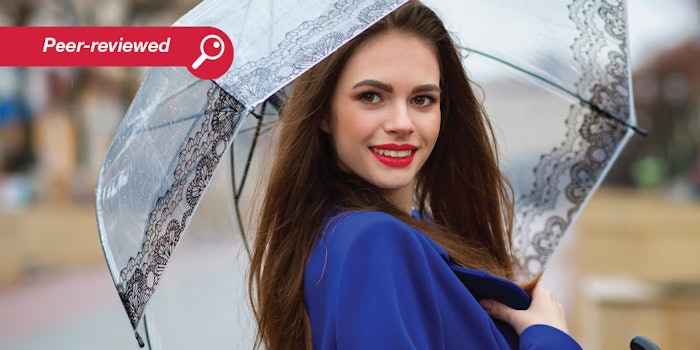
*First presented as a poster at the October 2019 IFSCC Conference in Milan. To read this article in its entirety, click through to your February 2020 digital magazine.
Water resistance is a desired property across a wide range of product categories; from leave-on hair products and decorative cosmetics, to sunscreens and skin care. This virtue can be achieved using one or more formulation approaches: a high concentration of non-polar emollients, specific combinations of waxes and resins, latex-based water-dispersible polymers, specific combinations of emulsifiers, and oil- and water-soluble film-forming polymers.
Currently, there is no globally accepted in vitro water resistance test method in any cosmetic category although according to Cosmetic Europe,1 an in vivo water resistance test is under development. Table 1 shows a variety of water resistance testing standards that exist across the world. The unifying factor for all these tests is a maximum water resistance time of 80 min.
The International Organization for Standardization (ISO) has set up a technical committee to develop the ISO/TC 217/WG 7 test methods for sun protection products, including an in vitro water resistance method.2 While this work is still in progress, the list of parameters proposed to be controlled during the test is available (see Table 2).
Polymers of various chemical classes and with a variety of structures have been used to impart water resistance to cosmetic products, for example: acrylates, silicones, latex-based, and graft and block copolymers. Most of these are multifunctional, acting as both film formers and rheological additives, and as such, require evaluation to determine their multiple effects on a product.
As noted, the present work explores the impact of two ingredients used to impart water resistance in formulas: the film-forming polymer and the type of emulsifier system. Both are known to change the rheological profiles of semisolid systems. This study first evaluated the impact of these variables on the rheological and texture profiles of o/w emulsions. Next, the researchers developed a water resistance test method to assess the efficacy of these variables in the test emulsions.
It became apparent during testing that all emulsions with the ionic emulsifier performed worse than their counterparts.
Materials and Methods
Materials: A range of seven film-forming polymers belonging to four chemical groups were used for the following tests, including: acrylates copolymer, acrylates/C12-22 alkylmethacrylate copolymer, trimethylsiloxysilicate, phenyl trimethicone, stearyl dimethicone, vinyl pyrrolidone/eicosene copolymer and polyurethane-62 (and) trideceth-6. These polymers are often used in hair care applications, although their effects on skin was explored here. The acronyms used in further text, alongside their chemical category, are presented in Table 3.
The samples in each group consisted of one base formulation (see Formula 1) without added polymer (control) and seven test formulations, each containing one of the polymers tested. The concentration of each polymer in the emulsion was 1% w/w, which was proposed in the literature as sufficient to exert water resistance. The second group of samples mirrored the first, except each contained an additional emulsifier: sodium cetearyl sulfate. All samples from the second group were labelled with a “+” sign; e.g., “AC+.”
Preparation of emulsions: A standard hot emulsification process at 80°C was used for the preparation of all test emulsions. If additional emulsifier was used, it was added to the oil phase at the beginning of the process. The polymers were dispersed in the water phase before emulsification.
Rheological tests: Rheological measurements were carried out using a rheometera with a 35-mm serrated parallel plate and the gap of 1.0 mm. Dynamic (oscillatory) and continuous flow tests were used in conjunction, to produce complete rheological profiles of the test samples.3 The oscillatory stress sweep was conducted by increasing the stress from 1 Pa to 200 Pa at the frequency of 1 Hz. The maximum oscillatory stress of 200 Pa was used in most cases, but it was increased if required by a high sample rigidity. A reduction in the complex modulus of 10% was used as the measure of yield stress; i.e., the point at which the sample yields and starts flowing.4
Two types of continuous flow tests were used: shear rate sweep and three-step thixotropy test. In the shear rate sweep, the samples were sheared from 250 s-1 to 10 s-1 for 300 sec. The use of reverse order of shear rates (from high to low) has been shown to produce less “noisy” and more repeatable data.5 The three-step thixotropy test consisted of three phases, carried out at the shear rate of 10 s−1, 250 s−1 and 10 s−1, respectively, each step taking 60 sec.5 The results were expressed as % recovery; i.e., the difference in the original viscosity measured at the first step, and the one measured at the third step.
Texture analysis: Texture analysis was performed with a texture analyzerb using a standard spreadability method.
Continue reading in the February 2020 digital magazine...