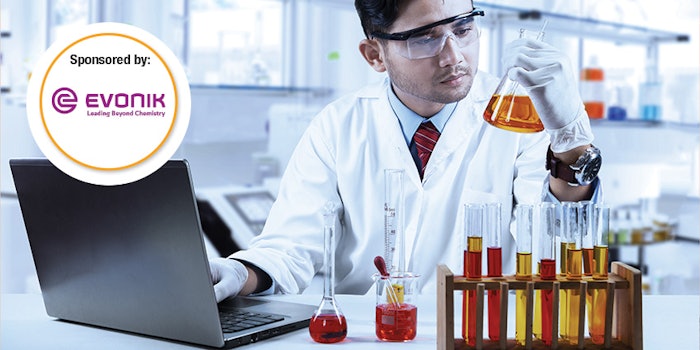
Read the full article in the April 2021 digital edition. . .
Editor's note: Beginning this month, Cosmetics & Toiletries is pleased to present an entire series focused on preservation—from benchtop strategies for formulators (described here), to case studies in production and their resolution, starting on Page 42. Join us as we follow products as they move beyond the benchtop, in order to identify potential weak points in preservation.
Where, in a formula's lifecycle, is it most vulnerable to microbial contamination? And what can formulators do to ensure a robust system that stands up to the challenge? These questions and others were posed to Steve Schnittger (SS), Ph.D., vice president of microbiology and fermentation in R&D at The Estée Lauder Companies, in the following interview.
Sidebar: At Evonik, preservation begins at the formulation development phase
This kicks off our special focus on preservation with a view from the bench—leading to a comprehensive series of challenges encountered during full production (see Page 42 for Part I in this series).
C&T: What are some of the key points during a cosmetic product’s life cycle where it is most vulnerable to microbial contamination?
SS: All cosmetic products that contain water have a potential risk of contamination if GMPs are not properly followed. So anywhere during that product's life cycle, from manufacturing to filling to use by the consumer, there's always a concern around potential contamination.
It all starts with the raw materials. If the raw materials are properly controlled during the incoming process of storage and handling, and the water system used during manufacturing is properly validated, then there is a high degree of confidence that the risk of contamination for this part of the process is minimal.
Secondly, if a company is following the proper cGMPs during both the manufacturing process and filling operation, then the risk is again reduced because hopefully they have validated their overall processes to reduce the potential of an external contaminant being introduced into the process flow.
It’s only when people aren't doing their due diligence that problems arise. More often than not, what you see in many of the FDA recalls is based on the presence of waterborne organisms. If the quality of the water that they use for manufacturing is not properly filtered or sterilized, or if standing water is left to accumulate anywhere in the process, that's where the problems begin. So if that first step in the process of influent water and sanitization is not under control, from there, major problems could occur.
C&T: What about powdered or nonaqueous products?
SS: For anhydrous products, the risk is not as great. Even in a powder product where a water-based ingredient might be in there, there's normally not enough water to support growth. You must continue to test and preserve but the potential for survival and growth is significantly reduced.
As with aqueous products, adherence to cGMP procedures is a must. You do see reports where products are tested right off the shelf but usually the numbers of organisms found are very low as compared to an aqueous based product. For anhydrous products, contamination is basically in a static state. So for the most part, again, if the raw materials meet specification and GMP procedures are followed, then the manufacturing of anhydrous and powder products would not be at a high risk for contamination.
C&T: What can product developers do to prevent contamination?
SS: Water is the main concern, and water-based ingredients—and ... many of the active ingredients that we use in our formulations, are water-based. So again, they have to be properly preserved and follow the proper controls for storage and handling. So yes, for a formulator, there is that same risk when developing a product as there is when a product is being transferred to manufacturing for production. The same rules and procedures apply.