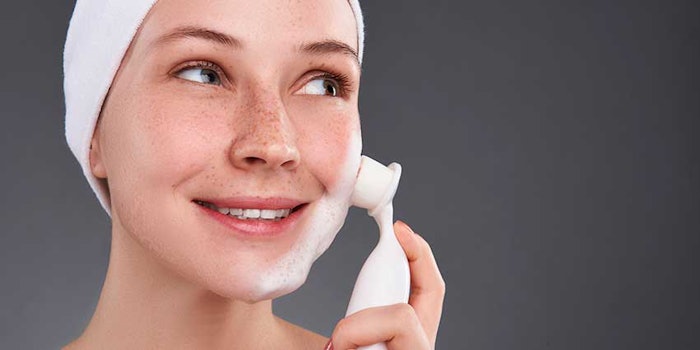
Skin cleansing today has become a demanding, fragmented market that requires sophisticated products having a variety of appearances and textures. Clear formulas with suspended particles, beads or capsules, for aesthetic or functional benefits are more and more common. Mild cleansing products for sensitive skin are also a trend, and are usually based on sulfate-free formulas.1, 2 Cleansers with added skin moisturizing and nourishing benefits, which often contain significant amounts of natural oils, are also growing areas, and as consumers expect such products to provide benefits beyond cleansing, the line between shower/bath products and skin care becomes blurred.
Beyond these trends, another focus for most product manufacturers is to lower the overall actives content in formulas—particularly in high-performance formulas, where lower surfactant levels are desired for economical and environmental reasons. The challenge for formulators is to achieve a significant reduction in the production cost while maintaining satisfactory performance for the consumer. This often involves incorporating performance additives in innovative, cost-effect ways to help compensate for the loss of certain attributes that necessarily follows from dilution.
Rheological solutions have continuously evolved to support these various needs. For conventional formulas, a number of commercial actives has been developed to impart viscosity, suspending power or both, based mainly on natural gums or synthetic polymers, which will be detailed later. However, to date, there is a clear gap between the available technological solutions and their successful application for specific textures, i.e., thickening, suspending and shear-thinning, without a negative impact on aesthetic benefits such as transparency; or performance attributes such as foam generation, cleansing and care.
The present article describes a hydrophobically-modified alkali swellable emulsion (HASE) polymer, polyacrylate-33a, which was designed to close this gap. It abilities to solve formulating challenges especially in low-surfactant cleansing formulations, i.e., 6-13%, was assessed by viscosimeter and rheometer readings, UV/VIS spectrometer, foam readings and sensory testing.
Polymer Design
The good balance between thickening, shear-thinning rheology and suspension properties provided by polyacrylate-33 in surfactant solutions was obtained through the adequate selection of proprietary associative macro-monomers. Schematically, the structure of this HASE polymer resembles the schematic shown in Figure 1. In its starting form, the material is a liquid grade, low viscosity acidic latex. Upon neutralization of the polymer in solution, hydrodynamic volume expansion of the latex particles occurs due to electrostatic repulsion between the ionized acidic groups. In addition to this, association between pendant hydrophobic groups contributes to the structure of the formula. These hydrophobic moieties are also free to associate with other species like surfactant micelles, providing additional synergies.
Materials and Methods
The performance of this polymer structure was assessed by incorporating it into simplified preparations and making several evaluations. For the tests conducted, unless otherwise specified, the concentrations of the raw materials are expressed in % w/w active. While the polymer can be added at any time during the process, for the described evaluations, it was added to deionized water under moderate stirring with a polymer amount between 1.0% and 3.3%; followed by the addition of the anionic surfactant(s) between 3.0% and 11.0%; and the slow addition of a 15% sodium hydroxide solution, i.e., the neutralization step, to reach a pH of 6.5. Amphoteric surfactant, between 1.0% and 3.0%, and nonionic surfactant, between 0% and 2.5%, were added followed by other ingredients including humectant, pearlizer, fragrance and solubilizer pre-mix, preservative, dye and sodium chloride. The formula pH was then adjusted with solutions of citric acid or sodium hydroxide. Finally, particles or beads were added for aesthetic purposes.
When the formula contained up to 0.5% cationic polymer, i.e., guar hydroxypropyltrimonium chloride or polyquaternium-7, it was added after the amphoteric surfactants. Post-addition of the polymer on a fully formulated product also could be considered, depending on the chassis, as could the addition of beads, particles or capsules after the incorporation of anionic surfactant and prior to neutralization at pH 6.5. In this manner, the formation of bubbles resulting from the final addition of particles in a viscous medium can be avoided. The viscosity of each composition was then measuredb after 24 hr in a temperaturecontrolled room, 20 ±1°C, and after a stabilization time of 1 min. Flow curves and yield stress measurements were taken by a rheometerc at 20°C using a 60-mm, 2 degree-cone/plate geometry with a 53 μm-gap. After a 2-min stabilization step, a stepped flow was applied with a ramp shear rate from 10-3 sec-1 to 1 sec-1. A continuous ramp was then applied from 1 sec-1 to 1,000 sec-1. The static yield stress was determined as the value of the applied shear stress beyond which the viscosity started to decrease.
Foam volumes, both initial and after 1 min, were measured using a high throughput methodology adapted from Ross-Miles tests. Solutions diluted 10x were prepared by mixing 10 g of each formulation with 90 g of water having controlled hardness (30°TH i.e. 300 mg CaCO3/Liter). These diluted formulas were then divided as follows: 20 mL were placed into plastic syringes set on a fixed metallic bar. Above the fixed bar, a mobile bar pushed and emptied the syringes at a controlled speed. The liquids then fall into 100-mL glass cylinders containing 10 mL of the same diluted formulas. The high-speed falling created foam, and this is photographed as a function of time. The initial foam volume and the volume after 1 min were then recorded.
Besides viscosity and foam, the transmittance of each formula was measured using a UV/VIS spectrometerd at 600 nm in a 10x10 cell. Transmittance values higher than 95% were targeted, which corresponds to a clear or even a crystal-clear formula. Typically, at 90% transmittance, a formulation is visibly turbid. Also, hand-wash sensorial assessments were carried out by an expert panel of 10 trained individuals following a standardized protocol of hand-washing.
Rheological Benchmarks
To understand the results, it is first beneficial to review benchmark rheological solutions. To obtain particle suspension or oil emulsion stability, the introduction of a rheological agent bringing sufficient yield stress is generally recommended. The yield stress point of a formula can be defined as the minimum stress value applied to initiate flow. When the stress is below the yield point, the system displays elastic or solidlike behavior. Beads dispersed in a formulation will thus remain suspended if the yield point in the medium is sufficient to overcome the effects of settling or buoyancy of those particles.
Some polysaccharides such as xanthan gums are well-known to provide high suspension power.3 However, they do not offer broad tolerance to common surfactant systems, and an undesirable “jelly” texture is obtained, which limits their use in cleansing products. Polyethylene glycol (PEG) diesters of fatty acids4 are also widely used in challenging mild surfactant systems such as sulfate-free formulas. Sulfate-free surfactant bases are known to be difficult to thicken.5 Standard salt addition promotes the formation of elongated micelles in classical ethoxylated sulfate chassis, thereby providing thickening. However, this does not work in most sulfate-free chassis. PEG-functionalized polymers offer an interesting thickening alternative6 but due to their associative properties, they do not provide yield stress and cannot be used for the sake of particle suspension or emulsion stabilization. Cross-linked acrylic emulsion copolymers (INCI: Acrylates Copolymer) constitute the most widely used benchmark for particle or capsule suspension,7 especially for the development of clear formulas, although they exhibit some disadvantages. The efficacy of polyacrylate-33 was therefore compared with acrylates copolymer, the most commonly used benchmark.
Thickening and Transparency
The results in Figure 2a show that polyacrylate-33 provided significantly greater thickening than standard, non-hydrophobically modified acrylates copolymer. This performance was evaluated in a classical though dilute surfactant chassis made from 9% active sodium laureth sulfate (SLES) and 2% cocamidopropylbetaine (CAPB) without the addition of salt, which typically is included to increase viscosity. At 2.4%, polyacrylate-33 was sufficient to obtain a shower gel viscosity of approximately 10,000 mPa.s, while 3% acrylates copolymer was necessary to obtain the same level of thickening. Consequently, for a similar level of 2.5% active of both polymers, polacrylate-33 yielded a viscosity of about 12,000 mPa.s, whereas acrylates copolymer obtained 5,500 mPa.s. Both formulations had fairly comparable transparency, with a transmittance of > 98% in both cases.
The superior thickening power of polyacrylate-33 in salt-free situations also remained true in a less conventional and more challenging sulfate-free chassis made from 8.25% disodium laureth sulfosuccinate (SLESS) and 2.75% cocamidopropyl hydroxysultaine (CAPHS). This chassis cannot be thickened with sodium chloride and requires the use of a rheological agent. At 2.75% active, polyacrylate-33 yielded a viscosity of about 11,100 mPa.s, compared with 6,300 mPa.s for the acrylates copolymer. In addition, the transparency of the formula thickened with polyacrylate-33 exceeded that of the acrylates copolymer, i.e., 95% versus 91% transparency.
In the presence of salt, when added to conventional SLES/CAPB chassis, polyacrylate-33 showed a synergistic thickening effect that was much greater than the synergy between acrylates copolymer and salt (see Figure 2b). At 1% sodium chloride, the formulation based on polyacrylate-33 was clear, i.e., 97.7% transmittance, while the formulation based on acrylates copolymer was measurably and visibly turbid, i.e., 90.3% transmittance (see Figure 2c). With the acrylates copolymer technology, even 0.5% sodium chloride added to the surfactant chassis negatively impacted the transparency of the formula, making transmittance decrease from 96.6% at 0% NaCl, to 94.1% at 0.5% NaCl. Polyacrylate-33, on the contrary, showed improved resistance to electrolytes in terms of clarity, provided the formulation pH remained above 6.3.
Yield Stress for Suspension Power
Besides viscosity and transparency, the yield stress response of formulations containing polyacrylate-33 was evaluated. The yield stress desired to achieve a specific particle suspension depends upon the particle diameter, density of the continuous medium and density of the particle. A minimum yield stress target of 1 Pa is typically desired for standard particle, capsule and bead suspensions.
As Figure 3 shows, the yield stress was dependent upon the total surfactant content in an SLES/CAPB conventional chassis; when the surfactant content was decreased, polyacrylate-33 exhibited an increasing yield stress response. This can be used to determine the level of polacrylate- 33 required to obtain a given yield stress in an SLES/CAPB chassis. For example, for a total surfactant content between 7% and 13%, a formulator would require between 2.0–2.3% to 2.4–2.6% polyacrylate-33 to obtain approximately 1 Pa (see Figure 3). For formulators developing low surfactant content systems with adequate thickening/suspending properties, this results in a low polymer level in their formula. As a final note, for formulations that need not be clear, the pH can be adjusted after neutralization between pH 3 and pH 6, where the thickening and suspending properties are maintained at an optimum level.
Synergies with Cationic Polymers
Cationic polymers can be introduced into shower gels and shampoos to provide conditioning, and being cationic in nature, their somewhat limited tolerance to large molecular weight anionic species such as rheology modifiers can cause formulation problems and performance limitations. However, HASE polymers, particularly polyacrylate-33, show synergistic thickening with cationic polymers;8 whether natural, i.e., guar hydroxypropyltrimonium chloride, or synthetic, polyquaternium-7. Furthermore, the addition of salt such as sodium chloride in systems containing polyacrylate-33 and polyquaternium-7 boosts the viscosity and transparency of the formula (see Figure 4), a feature which is generally not possible with standard acrylic-based copolymers. Beyond 0.5% w/w NaCl, the viscosity strongly increases, reaching the classical target of 10,000 mPa.s and a transmittance above 95% beyond 1% NaCl.
Texture and Foaming
A key challenge to reducing the surfactant content in a rinse-off formula is maintaining reasonable foaming properties, especially in the presence of rheological agents. Indeed, the speed at which foam is generated, or so-called flash foam, relates to the ability of surfactants to rapidly diffuse at the air/ water interface. This process can be significantly slowed in a highly viscoelastic medium due to the rheological agents that have been introduced.9 Further, upon applying a cleansing product to wet skin, consumers dilute it with the water on their skin in order to use it. To generate foam, the product must therefore present an appropriate rheological response to dilution itself, and products that remain highly elastic will foam less than those whose viscosity rapidly collapses with dilution. Thus, the authors investigated the viscosity response to dilution and foam generation of three different formulas, all based on the same surfactant chassis but thickened differently: with 2.5% polyacrylate-33, and with 2.5% or 3.3% acrylates copolymer. This higher level of acrylates copolymer was necessary to obtain a viscosity similar to that obtained with 2.5% polyacrylate- 33. The rheological and foam results are summarized in Figure 5.
Polyacrylate-33 yielded a clear formulation with a viscosity of about 11,700 mPa.s, whereas acrylates copolymer at the same level achieved 5,500 mPa.s. On the other hand, the acrylates copolymer imparted a larger yield stress, with 2.0 Pa at 2.5% and 5.1 Pa at 3.3%, compared to 1.3 Pa with polyacrylate-33 at 2.5%. Regardless, for all three formulations, the yield stress was larger than 1Pa and thus sufficient to suspend most standard beads or capsules encountered on the market.
As for the viscosity response of each formula to a 50% dilution (see Figure 5), the formula thickened with 2.5% polyacrylate-33 showed a thirtyfold collapse in the viscosity profile, while formulas thickened with 2.5% and 3.3% acrylates copolymer showed tenfold and fivefold collapses, respectively. At the same time, the foam evaluations showed that the formulation based on 2.5% polyacrylate-33 presented a significantly larger initial foam volume, which remained true after 1 min. While these viscosity experiments suggested that formulations based on acrylates copolymer tended to resist dilution, the foam experiments established that the foam generated was smaller. On the contrary, the viscosity resistance to dilution of formulas thickened with polyacrylate-33 was lower and as a result, the amount of foam immediately generated was larger.
Sensory Panel
To obtain a broader picture of the in vitro foam measurements, sensorial assessments of two formulas based on polyacrylate-33 and acrylates copolymer were carried out by a trained panel (n = 10) following a standardized hand-wash methodology. The polymer levels, i.e., 2.3% polyacrylate-33 and 3.1% acrylates copolymer, were adjusted so that the two formulations based on an 5.6/3.4/2.0% SLES/SLS/CAPB chassis had the same target viscosity of approximately 12,500– 15,000 mPa.s at 10 RPM. The sensorial spectrum including flash foam and foam viscosity, density, whiteness and richness, averaged over the 10 participants, is shown in Figure 6. While the formulation based on acrylates copolymer exhibited exceptional foam density, that based on polyacrylate-33 showed a more balanced spectrum of foam attributes, especially foam volume and flash foam.
Formulation with Polyacrylate-33 HASE Polymer
Table 1 shows example formulations with different textures and uses. The low surfactant scrub body wash in Formulation A is a chassis characterized by a low amount of polymer and surfactant that is based on SLES and CAPB yet contains exfoliating beads and SLS to boost foam properties. Formulation B, a sulfate-free exfoliating facial wash, depicts a clear formula based on a combination of mild surfactant grades, i.e., DSLESS/CAPHS, with emollient capsules. Formulation C, a pearlescent body wash formulated at an acidic pH, contains a pearlizing agent and mica pigments to add sparkle. Formulation D, a moisturizing shower cream, contains a high content of vegetable oil, the emulsion being stabilized by polyacrylate-33. Finally the clear shower gel with cushion feel in Formulation E illustrates the interest of associating polyacrylate-33 with polyquaternium-7 for the design of a transparent, thickened formula for foam richness, whiteness and density.
Utilizing polyacrylate-33, where crystal-clear formulations are desired, the final formulation pH should be adjusted to above 6.3, and the amount of amphoteric surfactants should be kept below 3.0% w/w. When cationic polymers are present in the formula, the salt content should be increased to 0.9–1.5% to achieve optimal transparency. As stated earlier, the polymer was designed to exhibit high thickening and good suspension properties in low-tomedium surfactant formulas. While suspension properties are optimal in low surfactant systems at low polymer levels, it would not be possible to suspend standard beads and particles in formulations containing more than 13% surfactant at a reasonable polymer content.
Polyacrylate-33 is a flexible and easy-to-process rheological agent. As noted previously, depending on the formula type, it can be added at any time during the formulation process; the only crucial point being that the polymer solution is neutralized at a pH of 6.5 after its incorporation, either by the addition of a sodium hydroxide solution or any ingredient that would increase the formulation pH.
Conclusions
Described here is a novel HASE polymer, polyacrylate-33, which offers rheological solutions for the development of modern cleansing formulations having premium textures and appearances. The polymer displays high thickening efficiency, shear-thinning rheology and good suspension properties in low-to-medium surfactant content systems. It has been shown to perform well in conventional sulfate-based surfactant systems but also in more challenging sulfate-free systems. Above pH 6.3, it provides high clarity with an excellent tolerance to salt. In addition, synergistic thickening occurs with the HASE polymer and salt, as well as with cationic polymers, which can be used to fine-tune the viscosity and flow behavior of cleansing formulations. This balances yield stress with thickening efficiency for an easy collapse of viscosity upon dilution during application for enhanced foam volume generation.
Acknowledgements: J. Cazette, E. Park, M. O’Rourke and the EU Home and Personal Care Laboratory have contributed to the experimental work presented in this article. In addition, the authors wish to thank T. Futterer, M.P. Labeau, F. w, F. Bussod, E. Leroy, D. Dobrowolski, I. Wong, Y. Yang, A. Lee, C. Mabille and V. Picquet for fruitful discussions throughout the project. They would especially like to thank D. Bendejacq for his assistance and guidance in writing this article.
References
- T Schoenberg, Sulfate-free cleansers, Cosm Toil 121(12) 61–66 (2006)
- R Davidson, Handbook of Water-soluble Gums and Resins, McGraw Hill, NY (1980)
- G Sworn, Handbook of Hydrocolloids, ch 6, CRC Press Inc, NY (2000) pp 103–115
- MJ Fevola, Ingredient profile: PEG-150 distearate, Cosm Toil 126(1) (Jan 2011)
- www.happi.com/articles/2011/11/versathix-an-ideal-rheology-modifier (Accessed Jun 21, 2012)
- U Kortemeier et al, Thickening agents for surfactant systems, SÖFW 136(3) 30–38 (2010)
- A Suares et al, Optimizing performance when using polymers in surfactantbased cleansing products, J Cosm Sci, 74–77 (2006)
- WO 2011/100071, patent application pending
- Les mousses: Moussage et démoussage, in Book of Formulation, EDP Sciences: Les Ulis Cedex A, France (9)74 (2000) content.