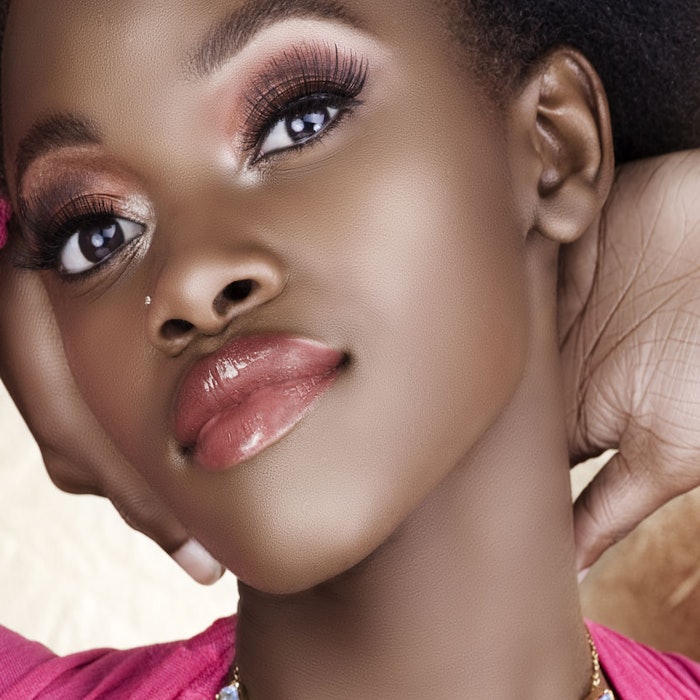
Although each cosmetic formulator has their own toolbox of ingredients to attain the desired product endpoints, versatile ingredients that provide multiple benefits are commonly favored. Obtaining the desired feel and performance in a formula has been greatly simplified by the evolution of silicone chemistry. Silicones have been popular cosmetic ingredients for decades, and have led to innovative textures in skin care and makeup. Though silicones began as basic linear polymer systems of polydimethylsilocane (INCI: Dimethicone), or more volatile, shorter cyclic silicones such as cyclopentasiloxane, technologies have evolved to develop various forms from these main backbones. Derivatives that were made from phenyl substituted silicones, such as phenyl trimethicone, also gave the industry more options for less volatile applications, compared to most linear systems.1
Log in to view the full article
Although each cosmetic formulator has their own toolbox of ingredients to attain the desired product endpoints, versatile ingredients that provide multiple benefits are commonly favored. Obtaining the desired feel and performance in a formula has been greatly simplified by the evolution of silicone chemistry. Silicones have been popular cosmetic ingredients for decades, and have led to innovative textures in skin care and makeup. Though silicones began as basic linear polymer systems of polydimethylsilocane (INCI: Dimethicone), or more volatile, shorter cyclic silicones such as cyclopentasiloxane, technologies have evolved to develop various forms from these main backbones. Derivatives that were made from phenyl substituted silicones, such as phenyl trimethicone, also gave the industry more options for less volatile applications, compared to most linear systems.1
In the past, the silicone’s molecular weight would dictate its viscosity and utility within formulations whereas today’s technologies can provide differentiated benefits with a range of volatilities and physical characteristics. Specifically, elastomer chemistry created by cross-linking linear polymers has been a significant development in the cosmetics industry. Advances in silicone emulsifier chemistries also have expanded the capabilities of silicone elastomers in formulations and extended their use.2, 3
Elastomer Attributes
The introduction of silicone elastomers to the cosmetics industry offered unique replacements and modification properties for traditional high oil and fatty alcohol systems, which dominated formulations for most of the 20th century. This allowed formulations to deliver exceptional aesthetics while providing additional benefits such as soft focus and line-filling, without the oiliness attributed to traditional systems.
When linear polymers are chemically altered into a cross-linked matrix, the resulting elastomer becomes insoluble in most solvents. As such, silicone elastomers can swell in a solvent vehicle with varying expandability that is proportionate to the number of cross-links present in the elastomer. In many cases, these elastomers create a mattifying effect upon application, providing a smooth, soft and even skin appearance. Elastomer powders also provide distinctive aesthetic properties that can range from smooth and silky, to powdery with a dry yet soft finish.
Another desirable attribute provided by silicone elastomers is sebum absorption.4 They also reduce the risk of overdrying and irritating the skin, compared with alcohol and other lipid-stripping solvents, making silicone elastomers a popular choice for anti-acne products. In relation, silicone elastomer materials have a low irritancy profile and provide a safe barrier on the skin. This low irritancy is true for most silicones, and silicones can be found in the medical field due to their safety profile.5
Elastomers can also entrap actives or fragrances in their matrix, enabling the elastomers to act as delivery vehicles within formulas. The release of an active or substance from the matrix can be stimulated by shear or by diffusion when applied on the skin. Besides personal care applications, it is common to see silicone elastomers embedded into skin treatment patches and other devices for this delivery function.
Depending on the chemistry and process to make them, silicone elastomers are referred to as silicone crosspolymers, dimethicone crosspolymers, dimethicone/vinyl dimethicone crosspolymers or polysilicone modified silicone.3 Commercially available silicone elastomers are offered in both gel and powder forms. They can be designed as hard or soft, for use in product types ranging from compact makeup to serums.
Elastomer Powder Formulation
Silicone elastomer powders provide many options for the modification of tactile and sensorial product characteristics. Formulators should be aware of certain interactions and solvency issues within the formulation. For example, high oil levels and certain plasticizer materials may diminish the elastomer’s oil- and sebum-absorbing properties by prematurely binding with them within the formula.
The elastomer powders can be added at low levels, i.e. < 5%, at various stages of the manufacturing process, most typically toward the end of dispersion or emulsion. If used at levels above 5%, proper dispersion must be ensured to avoid agglomerated particles within the product.
The amount of other powder ingredients present, such as silica or spherical particles, also can affect the addition of silicone elastomer powders. Also, although a lab-scale formula batch incorporating silicone elastomers may be mixed easily, manufacturing-sized batches using larger amounts should be mixed in stages or wetted out. In cases such as this, formulators may need to disperse the raw material in a solvent to ensure it is properly mixed into the formulation, and to prevent overmixing the emulsion.
Elastomer Gel Formulation
Silicone elastomer gels offer some of the same sensory and viscosity benefits as powders but with a different set of challenges, since they directly affect the emulsion formation of the product. While traditional versions placed the burden on chemists to successfully stabilize and disperse these materials into systems, newly available micro-dispersions and pre-emulsified suspensions make them far more feasible for large-scale product manufacturing.6
Silicone elastomer gels can contain silicones of varying volatilities, which provide a wide choice of textures to formulators. Typically, the more volatile the silicone, the lighter and less residual its elastomer gel will feel during formulation.7 Silicone elastomers can also contribute to the product’s structure and viscosity, allowing the formulator to avoid tacky thickeners, which impede luxurious textures.
Elastomer Blend Formulation
For silicone oil-based elastomer and emulsifier combinations not providing the desired textures, hydrophilic silicone elastomer blends can be useful. These modified chemistries can be readily dispersed in water systems, o/w emulsions or s/w emulsions. Their compatibility with polar materials such as glycerin and organic solvents also enables the formulation of a broader range of gels and dispersions. These hydrophilic silicone elastomer combinations are typically found in emulsions that require a wet finish and lighter textures.
Besides their use in emulsions, hydrophilic silicone elastomer blends can create clear, water-based systems for products such as serums or light lotions. They also are compatible in cold process systems. Many such elastomers contain a PEG/PPG component to assist with dispersion, although in certain cases, an additional water-dispersible emulsifier may help to improve stability and maintain product integrity. Instability in clear systems is quickly visible with the observation of changes in the clarity and variations in viscosity.
Elastomer Emulsifier Formulation
Although silicone elastomer chemistry has greatly simplified formulations, additional emulsifiers may be required to ensure stability and cohesiveness. Silicone emulsifiers would typically be added to w/s or silicone/o/w emulsions to ensure proper emulsion development. These emulsifiers are usually based on silicone polyether chemistry and have structures with PEG/PPG dimethicone formations. Two basic structures are polyether segments attached directly to the backbone of the silicone or polyether segments, which alternate within the silicone backbone itself in an A-B arrangement. Many variations of these can also be developed. Alkyl chains can be attached to make the emulsifiers more versatile, and modifying the molecular weight will dictate different performance capabilities. Depending on the modification, they can be tailored to affect the emulsification of other oils and organic materials.
Silicone-based emulsifiers are essential to elastomer systems, even though many are pre-emulsified. They are generally liquid at room temperature and relatively easy to use. Silicone emulsifiers typically are added while emulsifying or even after the elastomer has been incorporated and is swelling in the system.8 They are also often mixed into the oil or silicone phase and, due to their affinity for organic oils and in some cases waxes, can help emulsification within the system.
Silicone emulsifiers maintain the product's light feel while ensuring the silicone droplet is developed and uniform within the system. Their advantages are evident when compared with w/o emulsifiers used in formulations, which impart a heavier feel. The natural flexibility of the Si-O bond in the emulsifiers enables easy emulsification at any stage of the emulsion; this is the main difference when compared with the carbon- carbon bond of traditional emulsifiers that are used in w/o emulsions.
Stability Considerations
As with other emulsions, a good way to monitor the stability of silicone elastomers is to observe their particle sizes at different stages. Though silicone elastomers already contain components such as variations of polysilicones, which stabilize them as raw materials, formulators must ensure the product’s viability with additional emulsifiers. Separation or a grainy texture may be observed if the system is not balanced between the oil phase, elastomers and water phase.9 Traditional stability methods may also be used to look for coalescence or separation at higher and lower temperatures.
If instability arises, formulators should consider the water, oil and silicone phase ratios. The thickness of phases can also be examined; especially in w/s emulsions, where the viscosity would make the water difficult to fully emulsify. Additional emulsifiers may be needed if instability is noticeable and it is affecting the performance and aesthetics of the final product. Mixing and processing can also be considered when using high levels of elastomer systems. Although simple mixing is recommended, homogenization may be necessary to fully disperse powder silicone elastomers or higher levels of silicone gel elastomers.
Conclusions
In conjunction with the low irritation profile inherent to most silicones, elastomers can provide a safe and noninvasive module for active delivery to the skin. Their multifunctional abilities provide aesthetics such as smooth or wet finishes and provide structure to the product, making them a versatile tool for formulators. Due to their superior absorption characteristics, they also can entrap certain actives and fragrances, allowing them to serve as delivery systems.10
As noted, the use of silicone elastomer systems combined with innovative silicone emulsifiers has led to breakthrough products and textures in the makeup and skin care category. These products include but are not limited to BB creams, anti-aging wrinkle reducers, high-definition primers, liquid foundations, mousse foundations, gelled eye shadows and many more. In addition to improved aesthetics, they offer formulators a wide range of options such as quick or slow drying, matte or glossy finish and long-lasting hydration.11 Simple experiments using silicone elastomers with differentiated starting points, volatility and cross-linking suggest they provide many options. Novel formulas will continue to develop as this field grows, along with further advances in silicone emulsifiers.
References
1. F Kipping and LL Lloyd, Organic derivatives of silicon. Triphenylsilicol and alkyloxysilicon chlorides, J Chem Soc Trans 79 449–459 (1901)
2. M Ema, A Harazono, E Miyawaki and Y Ogawa, Dow Corning presents new silicones portfolio at In-Cosmetics, Chemical Business 23(4) 16 (Apr 2009)
3. M Starch, New developments in silicone elastomers for skin care, Dow Corning brochure article, 27-1060B-01 (2002)
4. M Toub, Factors affecting silicone volatile levels in fabricated silicone elastomers, Rubber World 226(3) 36 (Jun 2002)
5. A Colas and J Curtis, Biomaterials Science, 2nd edn, An introduction to materials in medicine, Elsevier Academic Press (2004)
6. G Dahms and A Zombeck, New formulation possibilities offered by silicone copolyols, Cosm & Toil, 110(3) 91-96 (1995)
7. L Tonge, M DiPino and C Gross, History and usage of silicone elastomers, Rubber and Plastics News 40(8) 12 (Nov 2010)
8. P Thau, Nonaqueous emulsions: History and current specialized applications, Cosm & Toil 128(5) 360 (May 2013)
9. I Van Reeth, XR Bao, Y Kaneta, C Delvall and B Sillard-Durand, Silicone emulsifiers and formulation techniques for stable, aesthetic products, Cosm & Toil 126(10) 720 (Oct 2011)
10. J Newton, S Postiaux, C Stoller, V Verhelst, S Lin and M Starch, Silicone elastomer delivery systems, Cosm & Toil 119(12) 24 (Dec 2004)
11. A Zombeck and G Dahms, Novel formulations based on nonaqueous emulsion of polyols in silicones, IFSCC Congress paper (Oct 1996)