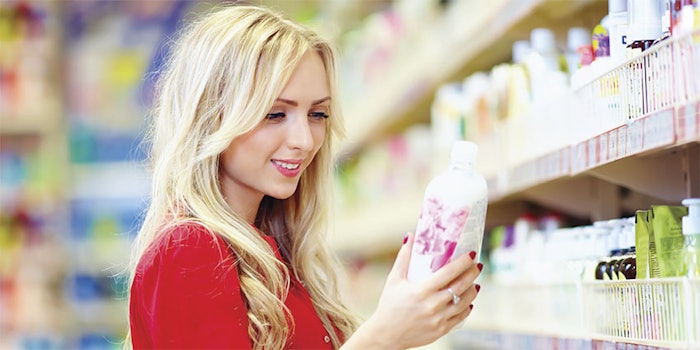
Non-sulfate anionic surfactants are often used in cleansing products for personal care, hard surfaces, laundry and industrial applications.1, 2, 5, 7, 8 In personal care alone, they range in variety; although notably, cleansers with added hair color-retention benefits and formulas positioned for the hair, scalp and body represent the segments in highest demand.2, 5, 7, 8 Due to these broad product applications, customizable performance attributes and biodegradability, the use of alpha olefin sulfonate (AOS) surfactants has increased dramatically.27
The most common AOS used in personal care is sodium C14-16 olefin sulfonate, which functions as a detergent, wetting agent and emulsifier depending on the application.18 When properly formulated, sodium C14-16 olefin sulfonate imparts viscosity, a consumer-acceptable foaming profile and quick flash foam to produce a stable lather, among other benefits.
In addition, the surfactant maintains performance at alkaline and acidic ranges, allowing flexibility for formulators.9, 3, 10 This stability is attributed to the sulfonate groups covalently bonded to a carbon; conversely, sulfate-based surfactants tend to hydrolyze below pH 4 due to inorganic ester bonds that cleave and yield a sulfate anion and an alcohol. The pH stability of C14-16 olefin sulfonate has generated additional interest over lauryl sulfates and lauryl ether sulfates for both claims and performance. It also allows the material to be provided as a preservative-free aqueous solution, using excess alkalinity for preservation.3
AOS may be produced from several olefins with differing performance characteristics. Typical grades are derived from C14-16, C16-18 and C14-18, and vary in product applications. Lower molecular weight grades are more soluble and produce better foam, while those with higher molecular weights have reduced solubility and increased detergency. Therefore, AOS of two different grades could lead to performance differences in apparently similar products with all other ingredients held constant. Foam volume, density and viscosity also vary depending on parent olefin carbon chain lengths and ratios.
Production and Manufacture
Olefins are mainly produced by polymerizing ethylene through different synthetic pathways such as the Oxo process, Shell Higher Olefin Process (SHOP) or refinery cracking; however, the Ziegler process is more common.6 The Oxo process produces a mixture of linear and branched α-olefin compositions, while Ziegler and SHOP products have lower levels of branching within their structure.6
As noted, variations in olefin quality will transfer into the final composition, and may cause differences in foam volume, density wetting properties and viscosity due to effects on surfactant micelle packing.6, 11 For example, long, single-branching and random internal olefin bonds from the Oxo pathway may result in reduced surface activity in the final sulfonate product.
The manufacturing process for AOS involves the sulfonation of the α-olefin selected to create the final surfactant. C14-16 α-olefin is the most common olefin used for synthesis in personal care applications due to its stable foam production and detergency for the final AOS.18 The sulfonation process may be carried out with different types of sulfonating agents, such as bisulfites or sulfur trioxide (SO3). The use of bisulfites introduces the bisulfite ion into the olefinic double bond in the presence of an oxidant, yielding an alkyl sulfonate. The bisulfate process, however, is not suitable for commercial production due to low yields and the complexity involved in the process.11, 14 The SO3 used for the reaction is commonly derived from the oxidation (burning) of sulfur. SO3 may also be recovered from oleum stripping or stabilized sulfur trioxide; however, stabilized SO3 requires removal of the stabilizer prior to reaction, adding an additional manufacturing step.15
The principal sulfonation method to produce AOS is a continuous process called falling film sulfonation, where a thin film of α-olefin is contacted with gaseous SO3 to create olefin sulfonic acid, as depicted in Figure 1.15, 16
Typical manufacturing steps to produce sodium C14-16 olefin sulfonate are comprised of α-olefin sulfonation, free-oil digestion, neutralization and hydrolysis.6, 11 Sulfonation reaction temperatures are controlled by feeding the C14-16 α-olefin into the reactor as a thin film while moderating contact of the gaseous SO3 vapor using an inert gas between the reactants.12, 17 Variations in the reactant feed rate, contact time, temperature of addition and mole ratio (SO3:α-olefin) affect the quality, including color, byproduct levels and free-oil levels.10, 15 Significant differences can result depending on the process equipment and controls. The process is run continuously to handle production volumes and for finer control.
Due to broad product applications, customizable performance attributes and biodegradability, the use of AOS surfactants has increased dramatically.
Conditions for the digestion step affect the type of sultones and isomerized intermediates such as 2-hydroxy sulfonate, which has very low solubility compared with alkene sulfonates.11 The hydroxy sulfonate content may increase depending on conditions. Neutralization of the olefin sulfonic acid with sodium hydroxide creates the desired sodium α-olefin sulfonate in addition to undesired five- and six-membered ring α- and δ-sultone structures, as depicted in Figure 2.11, 18 These sultones are known sensitizers and are removed through additional processing. Cosmetic grade AOS limits the γ-sultone impurity for leave-on or rinse-off products to < 10 ppm for unsubstituted alkane sultones; < 1 ppm chlorosultones and < 0.1 ppm unsaturated sultones based on the safety assessment of AOS in the Cosmetic Ingredient Review.10
Hydrolysis reduces intermediate sultone content by opening the ringed structures, converting them to the olefin sulfonate. This also modifies the ratio of alkenesulfonate to n-hydroxyalkanesulfonate via addition of a hydroxyl group, further shifting the distribution of alkenesulfonate positional isomers.6, 11 Acid hydrolysis can be used but lowers the product pH and may cause discoloration.14 Therefore, alkaline conditions are preferred for hydrolysis and final neutralization to make the AOS salt using caustic soda (NaOH) or sodium carbonate.
The resulting composition of AOS is a mixture of isomeric alkenesulfonates (65–70%) and hydroxyalkanesulfonates (20–25%), along with lesser amounts of disulfonated products (7–10%); alkene sulfonate and hydroxyalkane sulfonates.11, 10 The alkene sulfonate can rearrange during sulfonation to an internal olefin, having isomer mixtures of 1-, 2-, 3- and 4-alkene sulfonates. The reaction and process conditions discussed control the surfactant product properties such as color, clarity and performance in formulation. The AOS-critical quality parameters impacting final performance are governed by chemistry, residuals and byproducts, as shown in Table 1.
AOS Properties
Commercially, sodium C14-16 olefin sulfonates are supplied as 30–40% w/w active solutions, which are clear to slightly yellow and whose viscosity generally ranges from 200–1000 cP. The residual impurities found in AOS may include unsulfonated matter, disulfonate, NaCl, NaSO4 and γ-, δ- and chlorosultones, all of which affect the material properties. As noted, δ- and γ-sultones are known sensitizers with recommended levels not to exceed 34 ppm and 10 ppm, respectively.10 Manufacturing processes using sodium hypochlorite as a bleaching agent may create additional unsaturated and chlorosultones as byproducts and potent skin sensitizers.10, 19 Residual unsulfonated matter, disulfonate and the salts NaCl and NaSO4 may affect the Krafft point. Introductions of chain branching, unsaturation and polar segments into the AOS structure also impact Krafft temperature, through influence of the surfactant unimer solubility.
The ratio of alkenesulfonate to n-hydroxyalkanesulfonate is also impactful due to their solubility differences and can impact minimum storage conditions of approximately 20–27°C.20 The presence of the -OH group in the hydroxyalkane sulfonate structure increases solubility and lowers surface activity significantly more than the presence of unsaturation in the alkene sulfonate.
As noted, there are several benefits to formulating with sodium C14-16 olefin sulfonate, including broad pH stability and formulation versatility. C14-16 olefin sulfonate can be used as a primary surfactant in combination with betaines or sarcosinates, as well as nonionic surfactants such as polyglucoside and polysorbate and other nonionic derivatives. The nonionic surfactants aid in building sufficient packing of the micelles in the systems, consequently increasing the viscosity.18 Salt also can be used to enhance the thickening of the system; however, when using NH4Cl in place of NaCl, the product pH must be less than 7.0 to prevent ammonia formation and off odor.
There are several benefits to formulating with sodium C14-16 olefin sulfonate, including broad pH stability and formulation versatility to meet consumer needs.
Foam benefits also are noted in conjunction with betaines and ethoxylated glucosides, which have synergy with AOS and improve foam quality.18, 21 Although higher surfactant loads of C14-16 olefin sulfonate are generally necessary to achieve enhanced foaming profiles,22 the moderate cost for C14-16 olefin sulfonate offsets the need for higher concentrations. Levels also can be reduced when used in combination with ethoxylated glucosides, fatty alkanomides or fatty amidoalkyl betaines, which increase foam abundance stability and create a wetter foam for a creamier lather.21 The ability of AOS-based formulations to be customized for performance with common secondary ingredients allows product developers to readily meet design and cost targets for various segments; e.g., economy, mass, premium and luxury. Further comparisons of AOS vs. commonly used surfactants can be seen in Table 2.
Advantages and Outlook
AOS has been used in personal care mainly as a primary or secondary surfactant in rinse-off products including hand washes, facial washes, bubble baths, shampoos and most commonly, body washes. Concentrations exceeding 10% w/w in personal care formulations are considered acceptable, with AOS use in shampoos and body washes generally at ~16% w/w as supplied and above.10
As stated, the chemical stability of AOS and its ability to maintain efficacy under extremes of pH enable broad applications. The low pH stability of AOS has advantages over sulfates in specialized products for anti-acne treatments that contain large amounts of salicylic acid.23 And again, this flexibility also allows for alkaline preservation, alleviating concerns over preservative type and regulatory restrictions.
All in all, sodium C14-16 olefin sulfonate can be effectively formulated in synergy with secondary surfactants and electrolytes to meet consumer-acceptable viscosity, aesthetics and foam quality. Its moderate price can positively impact associated formulation costs due its versatility and broad application. The surfactant is also readily biodegradable, which is a highly desirable feature.27
Taken together, the robust nature of this surfactant category, cost in use and tangible benefits as well as claims have advantages for use in the future development of personal care products.
References
- cosmeticsandtoiletries.com/formulating/function/surfactant/premium-sulfate-vs-sulfate-free-information-to-make-a-choice-214206751.html (Accessed Dec 1, 2017)
- pureology.com/blog/lifestyle/everything-to-know-about-sulfate-free-shampoo.html (Accessed Dec 1, 2017)
- stepan.com/uploadedFiles/Literature_and_Downloads/Product_Bulletins/Surfactants/BIO-TERGE%C2%AE/BIOTERGEAS40.pdf (Accessed Dec 1, 2017)
- http://bit.ly/2kiDNhR (Accessed Dec 18, 2017)
- https://www.solvay.com (Accessed Dec 18, 2017)
- RJ Farn, Alpha olefin sulfonates, Chemistry and Technology of Surfactants 119-121 (2006)
- http://bit.ly/2CAPgQx (Accessed Dec 1, 2017)
- cosmeticaitalia.it/documenti/a_centrostudi/Mintel-Cosmoprof-2015.pdf (Accessed Dec 1, 2017)
- www.rhodia.com/en/markets_and_products/product_finder/product_details.tcm?productCode=90018371 (Accessed Dec 18, 2017)
- B Nair, Final report on the safety assessment of sodium alpha-olefin sulfonates, Intl J Toxicol 17(5) 39–65 (1998)
- R Bernhardt and G Dado, Sulfonation and sulfation, in Kirk Othmer Encyclopedia of Chemical Technology, John Wiley & Sons Inc., DeKalb, IL USA, online (Sep 14, 2017)
- NC Foster, Sulfonation and Sulfation Processes, The Chemithon Corp 1-36 (1997)
- surfatech.com/pdfs/Sulfate%20Article.pdf (Accessed Dec 1, 2017)
- US Pat 3409637, Sulfonating olefins with gaseous sulfur trioxide and compositions obtained therby, RD Eccles, JE Yates and TP Matson, assigned to Continental Oil Company (Nov 5, 1968)
- US Pat 531518, Process for the reaction of alpha-olefins and gaseous sulfur trioxide, RL Jacobsen and TH Ohren, assigned to Proctor & Gamble Co (Sep 29, 1970)
- US3420875, Olefin sulfonates, WA Di Salvo and JS Scharger, assigned to Colgate-Palmolive Co (Jan 7, 1969)
- L Yamane, Recent findings and experiences with alpha olefin sulfonates, J A M Oil Chemists 17 81-86 (1978)
- AJ O’lenick, Alpha olefin sulfonates, Surfactants: Strategic Personal Care Ingredients, Allured Business Media, Carol Stream, IL USA47–48 (2014)
- US Pat 4052431, Process for the production of commercial alpha olefin sulfonates, TG Baker and RJ Shute, assigned to Stepan Chemical Co (Oct 4, 1977)
- K Holmberg, B Jonsson, B Kronberg and B Lindman, Surfactant micellization, in Surfactants and Polymers in Aqueous Solution, 2nd edn, Wiley, Oak Brook, IL USA 37–65 (2002)
- US Pat 4450090, Thickened alpha-olefin containing formulations, J Kinney, assigned to Clairol Incorporated (May 22, 1984)
- cosmeticsandtoiletries.com/formulating/function/surfactant/premium-sulfate-vs-sulfate-free-information-to-make-a-choice-214206751.html (Accessed Dec 1, 2017)
- personalcaremagazine.com/story/8753/encapsulated-salicylic-acid-for-acne-treatment (Accessed Dec 1, 2017)
- ME Tuvell, GO Kuehnhanss, GD Heidebrecht, et al, AOS—An anionic surfactant system: Its manufacture, composition, properties and potential application, J Am Oil Chem Soc 55(1) 70–80 (Jan 1978) doi: https://doi.org/10.1007/BF02673393
- stepan.com/uploadedFiles/Literature_and_Downloads/General_Lit/Personal_Care/StepanSulfateFreeSurfactantSolutionsGuide.pdf (Accessed Dec 1, 2017)
- US Pat 9622952, Internal olefin sulfonate composition, Y Doi, H Hori, Y Mitsuda and Y Yoshikawa, assigned to Kao Corp (April 18, 2017)
- I Brierley-Green and J Gee, Recent studies on the production of sodium alpha olefin sulfonates as concentrates and dry products, Chemithon Corp (2000)
- DR Karsa, Surface Active Behavior of Performance Surfactants, Taylor and Francis, Abingdon, England 14 (2000)
- www.thefreelibrary.com/Sulfate-free+personal+cleansers%3a+more+marketers+are+trying+to+develop...-a0185167259 (Accessed Dec 1, 2017)
- in-cosmetics.com/RXUK/RXUK_InCosmetics/2014-website/Documents/Innospec%20IS%20Presentation2ndApr.pdf?v=635340141445032079 (Accessed Dec 1, 2017)
- soynewuses.org/wp-content/uploads/MOS_Surfactants2009.pdf (Accessed Dec 1, 2017)