- McNeil, K., Sayer, R. and Miles A. (2014). Assessing the sensory performance of novel coating technology. SÖFW 140(7) 2-7.