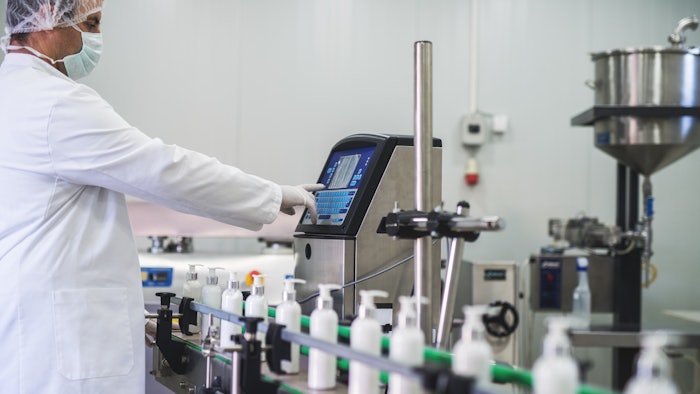
Huge resources in terms of money and time are invested to develop a cosmetic product from prototype to finish that may not even be launched to the market. Various challenges can arise that force a company to postpone or even cancel the launch. For example, during the frenzy of completing the launch, sometimes small, seemingly insignificant variables are forgotten. Or, problems are pushed to the future to address – but sooner or later, these return; this has been referred to as the time bomb or boomerang effect.1 Once these variables return, they erode the value and quality of the product.
Add to these challenges the fact that the focus of formulation has, in many ways, moved away from technical basics to trending concepts such as green and sustainable;2, 3 or skin physiology, new analysis techniques, etc. As a result, the fundamentals of formula reproducibility or long-term stability have become secondary, perhaps because basic concepts have been lost.
The present article revisits basic considerations for product development in terms of the roles of the formulator and process engineer, demonstrating the many variables where issues may arise. This can help the formulator to anticipate the challenges faced during scale-up to speed their resolution – or prevent them from the start. The article also provides tips and tricks to assist in the scale-up process.
Systematic Formulating
Everything starts from the formulator’s activities. The main aim of a formulator is to create innovative, pleasant, efficient, stable formulae within the goals and limits of a marketing project, in a fixed time and within a given cost frame. Initially, a small-scale sample of a few hundred grams helps to identify the key quantitative ratios among the selected ingredients.
The formulator’s objective is to associate the required functions and characteristics of the finished product with a series of raw materials and their mutual ratios. The assembly of ingredients provides a systemic constellation of interactive properties in a delicate equilibrium. Ingredients are added in a small beaker, one by one, and their successive introduction modifies the composition universe. Substances are forced to combine by excess mechanical action and temperature on the few hundred grams of the blend. And certainly, formulators prepare the model formulae or recipes more than once, with small differences from the final solution selected.
This experience represents the traditional production method — even if the 400-500 g is just a small universe compared to what will be the final batch size. In addition, the formulator collects information concerning the adopted order of addition of ingredients in the model, the selected temperatures of preparation, the vacuum strategy (practical or theoretical, since bench samples are rarely prepared under vacuum) and the importance of time schedules in the different stages of preparation.
Any mixing difficulty encountered or product parameter determined throughout the process is also recorded; e.g., the homogenization times and speed; heating and cooling procedures; the suggested control parameters (intermediate and final); their acceptable variability (whether numerical or sensorial); and key characteristics and organoleptic parameters. Moreover, all negative results should be taken into consideration, as they could provide elements for the interpretation of scale-up results.
Planning for Scale-up
The next step is to investigate the industrial feasibility of the developed formula. This should be the task of process development experts, who aim to make scaling up from the bench formula to industrial production a smooth process. They also forecast and plan adequate trials to obtain the required model on a larger scale.
Identifying the process: In the transfer to an approx. 1,000× larger scale, it is necessary to identify the simplest, cheapest, quickest and safest way to reproduce a given recipe with minimum possible variability in the course of several successive industrial runs. Factors such as the weighing of ingredients and their addition order while feeding the mixers, the organization of the mixing speed, the temperature cycles, homogenization and vacuum conditions, etc., require mastering a large set of technological elements.
Accounting for the chemistry: Fundamentally, there are also considerations for the chemical characteristics of ingredients, including their mutual solubility and melting behaviors, the requirements of storage conditions and handling, the mechanical and energy characteristics of mixing and filling equipment and energy and time-saving procedures, together with the assembling of adequate check methods and instruments.
Equipment, controls, materials and production variables: Process development also involves the management and organization of an array of variables ranging from the deionized water supply and its cycles; heating speed of the bulk; and dispersion, wetting and swelling behavior of powders and polymers, etc.; to batch homogeneity; identifying optimal particle size in solid dispersions and emulsions; selecting the most suitable type of mixer; and decisions over proper batch size, etc. Moreover, there are intermediate controls during batch preparation, calculations for the premix, mixer-discharging procedures, stability of characteristics and specifications, color and physical variable corrections, and worker safety elements to consider.
Time constraints: Time constraints are always the enemy to accurate product scale-up. Frequently, the careful study of all the variables described would take more time than is compatible with the characteristic short, unknown and swift speed of the cosmetic market; although a well-studied formula scale-up would represent a form of insurance for the long-term success of the formula’s reproduction.
Transfer of Knowledge from Lab to Process Development
Another critical step is to transfer the know-how from the formulation lab to the process development team. To successfully achieve this, formulators should include a brief description of the original reasons for the formula’s development, the adopted formulation strategy, the product requirements as outlined by marketing, the product characteristics, the packaging type and materials, and the most probable type of consumer.
Ingredient details: Ingredients should be described in the order of their importance in the formula and the key reasons for their combination. Foreseeable variabilities in ingredient quality and characteristics, which are sometimes the reason for selecting a given supplier, should be explained and discussed. The tolerance of their amounts by the finished formula is also important; usually, this is of the order of + 0.1% to 1.0% of the foreseen amount, depending on the type of ingredient.
The key parameters of raw materials – the known impurities (e.g., residual reagents, by-products and known contaminants) and their specifications, possibly already agreed upon with the supplier – should be presented. Specific information concerning their ideal storage conditions, stability, economic and minimum lots, containers that represent their standard supply, all microbiological aspects and the ease of in-house communication with the supplier (in case of problems) all should be communicated. As a form of insurance in the case of future raw materials shortages, the identification of possible substitutes or alternative suppliers should also be examined, including the level of risk involved for each substitution.
Bulk stability and storage: At this stage, the proper storage conditions for the final bulk product should be identified as well, considering the results of stability trials carried out on the selected prototypes and on all other back-up recipes. All microbiological pedigree of the formula should be disclosed, too, together with the delay required for the microbiological approval of the bulk (when necessary).
A standard sample of the most significant laboratory trial of the formula, communicating its age, expiration date and approval references, should be shared and discussed with the processing department. Tentative product specifications can also be provided at this time, together with tentative acceptable variability of specifications.
Production review: During production, the product profile is examined in terms of the known immediate behavior after production, after 24-hr stabilization, the behavior of the bulk during storage and any other special needs after manufacturing. Whether it is necessary to establish a regression curve for some key parameters will be determined by the process development department; this usually concerns rheological behavior and pH values. Correction actions also should be identified and established in advance whenever necessary – even if once can identify the sources of variability and keep them under strict control.
A Note on Process or Recipe Changes
When it comes to changing a process or recipe, all the elements must be carefully described; e.g., chemical, physical, sensorial, foreseen manufacturing procedures and explanations for their purpose. Frequent reasons for change could be to replace the perfume or preservative system. Trial modifications of existing manufacturing methods may also identify a valid reason for alterations. For instance, it may be observed that the addition of NaCl to a cleansing formula could be performed through the addition of a saturated aqueous solution of NaCl. This change would speed up all manufacturing times related to the complete dissolution of NaCl in the surfactant blend. One additional reason could be upgrading the batch size or adopting existing ingredients from new suppliers.
Scaling Up: Tips and Insights
Scaling up cosmetic formulations is a many-sided problem. First, as formulators know, it reflects the complexity of cosmetic formulations considering the often high number of ingredients in each formula. Second, the blending operations of ingredients are made complicated by their different physical forms and aggregation states: light and heavy powders, solid waxes, pastes, sticky butters, fluid and gluey oils, water, volatile perfumes, solvents and the whole range of physico-chemical possibilities of polarity and solubility.
Third, the amounts of individual ingredients can vary from 0.001% to more than 50% of the batch size. Moreover, the characteristics of the finished products cover a wide spectrum of possibilities; from cast products to fluid emulsions; viscous pastes to compact powders; aerosol to gels; suspensions to solutions and an equivalent variety of adequate dispensing systems.
When it comes to scaling up, it typically is recommended to increase a batch size by one order of magnitude or slightly less. In other words, when the first step is set at 5-10 kg, the second step is at 50-100 kg and the final pilot (or first industrial test) is at 300/500 kg. A different approach may be applied to makeup products, which are smaller-scale developments, or personal hygiene products, where larger quantities are needed for final trials. The choice of the batch format is also dictated by the availability of machinery in the production site, the quantity of raw materials required and the destination of the pilot productions.
It also is recommended to increase the batch size only when the previous test has given satisfactory results. During these tests, a series of intermediate checks must be carried out for variables such as appearance, homogeneity, transparency, viscosity, aggregates, etc., at increasing times to better understand the temporal elements.
Mixing, dissolving and dispersing: The key to controlling these variables is understanding the correct time scale for adequate mixing, dissolving and/or dispersing. Generally, the most appropriate strategy is for the addition of each subsequent ingredient to the main batch to be aided by the composition of the premixed mixture. For example, to dissolve allantoin quickly, it is best to add this ingredient to water without any prior addition of glycerin or propylene glycol, since allantoin is less soluble in these premixes than in pure water.
Unfortunately, the addition of hydrotropes or alcohol dramatically decreases its solubility. The process also requires some time and frequently takes place in the final packaging in warehouses, especially at low winter temperatures.
Effects of pH: Another interesting case is the industrial dispersion of hydroxyethylcellulose, which occurs more easily in slightly alkaline aqueous solutions than in neutral water. To achieve complete swelling of this dispersion, it would subsequently become slightly acidic. By selecting the order of addition of acidic or alkaline ingredients to the formula, the most suitable environment can be created.
Thickening: The subsequent addition of ingredients also must be such as to avoid excessive thickening of the system. This is critical during the industrial process of preparing, e.g., a shampoo or shower gel; if thickening occurs in the final stages, this helps to avoid the excessive incorporation of air. Furthermore, the fluidity of the additive must be comparable with that of the premix to which it is added to avoid a laminar flow of the two liquids without adequate incorporation of one fluid into the other.
Solubility: Ingredients that are difficult to dissolve into a preformed blend of ingredients should be pre-dissolved in one of the raw materials where they have their maximum solubility. Similia similibus solvuntur (like dissolves like), in other words the polarity of the solvent must be compatible with that of the solute.
Of course, acidic (or hidden acidic) materials will dissolve easily in alkaline (or hidden alkaline, e.g., panthenol) mediums. For instance, parabens that are weak acids for their phenolic structure dissolve more easily in TEA or in panthenol without the need of heating the water phase. Similarly, they could be dissolved in the oil phase when heated before the preparation of emulsions. The successive homogenization with water will partition them into two phases.
Polar fluid ingredients like glycols, phenoxyethanol and many perfume ingredients are exceptional solvents for sparingly soluble organic ingredients. Frequently, the issue for difficult ingredients is not their absolute solubility, but the time necessary for their dissolution. An example of this time constraint is in the manufacturing of shampoos and bath foam.
The impact of salt and salt curve: In most shampoo and bath foam product recipes, surfactants are used that contain variable amounts of salts, mainly NaCl. Salts influence the viscosity of the final formula and are generally added in limited amounts (to avoid precipitations at cold temperature, the insolubilization of perfumes, or the takeover of the concentration where any further addition provides a sudden drop of the viscosity) to reach the required viscosity.
To keep such variability under control, the best strategy is to analyze the salt content in each surfactant raw material received. If this is not practically feasible, a graph should be prepared with a pilot batch, interconnecting the salt content of the blend with product viscosity, progressively adding 0.1% portions of NaCl and measuring the viscosity values after each addition. This curve will be a helpful tool for correcting industrial runs.
Moreover, the addition of the salt as a solid requires long mixing times (as noted previously) and proper agitation, as solid crystals may deposit easily at the bottom of the mixer, where fluid motions are slow or scarcely efficient. To avoid these inconveniences, most of the NaCl theoretically necessary should be added at the early phases of the manufacturing process, unless this could induce extremely high viscosity.
Final viscosity corrections: The final correction of viscosity values should be made with a saturated solution of NaCl prepared in advance. Such a premix solution does not require preservatives and can be stored for a long time. Its addition to the bulk is easy and quick – contrary to what happens when solid salt crystals are added to the viscous blend; in this case the dissolution is frequently problematic.
Notably, during production, the preparation of the premix phase, in general, should be reduced to a minimum, and if possible, avoided. Moreover, the volume of a premix usually should not exceed 2-5% of the bulk volume for its safe handling.
Premix considerations: Preliminary or extemporary premixes often are prepared as a time-saving measure. They are necessary when a dissolution process requires high temperatures; for example, working with a solution of a blend of waxes at a high temperature, which is a slow process. This can be mediated with the help of some fluid ingredients that work both as temperature transporters and solvents for big blocks of waxes.
Dissolution with the help of temperature additionally requires the evaluation of successive process phases. One also must avoid incorporating a hot phase into a cold blend so as not to cause precipitation or clouding.
Another case where a premix is considered necessary is with an expensive ingredient, to ensure that waste is reduced to a minimum. This is achieved by carefully preparing a concentrated solution instead of adding it into the main mixer.
Premix preparation is also necessary to dilute alkali or acids and avoid a strong pH impact when adding them to the main mixer. This could lead to the temporary formation of cloudiness or precipitation.
Drawing comparisons: Finally, when differences are observed between the approved prototype and first pilot batches, an investigation must be initiated to understand them. All manufacturing variables could be responsible for differences but most frequently, the key factors are:
- The incomplete swelling of polymers;
- Insufficient homogenization time/energy;
- Too low an emulsification temperature;
- Deaeration (the bench samples usually much air);
- Raw material variations/specifications;
- Inadequate cleaning of mixer/tools; or
- Evaporation of solvents.
Conclusion
Creating a quality finished product requires investments in time and money. The ability to maintain a high-quality formula throughout processing and scale-up is possible – but considering the complexity of the cosmetic product, it takes the consideration of numerous variables and intervention of different professionals to define the formula’s boundaries and actively collaborate to achieve the set objectives.
References
1. Lin, J. (2010). Manufacturing cosmetic emulsions: Pragmatic troubleshooting and energy conservation. Allured Books. Available at https://books.google.com/books/about/Manufacturing_Cosmetic_Emulsions.html?id=tdo0QwAACAAJ
2. Oyama, S. (2022). History and DNA with sustainability and its future. IFSCC Magazine. Available at https://ifscc.org/magazines/volume-25-no-4/
3. Gilbert, L. et al., (2022). Holistic sustainability. IFSCC Magazine. Available at https://ifscc.org/publications/library/ifscc-magazine/