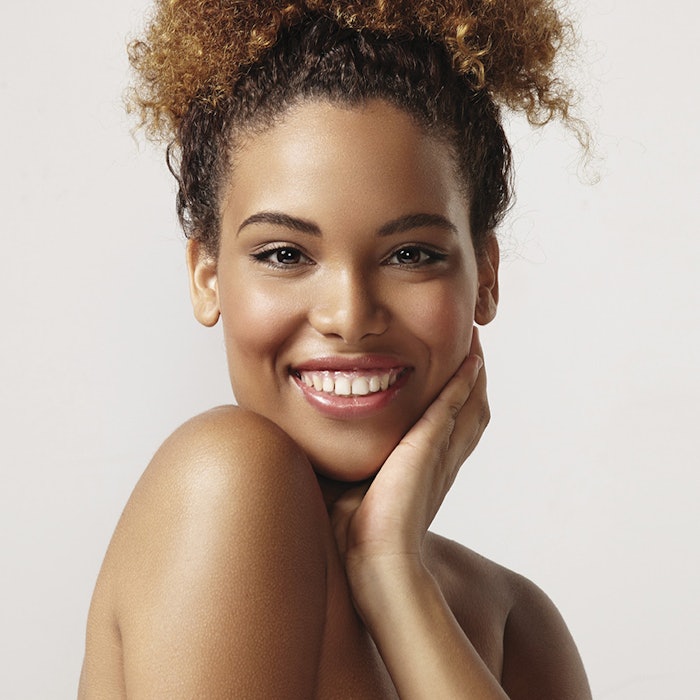
The drive for personalized consumer products is no longer a passing fad. Personalization stems from deep motivations. The emotional wish to purchase products created “especially for me” comes across with an understanding of diversity between individuals and the prospects for more effective solutions to meet each individual’s special needs. However, efforts to introduce personalized skin care—i.e., for unique skin with distinctive characteristics—on an industrial scale means products formulated for generalized needs, which could not be as effective.
Furthermore, human skin has historically been characterized by type using a conventional scale to rank it from very dry, dry, normal-to-combination and oily. Yet accurate skin characterization includes additional factors such as pigmentation, pH, roughness, age, flexibility, etc. Indeed, the fact that so many parameters characterize skin could partly explain why the daily application of off-the-shelf cosmetics is sometimes met with disappointment and poor results.
This led to the analysis of biomarkers to create personalized skin care. Such a method was patented years ago and involved skin sampling, quantitatively measuring biomarkers, analyzing biomarker profiles and preparing dermocosmetics in accordance with an individual’s specific skin needs.1
Taking this a step further, two research projects within Europa’s Seventh Framework Programme for Research and Technological Development (FP7) have aimed to execute the industrial manufacturing of such personalized skin care. The first project2, 3 sought to improve skin syndromes by developing customized topical treatments. The second project4 leveraged the achievements of the first in addition to designing the required manufacturing facilities.
The main result of these two projects is described here as an integrative personalized skin care system (IPS). This multipart process, from skin analysis to product manufacturing, is presented as a case study toward the full-scale production of personalized skin care. The basic components are reported, as are strategies of the system. Furthermore, its proof of concept, which was previously demonstrated, is illustrated here by developing personalized facial care products for a pilot group of 30 subjects.
IPS Process Overview
Personal preferences: The IPS process begins with a questionnaire to collect the customer’s personal information—e.g., age, gender, known skin sensitivities, and sun and pollution exposure levels (based on work and lifestyle), along with preferences regarding product fragrance, texture and packaging.
Skin characteristics: Next, the customer’s skin is measured using non-invasive procedures to evaluate the status of the most relevant skin characteristics.
Skin profile: The data obtained from the questionnaire and skin measurements is then processed by an algorithm that generates a personalized skin profile for each customer.
Formula proposal and production: Based on the skin profile, the algorithm proposes a customized skin care formula for the consumer’s order. In some cases, the algorithm may identify health issues or allergic risk, and decline the initial order or generate an alternative. The formula is then finalized, including calculated pump timings for each ingredient to control the dosing. Following the consumer’s order and payment approval, final production is executed in a two-step process, described below.
Product labeling: Simultaneously, the proposed formula is transferred to a machine-readable recipe, from which a proper label is output according to the requirements of the European Commission (EC) Regulation EC 1223/2009.5 The generation of this label involves resolving the formula to INCI names.
Product distribution: After production, customers receive products either on-site or by mail. Customer feedback on the product and IPS experience is also collected for continuous system improvements.
Core Components
The described IPS therefore includes four distinct components:
- A mini lab for non-invasive skin measurements;
- The multifactorial computer algorithm including learning functionality to process both personal preferences and skin parameters, and ultimately generate the personalized formula proposal;
- A two-step “mother” and “mini” factory manufacturing system,6 discussed below; and
- A computerized production system for cross-module communication and data integration.
Two additional components are logistics and regulations.
Mini Lab for Skin Analysis
For the present IPS process, data is first collected in vivo on various physical and biochemical features of the skin, such as hydration, sebum secretion level, color, elasticity, inflammatory sensitivity, oxidation, metabolism, etc., to evaluate an individual’s skin health status. This data is collected non-invasively from the body site where the personalized product will be applied; i.e., on the face for facial care, or hands for hand moisturizers. To accomplish this, a portable mini lab was designed with probes that attach to skin and quickly analyze various skin indices: hydration (by corneometer),7 pH, sebum,8 elasticity, roughness and pigmentation.
Skin structure elements also are analyzed in vivo using spectral-auto-fluorescence measurements for: collagen cross-links, elastin cross-links, advanced glycation end-products (AGEs) and tryptophan moieties.9 This data is collected quickly in vivo in a battery of measurements, taking 5–12 min total for all tests combined. Note that tape-strips for biochemical measurements were taken and evaluated as part of the mini lab development process, for comparison with non-invasive physical measurements.
Additional non-invasive skin biomarker tests are included; although their inclusion in the mini lab design is not yet feasible due to logistics. In the future, these will be added to the mini lab design, once their execution is less time-consuming and more cost-effective.
Specific biomarkers of interest include cytokine levels, e.g., interleukins and other chemokines; oxidation-reduction metabolism; and volatile organic compound (VOCs). Previous studies have shown that significant differences in the expression of these biomarkers are correlated with skin and health conditions such as aging,9 psoriasis,10 atopic dermatitis,10 chronic renal failure,11 diabetes mellitus12 and rosacea.13 As such, variations in these markers warrant further analysis.
Multifactorial Learning Algorithm
The next major component of the IPS concept is the computerized algorithm equipped for self-learning to process the collected data. This system performs multifactorial data mining to contribute to the sophistication of the IPS as it optimizes the selection of the personalized cosmetic formula. Since client satisfaction is a major target of the proposed IPS, the multifactorial analysis integrates both subjective and objective information.
The algorithm-driven selection of personalized products, whose efficacy was previously shown in FP7,14 was based on the following (see Figure 1):
- An individual’s skin profile based on objective skin measurements. As noted, rules for creating the profile are determined using both data mining techniques and mathematical models.
- The customer’s subjective preferences for product texture or form—i.e., cream, lotion, gel; type of packaging—i.e., tube, jar, bottle; fragrance; and packaging artwork design.
- The customer’s sun exposure level based on geographic location, place of work and lifestyle.
- Relevant historical background relating to personal and family health, such as known allergies and sensitivities.
- Existing databases from outside sources applicable for suggesting personalized treatments, such as:
- Personal subjective feedback from the consumer of past product use;
- Personal objective feedback on treatment efficacy based on skin measurements or physician exams;
- Scientific literature of old and new skin biomarkers;
- Scientific literature of new and existing skin preparations and cosmetic ingredients; and
- Personal adverse events, if they have occurred.
- Self-learning by the algorithm, for further optimization of the customized formulation and product design (see broken red line in Figure 1).
Products developed 'especially for me' come with the prospects for more effective solutions to meet specific needs.
Mother and Mini Factories
Commercial cosmetic products are typically manufactured from A to Z in big chemical reactors. This batch-wise manufacturing concept is optimized for the dynamic production of large volumes of product in a central, “mother,” factory. Producing a cosmetic product for one individual based on this process would be inflexible, costly and unrealistic. The described IPS system instead leverages the capacity of the mother factory to prepare large-scale base formulas, which are then customized in a mini factory.6 This enables both small scale and flexible manufacturing while obeying cosmetic GMP standards. To achieve these goals, two major principles must be applied:
1. A two-step manufacturing process, including: a) the pre-preparation of a limited number of large-batch cosmetic concentrated bases in a centralized mother factory; and b) the final customized production in a mini factory located near the point of sale. The mini factory, described below, provides sufficient flexibility by the easy extension and exchange of process components, to accommodate individual customer requests.
2. Concentrated bases, which are prepared at the mother factory. The water content of the base formulas is 10–20% instead of 50–70%, which is more typical of final cosmetic preparations. For the bases, formulators calculate the stability, compatibility and microbial challenge in advance for both maximum and minimum concentrations of diluting water, as well as with maximum concentrations of the optional added actives to bases. The bases also contain the required preservative levels before dilution. In addition, their stability is analyzed in advance with minimum and maximum concentrations, which are calculated by the algorithm.
Once the base formulas reach the mini factory, they are diluted in water, and actives, fragrance and preservatives are added at appropriate levels for the new formula volume. To control microbial contamination—as described in detail below—the mini factory is designed as a GMP independent processing system with cleaning-in-place procedures and periodic assessments to ensure sanitary conditions.
Mini Factory in Action
The mini factory is essentially an automated mixer including an additives-dosing valve system and washing unit.6 Its role is to first add water to the concentrated base in order to dilute it to the desired level. Then, selected additives are incorporated into the product and simple mixing is used to quickly prepare the final cosmetic—eliminating the need for high-temperature homogenization. The mini design incorporates the use of 21 small pumps for additives and six larger pumps for three bases and water, soap and alcohol—used for cleaning and disinfection (see Figure 2). The active manufacturing process from concentrated base to final personalized product takes 10–20 min, depending on the dose, number of ingredients and desired product viscosity.
Integrated Computerized Production
Last, the IPS utilizes different interfaces to integrate data from the consumer, mini lab, algorithm, production unit, logistics and inventory into a single, uniform platform that speaks the same language in terms of information and communication technology (ICT). This communication is executed via a computerized production system, whereby physical components interact with software in a cloud.
The following key requirements were incorporated into this system: a high degree of automation; flexibility in the manufacturing process; remote management and maintenance; and process traceability and documentation. This architecture was previously described.15
Regulatory Considerations
In the European community, topical skin care is monitored in accordance with Regulation EC 1223/20095—and personalized products are no exception. While the processes for manufacturing industrial-scale concentrated bases at the mother factory align with the cosmetic regulation, small batch production at the mini factory has specific requirements. These are listed in different articles of the EC Regulation and include considerations such as: safety (Article 3), responsible person (Articles 4 and 5), good manufacturing practice, i.e., ISO 22716 (Article 8), safety assessment (Article 10), production information file (Article 11), notification (Article 13) and labeling (Article 19). A detailed report describing IPS solutions to these articles was prepared by Zanotti and Robino16 (unpublished data), which has paved the way for IPS mini factories to become fully compliant.
Selected additives are incorporated into the product and simple mixing is used to quickly prepare the final cosmetic.
As an example, Article 13 relates to notification and it outlines the information required regarding a product’s composition. However, each product manufactured as an IPS is unique. As such, this information is provided as a concentration range, which is allowed under the official EC guidance. Consequently, each IPS product made in a mini factory has a common base and pool of active ingredients whose levels vary, but fall within the pre-defined range. This allows the IPS to benefit from both personalization and controlled, regulatory-approved production. The proposed framework thus enables traceability, reproducibility and quality standardization, all while complying with the EC cosmetics regulation.
Proof of Concept
To test the described IPS system, in terms of module operation, personalized treatment, customer experience, cost and environmental impact, a small group of 30 subjects was recruited as part of the original FP7 project 2.2, 3 Figure 3 illustrates the entire process, comprising: 1) logistic operations and 2) analysis of the demo outcome and user satisfaction.
Part 1: Logistics
As stated, 30 volunteers (ages 60–75) were recruited and enrolled with his or her informed consent. The volunteers represented three different states of skin health: healthy, type II diabetes and rosacea (see Table 1). All volunteers completed two questionnaires at the beginning of the process. The first related to health, e.g., skin type, allergies, health condition, etc.; the second was a preference questionnaire regarding texture, scent, etc. (see Volunteer Questionnaire).
Physical measurements of the volunteers’ facial skin were then taken to measure superficial biochemical levels (see Table 2). As stated previously, due to logistic constrictions, the biochemical results were analyzed but not in situ during the demo. The final customized cosmetic formulas—in this case, facial care—for volunteers were then proposed based on the individual skin profiles, as calculated by the algorithm.
Each formula comprises a concentrated base, active ingredients, fragrance and preservative. For the present proof-of-concept study, two different bases were used for facial products: a serum and cream-gel. Both were w/o emulsions containing oil and water phases, emulsifiers, preservatives and calming agents. These were produced in the mother factory per GMP ISO 22716 then transported to the mini factory to be used for the demo.
The proposed formulas were then sent to the mini factory mixing unit for preparation by dosing the selected base to the desired volume, mixing it with water and the specified additives, and generating the label according to the EU regulation. This demo aimed to test the ability of the mini factory to dose and mix the base and ingredients as directed by the computerized production system; i.e., without human intervention. All pumps were successfully controlled by the software, and the final products were prepared by fully automated dosing and mixing according to the generated prescription. The finished products also were handed to the volunteers within a few minutes after completing their skin measurements. Thus, the customized production proof of concept was well-demonstrated.
Technology Readiness
While still in the early stages of development, this four-module IPS system was submitted17, 18 to European authorities who rated it on a scale of 1–9 regarding readiness for commercialization. Here, 1 refers to the initial research mode and 9 is the final testing stage. The IPS mini lab was rated an 8, i.e., nearly ready, whereas the algorithm and computerized production systems are at a stage of 7—mature yet requiring further demonstration of actual system prototypes in an operational environment.
The mother and mini factories are at a 6, meaning they are still in demonstration levels. Thus, while it will take some time before all four modules are up and running for industry use, the approach appears to be feasible.
Part 2: Demo Outcome and User Satisfaction
After proof-of-concept testing came the real test: users. Four weeks after receiving custom products, the volunteers completed questionnaires to provide feedback about the products and their experiences. In addition, volunteers returned for a second session of measurements to assess the effects of the products on their skin. The data from both skin measurements and feedback questionnaires was integrated into the algorithm formula for self-learning to define whether the treatment was effective for each of the 30 volunteers.
Subjective results: Analysis of the subjective feedback (see Table 2) indicated 100% of "customers" were satisfied with the personalized treatment and service. Furthermore, 90% expressed interest in purchasing their demo products.
Objective results: Regarding objective efficacy, skin measurements taken before and after use of the personalized products indicated statistically significant improvements in skin’s natural moisturizing factor and elasticity, as demonstrated by corneometry and cutometry, respectively. Table 3 summarizes these results.
The capability to successively improve products based on feedback from the self-learning algorithm holds
interesting potential.
Cost Considerations and Other Benefits
It is beyond the scope of this paper to delve into comparative costs between personalized and mass-produced products. However, expert analysis of the results of the proof of concept suggest costs for the IPS product in the mother factory could be lowered by as much as 57–67%, compared with those for a similar mass-produced product. This is due, in part, to the lower production volume and weight of concentrated bases, which would save storage space.
The concentrated forms would also cut inventory transportation costs by nearly 35% (data not shown), as well as the need for secondary packaging and the number of beneficiaries along the way as the product moves from manufacturer to consumer. Furthermore, by employing simple mixing processes, the mini factory would reduce energy consumption.
Although the cost for a second mini factory would, no doubt, reduce some savings, estimates place overall savings of the entire IPS approach at ~30%.19 A commercial pilot is planned to make more accurate, reality-based observations and evaluations.
Finally, the capability to successively improve products (and skin conditions) based on updated proposals from the self-learning algorithm has yet to be proven but holds interesting potential. This option is non-existent in today’s mass-marketed products.
Discussion and Conclusions
The idea of personalized skin care is not new. Historically, it was common practice for physicians to prepare small galenic formulas on demand in a pharmacy. Similar to IPS products, these formulas were characterized by small volumes and customized as "especially for you" solutions to specific concerns. However, these products did not meet the quality standards of health authorities due to the lack of GMP-approved manufacturing plants and ISO 9001 QA standards for production.
The described IPS system presents a practical means to execute personalized cosmetic preparations in accordance with the EC regulatory framework. Furthermore, the system could serve as a tool for monitoring not only skin conditions, but overall health status, since the expression of some skin biomarkers is indicative of diabetes, or chronic and renal failure.11, 12 Finally, IPS execution can reduce costs and shorten production time to market, which could translate to other personalized consumer goods, such as health food and food additives.
The market potential for personalized skin care and cosmetics is steadily increasing. Today’s European cosmetic consumers are drawn to strong innovation, product novelty and format, skin-specific treatments, anti-aging skin care and personalized formulas.20 The presented IPS system could appeal to several of these facets, or draw in new users via market positioning; e.g., custom products that are tailored to be safer, natural, etc. Various parts of the population are expected to be first-adopters of IPS concept—from millennials seeking constant novelty through their smart technologies, to older generations needing direct, in-person advice from experts.
In the future, one might envision mini labs and mini factories used in perfumeries in larger shopping complexes, dermatology clinics or flagship stores in busy airport terminals. The IPS could be further modified to enable virtual shopping, where skin tests are performed in mini labs at prime locations and mini factory activities are presented to the customer via internet video. Different business models and services in terms of investment and franchise have yet to be thoroughly analyzed.
Regarding efficacy, it is notable that comparisons between personalized and mass-produced products would be difficult at best, considering personalized products do not stand alone—i.e., they are specific to the user, skin conditions and preferences—and are presented in a different frame of service for feedback and further improvement. Thus, objective and subjective comparisons would hold little value. However, it would be interesting to compare an initial personalized product or mass product with a personalized product after iterations.
Based on preliminary analyses, these authors believe the IPS system presented poses viable and versatile opportunities for the cosmetic and other industries in the near future. Further innovative thinking, as well as trial and error, will establish the most effective strategies to fully exploit the commercial potential of the proposed IPS.
Acknowledgements: This study was supported by:
- The European Commission FP7 Programme: Theme FoF.NMP.2013-6; Develop and demonstrate a “mini factory” concept for production of personalized skin care products for elderly population, SuperFlex project, grant agreement no. 609198 (2012-2016); and
- The European Commission FP7 Programme: Theme NMP-2007-3.1-2: New added-value user-centred products and product services under SkinTreat project, grant agreement no. 213202 (2008-2012).
The authors also wish to acknowledge all colleagues and researchers of the SuperFlex and SkinTreat projects for their contributions.
Finally, they would also like to thank Ms. Yaara Laor from the AHAVA formulation team, who took part in the development of the tested skin care formulas.
References
- Israel Pat IL 157786 Patent,Personalized skin care composition and methods for production,Z Ma’or, Y Milner and FM Bregegere (2010)
- www.fp7-superflex.eu/ (accessed Jul 31, 2018)
- http://cordis.europa.eu/project/rcn/109254_en.html (accessed Jul 31, 2018)
- https://cordis.europa.eu/result/rcn/45549_en.html(accessed Jul 31, 2018)
- Regulation (EC) No. 1223/2009 of the European Parliament and of the Council on Cosmetic Products, Official J Euro Union (Nov 30, 2009)
- World Pat WO2017/013212 A1 (in German), Mischvorrichtung und verfahren zum mischen von medien, N Othman and M Daumüller (2017)
- P Clarys, R Clijsen, J Taeymans and AO Barel, Hydration measurements of the stratum corneum: Comparison between the capacitance method (digital version of the Corneometer CM 825) and the impedance method (Skicon-200EX) Skin Res Technol 18 (3) 316–323 (2012)
- R Reimar and E Kownatzki, Corneometric, sebumetric and TEWL measurements following the cleaning of atopic skin with a urea emulsion versus a detergent cleanser, Contact Derm 50(6) 354–358 (2004)
- GN Stamatas, RB Estanislao, M Suero, ZS Rivera, J Khaiat, A Li and N Kollias, Facial skin fluorescence as a marker of the skin’s response to chronic environmental insults and its dependence on age, BJD 154(1) 125–132 (2006)
- M Portugal-Cohen, L Horev et al, Non-invasive skin biomarkers quantification of psoriasis and atopic dermatitis: Cytokines, antioxidants and psoriatic skin auto-fluorescence, Biomed Pharmacother 66 293–299 (2011)
- M Portugal-Cohen, M Oron et al, Noninvasive skin measurements to monitor chronic renal failure pathogenesis, Biomed Pharmacother 65 280–285 (2011)
- M Koetsier, HL Lutgers, et al, Autofluorescence for the risk assessment of chronic complications in diabetes: a broad excitation range is sufficient, Opt Express 17(2) 509–519 (2009)
- K Yamasaki and RL Gallo, The molecular pathology of rosacea, J Dermatol Sci 55 77–81 (2009)
- DA Rahimi, L Ruther and V Popov, Human skin profiling by physical skin biomarkers: A machine learning approach to personalized skin-care (unpublished data), submitted to Skin Res Technol
- MC Oberle and P Dreiss, Design and implementation of cyber-physical production system for personalized skin-care: A microservice-style approach, IJMMM 6(4) 295–302 (2018)
- MR Zanotti and F Robino, Standardization and regulatory aspects of personalized cosmetics (unpublished data)
- http://ec.europa.eu/research/participants/data/ref/h2020/wp/2014_2015/annexes/h2020-wp1415-annex-g-trl_en.pdf (accessed on Jul 31, 2018)
- www.acq.osd.mil/chieftechnologist/publications/docs/TRA2011.pdf (accessed on Jul 31, 2018)
- Perruca M., and Truffa S. D7.3: Report on LCA and LCC analysis of validated process. Unpublished data, Submitted to the EC (2017)
- M Sharma, Need for growth in the European personal care and cosmetics, available at https://guests.blogactiv.eu/2016/05/17 (accessed Jul 31, 2018)