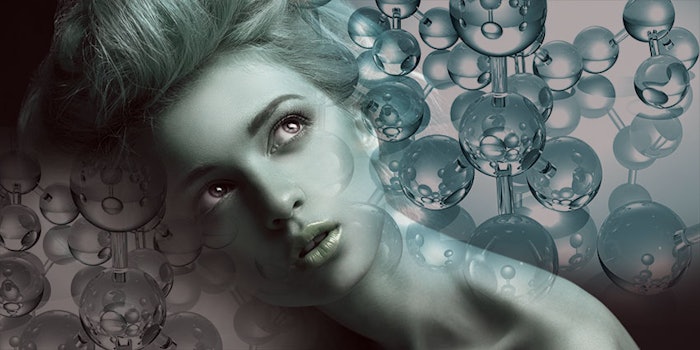
In nature, cellulose is found as β-1,4-linked glucopyranose units. The polymer chains are linked via hydrogen bonds forming fibril bundles of both highly ordered crystalline regions and disordered amorphous regions in the plant cell wall.1 Cellulose fibrils are responsible for the high tensile strengths in the cell wall of plant fibers. These fibrils or fibril bundles are obtained from wood and other lignocellulosic fiber materials.2
Log in to view the full article
In nature, cellulose is found as β-1,4-linked glucopyranose units. The polymer chains are linked via hydrogen bonds forming fibril bundles of both highly ordered crystalline regions and disordered amorphous regions in the plant cell wall.1 Cellulose fibrils are responsible for the high tensile strengths in the cell wall of plant fibers. These fibrils or fibril bundles are obtained from wood and other lignocellulosic fiber materials.2
The fibril bundles themselves are linked to one other, forming fibers. When these cellulose fibers are treated with high shear forces, they are torn apart in a longitudinal direction to result in thinner and higher aspect ratio microfibrils, i.e., higher surface area materials, referred to as microfibrillated cellulose (MFC). In order to obtain MFCs from wood, for example, high shear forces are used to disintegrate the cellulose fibers into finer structures.
The resulting MFC is capable of binding high volumes of water and forming three-dimensional (3-D) networks. This was the basis for the development of a suspension that exhibits interesting properties in cosmetic formulasa. If dried, the 3-D network structure of MFC and hence the suspension collapses, losing its water-binding properties. However, in water-bound systems, polar solvents and mixtures thereof, this 3-D network offers interesting properties.3 The present article explores potential benefits of this sustainable material for its rheology and thickening performance, matte effects, reduced combing forces and sensory appeal.
Rheology Comparison
To compare the rheological properties of the natural cellulose material with other polymers, each was dispersed in 5% glycerin (99.5%), added to a water phase, then pre-heated to 80°C. This mixture was homogenized for 1 min at 13,000 rpm using a homogenizer, then mixed at 300 rpm using a stirrer. The viscosity of the aqueous gels was measured at 10 spins per minute using a rheometer after 30 sec. Table 1 shows the resulting values.
The viscosity of the cellulose material between 0.1% and 0.4% could not be measured, likely due to the limits of this measuring method. In different formulations, however, MFC provided a non-dripping effect at low concentrations despite the fact its viscosity could not be measured using the described method. These evaluations are illustrated in further detail on page 55, in the “Viscosity Recovery in Sprays” discussion.
Skin creams produced with the cellulose material scored higher in overall matte effects than the known benchmark.
Matte Effects in Color Cosmetics
The matte effects of MFC were also of interest due its irregularly shaped, micro-sized and flexible aggregate components, which were expected to help conceal wrinkles in the skin. To determine these effects, test face creams were produced in accordance with Formula 1 and used by nine test subjects. A photograph of each subject’s face was taken before application, 600 μL of the test or control cream was applied to their face, and after a 10-min resting phase, another photo was taken.
Next, six trained raters were blindly and simultaneously presented with photos of the treated and untreated halves of the faces, for assessment. The photos were shown to the raters on a calibrated screen. The absorption times also were not shared with the raters.
After examination, the raters graded the test subjects according to criteria of: matte effect, even skin color, skin radiance and attractiveness as follows:4
1= less matte effect or 2 = more matte effect;
1 = less even skin tone or 2 = more even skin tone;
1 = less skin radiance or 2 = more skin radiance; and
1 = less attractive or 2 = more attractive.
According to the reviewers, the skin creams produced with cellulose scored higher in overall performance in all comparisons than the formula incorporating the benchmark of sodium potassium aluminum silicate (and) CI 77891 titanium dioxide (and) silica (see Figure 1). For the matte effect, even skin color and attractiveness categories, a significant difference was noted using the cellulose (see Figure 2).
These findings were surprising since the benchmark product is a well-known soft focus pigment and the natural cellulose fiber is not a spherical-shaped, coated pigment. These results suggest the 3D structure of the cellulose seemed to have an effect on skin.
Combing Forces in Hair
In general, hair combing, particularly in wet hair, can be significantly improved by using conditioners. As such, MFC was assessed for wet combing properties to potentially provide product developers with a sustainable, silicone-free alternative. A basic formula with different additives in varying quantities was therefore prepared for the related experiments (see Formula 2).
After washing and rinsing hair under defined conditions, testing was carried out by measuring combing forces in pre-treated hair. Ideally, the conditioning substance of interest added to formula will produce a film on hair to reduce the force required to comb through it. To test the prototype formulas, both blonde and gray hair were used.
While the results for MFC on blonde hair were comparable to the benchmark PCA glyceryl oleate, interestingly, on gray hair, MFC significantly reduced combing forces. This suggests MFC could serve as an effective silicone replacement for hair conditioning (see Figure 3 and Figure 4).
PCA glyceryl oleate is a well-known natural conditioner and can protect hair due to its structure. Interestingly, MFC appears to have similar effects, likely due to its relatively small size, which could fill the gaps in damaged and gray hair, providing better wet-combing forces.
Microfibrillated cellulose rapidly recovered the viscosity of a sunscreen formula greatly sheared by spraying.
Viscosity Recovery in Sprays
Initially, a method was developed to test the potential of MFC to increase the sun protection factor of an SPF 25 sunscreen formulation (see Formula 3), in comparison with known SPF booster trimethoxybenzylidene pentanedione. Per ISO 24444 (November 2010), this booster was added to the test sunscreen. Unfortunately, during in vivo tests, neither the known booster nor MFC provided a significant boost to SPF. Instead, two other effects of MFC were identified.
First, the samples made with 1% MFC displayed rapid viscosity recovery when the sunscreen formulation was sprayed, after shearing greatly reduced the test formula viscosity. This is shown in Figure 5. Second, the sensory properties of products normally perceived as oily or too rich were considerably changed using microfibrillated cellulose, and they became more velvety (data not shown).
Conclusions
In summary, a novel and sustainable material based on microfibrillated cellulose is shown here to improve formula properties such as rheological behavior, matte effects and hair combability. It therefore serves as a valuable, sustainably produced raw material option ideally suited to the enhancement of different product categories.
References
- RM Brown and IM Saxena, Cellulose biosynthesis: A model for understanding the assembly of biopolymers, Plant Physiol 38(1/2) 57–67 (2000)
- D Klemm, B Heublein, H-P Fink and A Bohn, Cellulose: Faszinierendes biopolymer und nachhaltiger rohstoff (Cellulose: Fascinating biopolymer and sustainable raw material, Angew Chem 117 3422–3458 (2005)
- A Karppinen, T Saarinen, J Salmela, A Laukkanen and M Nuopponen, Flocculated flow of microfibrillated cellulose water suspensions, Cellulose 19(6) 1807-1819 51 (2012)
- N Lunau, S Bielfeldt, M Seise and K-P Wilhelm, New method to assess soft focus parameters on living skin: How does it compare to visual lay person rating of skin radiance? Interne Methodenbeschreibung (internal description of methods), proDERM Institute for Applied Dermatological Research (2015)